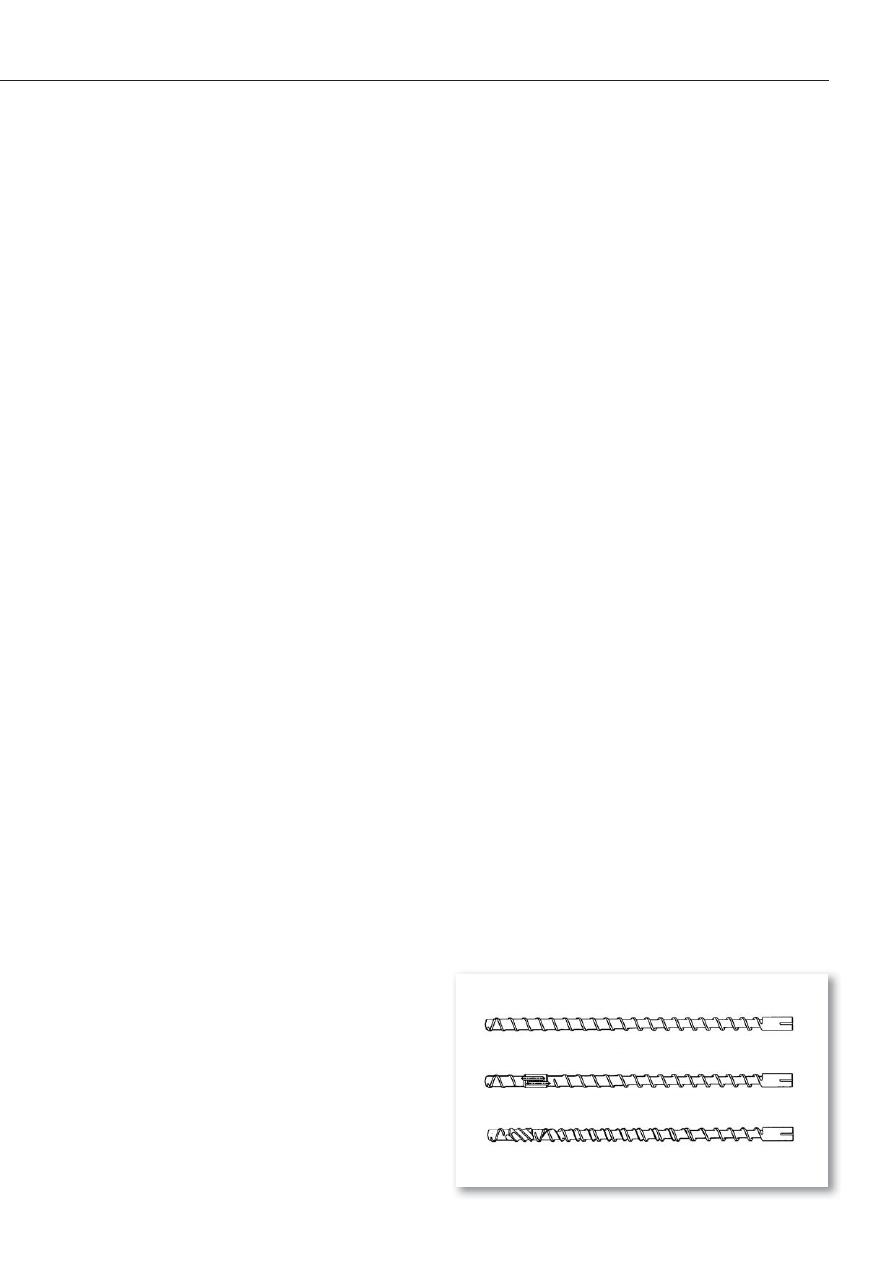
«КАБЕЛЬ-news», № 9, 2010
27
Производство
ÎÁÎÐÓÄÎÂÀÍÈÅ
К
экструдерам, применяемым для нанесения
покрытий на провода, часто предъявляется
требование перерабатывать несколько типов
полимеров и/или одинаково работать в различных
эксплуатационных режимах. Выбор соответству-
ющего типа шнека для оптимального удовлетворе-
ния комплексу требований является весьма важ-
ным шагом для оптимизации качества продукции и
снижения издержек производства. За многие годы
конструкции шнеков изменялись, и сегодня широко
применяются в основном шнеки барьерного типа.
Однако в некоторых случаях и другие, более про-
стые конструкции, разработанные ранее, могут эф-
фективно использоваться.
В этой статье обсуждаются характеристики шне-
ков и экструдеров для современных технологиче-
ских процессов изготовления проводов и кабелей
разнообразного назначения.
ДОЗИРУЮЩИЕ ШНЕКИ
Раньше конструктивно шнек представлял собой
дозирующий винт, который достаточно хорошо обе-
спечивал переработку некоторых полимеров, одна-
ко с меньшей производительностью по сравнению с
современными экструдерами, перерабатывающими
различные полимеры (рис. 1, верхняя конструкция).
Со временем дозирующие шнеки видоизменя-
лись, увеличивалась их прозводительность. В основ-
ном этот процесс носил характер проб и ошибок —
испытывались и сравнивались шнеки с различными
глубиной канала и длинами секций. Некоторые типы
материалов с высоким уровнем наполнения хорошо
перерабатывались с помощью дозирующих шнеков с
глубоким каналом. Полупроводящий полиэтилен (PE)
с поперечным сшиванием (XLPE) до сих пор пере-
Âûáîð øíåêîâ
è êîíñòðóêöèé
ýêñòðóäåðîâ äëÿ
íàíåñåíèÿ ïîêðûòèé
Эдвард СТЮАРД,
директор по технологии обработки компании Kuhne Corp., Ashaway, Rhode Island, USA
рабатывается шнеками этого типа. В переработке
непроводящих материалов типа XLPE, а также мате-
риалов с небольшой степенью наполнения добавка-
ми, с помощью дозирующих шнеков были достигнуты
пределы эффективности. Ее дальнейшее повышение
стало возможным путем добавления смесительных
секций (рис. 1, средняя часть), которые первоначаль-
но представляли собой ряды штырей, перекрываю-
щих до 50% поперечного сечения канала.
СМЕСИТЕЛЬНЫЕ ШНЕКИ
Для смешения используется конструкция смеси-
тельного шнека Мэддока. В этом случае весь ма-
териал при переработке принудительно проходит
через небольшие зазоры. Штыревые смесительные
секции, как выяснилось впоследствии, не обеспечи-
вают такого хорошего прохождения потока расплав-
ленного материала, как это наблюдается при ис-
пользовании смесителя Мэддока. Эта конструкция
со временем также подверглась усовершенствова-
ниям по сравнению с миксером, имеющим осевую
Рис. 1. Три основные конструкции шнеков
ДОЗИРУЮЩИЙ ШНЕК
СМЕСИТЕЛЬНЫЙ ШНЕК МЭДДОКА
БАРЬЕРНЫЙ/СМЕСИТЕЛЬНЫЙ ШНЕК
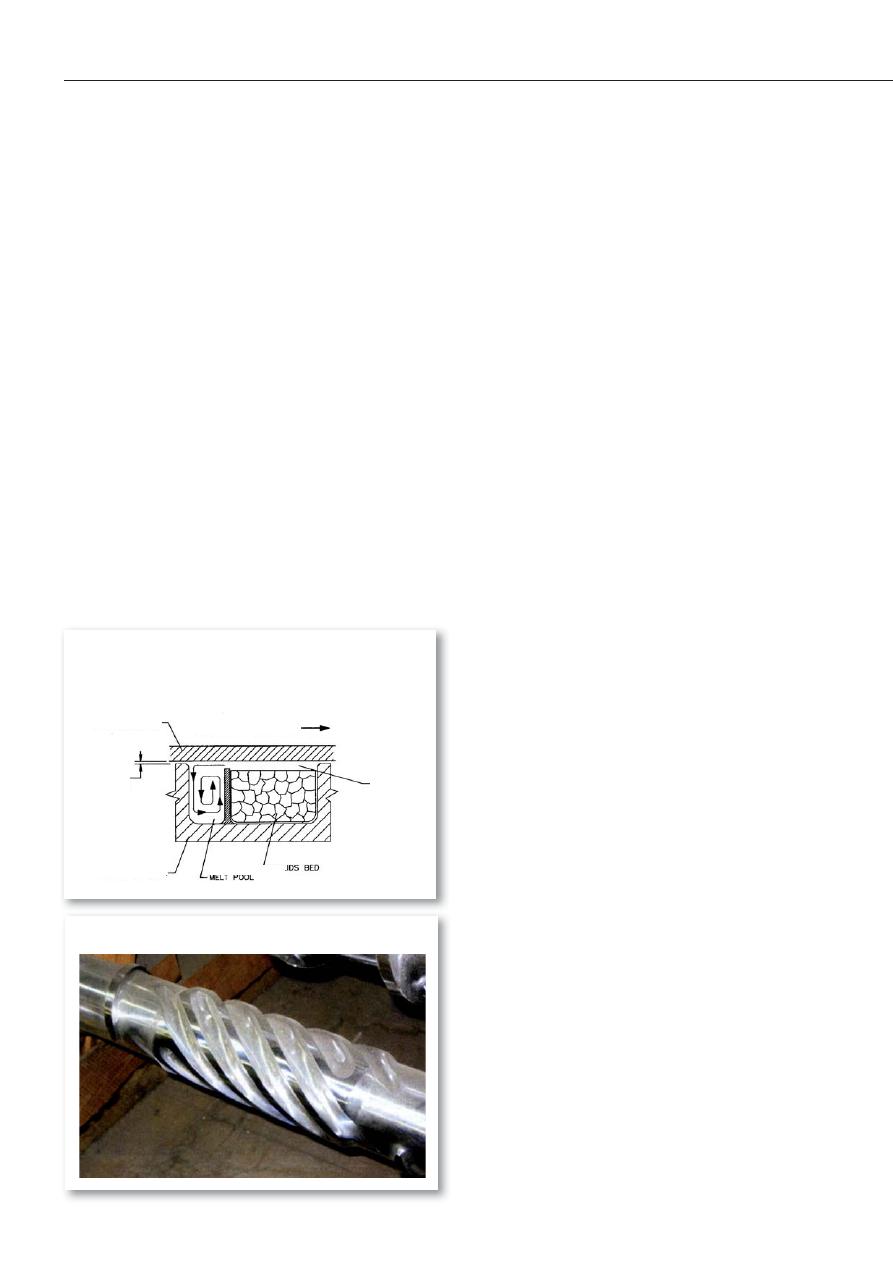
«КАБЕЛЬ-news», № 9, 2010
28
ориентацию канавки. В современных смесителях
часто используется спиральная ориентация канала,
и его контуры по глубине сделаны таким образом,
чтобы улучшить протекание материала на их концах
по сравнению с устаревшими более глубокими ка-
налами. Смесители с хорошим протеканием потока
расплавленного материала используются для пере-
работки XLPE, PVC (поливинилхлорид) и других по-
лимеров. Протекающий через смесительную часть
поток материала изменяет свой цвет (рис. 3).
Добавление смесительной секции позволило сде-
лать дозирующие шнеки с более глубокими канавка-
ми и тем самым повысить производительность при
заданной скорости вращения. Увеличение сопро-
тивления продавливанию и зазора между шнеком и
цилиндром экструдера в смесительной части долж-
но приводить к увеличению температуры расплава
по сравнению со шнеком без смесительной секции.
Если углубить каналы шнека и сохранить качество
расплавленного материала за счет дополнительных
затрат энергии, то шнек со смесителем обеспечит по-
вышение производительности при более низкой ско-
рости вращения. Скорость вращения шнека является
Производство
ÎÁÎÐÓÄÎÂÀÍÈÅ
параметром, который в наибольшей степени влияет
на температуру расплава. Сравнение производитель-
ности при заданной температуре расплава указывает
на выбор шнека со смесительной секцией, поскольку
такая конструкция дает возможность использовать
более глубокие каналы и меньшую скорость враще-
ния. Шнеки со смесительными секциями особенно
хорошо подходят для использования в технологиче-
ских процессах (переработка поливинилхлорида, по-
лиэтилена FPVC, PE и т.д.), в которых допускается
работа шнеков на повышенных скоростях. Более вы-
сокие скорости дают больше возможности для под-
держания качества расплавленного материала, когда
каналы шнека имеют увеличенную глубину для мак-
симизации производительности.
БАРЬЕРНЫЕ ШНЕКИ
Конструкция барьерных шнеков (рис. 1, нижняя
часть) обеспечивает лучшее продавливание рас-
плавленного материала и возможность дальнейше-
го увеличения глубины каналов, если используется
смесительная секция. При повышенных скоростях
вращения шнека стабильность продавливания рас-
плавленного материала обычно уменьшается при
применении дозирующих шнеков, а при использо-
вании барьерных повышается эффективность плав-
ления и улучшается продавливание расплава. Если
барьерный шнек сконструирован специально для
определенного полимера и конкретного технологи-
ческого процесса, твердые куски (гранулы) материа-
ла могут удерживаться в одном канале, а плавление
будет происходить в другом (рис. 2).
Высокопроизводительные барьерные шнеки, как
правило, имеют смесительные секции. Только в тех
случаях, если не требуется высокая производитель-
ность и возможны неглубокие канавки, смеситель не
нужен. Барьерная секция проектируется таким об-
разом, чтобы можно было управлять стабильностью
продавливания экструдера, а смеситель не влиял
бы на стабильность давления в конце его цилиндра.
В течение многих лет на рынке предлагалось мно-
жество конструкций экструдерных шнеков, но опти-
мальным выбором является шнек барьерного типа в
сочетании с обтекаемой и компактной смесительной
секцией. Смеситель обычно имеет длину, равную
двум диаметрам шнека. Более того, он должен быть
спроектирован так, чтобы зазор между витками
шнека и цилиндром экструдера имел минимальную
величину для обеспечения хорошего качества рас-
плава и смешения.
ПОЛИВИНИЛХЛОРИД (PVC)
При производстве проводов могут использовать-
ся различные типы поливинилхлорида — от мягкого
до полужесткого. Для более мягкого PVC необходим
Рис. 3. Типовой экструдерный шнек
Рис. 2. Внутренний вид смесительного
элемента одношнекового экструдера
СХЕМА РАСПЛАВЛЕНИЯ МАТЕРИАЛА В ОДНОШНЕКОВОМ
ЭКСТРУДЕРЕ
НАГРЕТЫЙ ЦИЛИНДР
НАПРАВЛЕНИЕ ЭКСТРУЗИИ
КАНАЛ ШНЕКА
ЗАГРУ-
ЖЕННОЕ
СЫРЬЕ
КАМЕРА С РАСПЛАВОМ
ЗАЗОР МЕЖДУ
ШНЕКОМ
И ЦИЛИНДРОМ
ПЛЕНКА
РАСПЛАВА
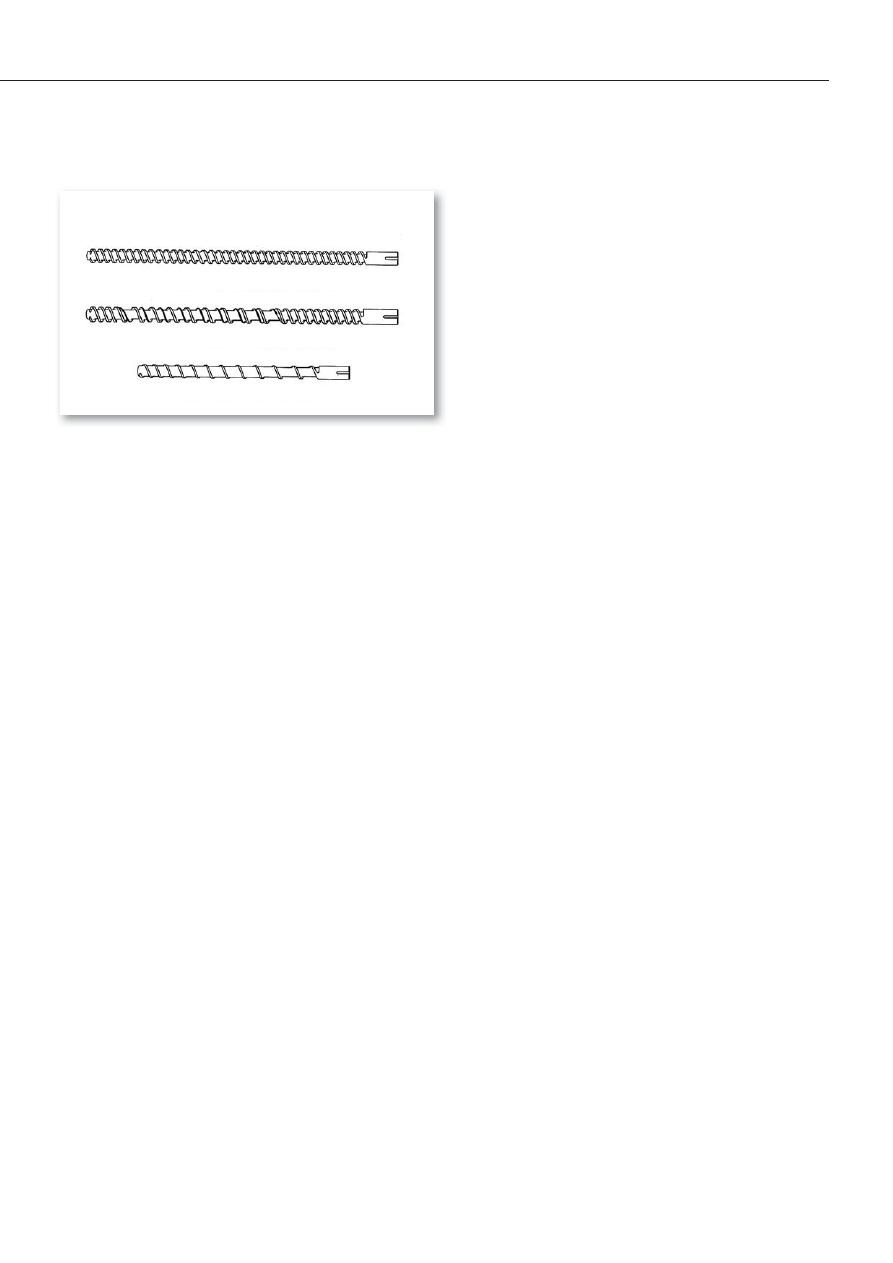
«КАБЕЛЬ-news», № 9, 2010
29
шнек с менее глубокими каналами и смеситель с
большим зазором между вершиной витка и цилин-
дром экструдера или с барьерной секцией для обе-
спечения полного выхода расплавленного материа-
ла из экструдера. В базовой конструкции шнеков
(дозирующего типа) первоначально по всей длине
винта делались сквозные отверстия. Для обеспече-
ния полного расплавления полимерного материала
при умеренных скоростях вращения шнека исполь-
зовалось его принудительное охлаждение (посред-
ством циркуляции воды внутри винта). Без водяно-
го охлаждения старые дозирующие шнеки не могут
обеспечить полное расплавление ПВХ, при этом
экструдат может содержать комки и /или он будет
плохо перемешан. Использование смесительной
секции и изменение конструкции шнека позволили
отказаться от водяного охлаждения, что привело к
повышению производительности. Система водяного
охлаждения внутри шнека требовала техническо-
го обслуживания, и ее использование приводило
к снижению продавливающей способности шнека
на величину до 50% по сравнению с неохлажда-
емым шнеком. В настоящее время шнеки с водяным
охлаждением редко используются, в основном при-
меняют смесительные шнеки или шнеки типа барь-
ерный/смесительный.
Цилиндры экструдеров обычно охлаждаются
воздухом, при диаметре шнека 3,5 или 4,5 дюйма;
в больших установках используются шнеки диаме-
тром 6 дюймов или более — в таких случаях исполь-
зуется водяное охлаждение. В целом, применение
водяного охлаждения в больших машинах является
вполне оправданным. При любой возможности ис-
пользуется водяное охлаждение из-за простоты и
удобства техобслуживания. Шнеки обычно изготав-
ливаются из высококачественной стали (например
AISI 4140), и витки, как правило, упрочняются на-
плавлением из материала, выбранного для внутрен-
него покрытия цилиндра экструдера. Материалы, из
которых изготавливаются цилиндры и шнеки, часто
содержат карбид вольфрама для обеспечения боль-
шего срока службы при использовании их для пере-
работки материалов типа PVC с наполнителями в
процессе нанесения покрытий на провода. В боль-
шинстве установок для переработки PVC использу-
ются экструдеры с отношением длина/диаметр 24:1,
шнеками диаметром 4,5 дюйма и моторы мощно-
стью от 150 до 200 л.с. с максимальной скоростью
вращения шнека 100 об/мин.
ПОЛИЭТИЛЕН (РЕ)
К полиэтилену относится большое семейство
продуктов, включающее LDPE, MDPE, HDPE (по-
лиэтилен низкой, средней и высокой плотности
соответственно) и MPEs (группа металлоценовых
полиэтиленов). Эти материалы перерабатывались
шнеками различных типов — от дозирующих до
смесительных, а в настоящее время перерабаты-
ваются шнеками барьерного/смесительного типов.
Дозирующие шнеки использовались без водяного
охлаждения, поскольку при переработке ПЭ с во-
дяным охлаждением не достигались такие же поло-
жительные результаты, как при переработке PVC. В
течение продолжительного времени предпочтение
отдавалось шнекам дозирующего/смесительного
типов, но применение современных шнеков барьер-
ного/смесительного типов дает лучшие результаты
(если шнеки сконструированы надлежащим обра-
зом). Для переработки полиэтиленов (MD, HD, LLD,
многие типы mPE) необходимо использовать экс-
трудеры с малой величиной зазора между витками
шнека и цилиндром экструдера (с более глубокими
каналами), независимо от типа конструкции шнека.
В экструдере со шнеком диаметром 4,5 дюйма, при
отношении длины цилиндра экструдера к диаметру
шнека 24:1, может использоваться мотор мощно-
стью 150 л.с., который обеспечивает максималь-
ную скорость вращения шнека 100 об/мин. В то же
время для переработки полиэтиленов, обладающих
большей вязкостью, необходимы моторы мощно-
стью 200 или даже 250 л.с., обеспечивающие мак-
симальную скорость вращения шнека 100 об/мин.
При переработке PVC в экструдере должно исполь-
зоваться воздушное охлаждение, если диаметр
шнека — до 4,5 дюйма, или водяное охлаждение,
если диаметр шнека — 6 дюймов или более. Шнек
должен быть изготовлен из высококачественной
стали с наплавлением упрочняющего материала
на виток шнека для обеспечения требуемой изно-
соустойчивости. Для переработки HDPE исполь-
зуются разнообразные конструкции шнеков — от
подвергнутых закалке до шнеков, для упрочнения
которых использовалось наплавление различных,
устойчивых к истиранию, современных материа-
лов. Полиэтилены LLDPE и MDPE ведут себя по-
добно полиэтилену HDPE и перерабатываются по
Рис. 4. Три конструкции шнеков
для экструзии резины
ДВУХВИТКОВЫЙ ШНЕК
ШНЕК С ПЕРЕМЕННЫМ ШАГОМ
БАРЬЕРНЫЙ ШНЕК ДЛЯ РЕЗИНЫ
Производство
ÎÁÎÐÓÄÎÂÀÍÈÅ

«КАБЕЛЬ-news», № 9, 2010
30
схожим сценариям. Семейство полиэтиленов mPE
отличается разнообразием степени вязкости, что
требует тщательного выбора конструкции шне-
ков для каждого конкретного случая. В некоторых
случаях используется достаточно большой момент
кручения, что приводит к нестабильности распла-
ва вдоль шнека. Для переработки таких материа-
лов необходимо выбирать шнеки барьерного типа
с таким расположением барьерной секции, при ко-
тором предотвращается раннее возникновение не-
стабильностей расплава.
ПОЛИПРОПИЛЕН (РР)
Переработка полипропилена осуществляется
с меньшей эффективностью по сравнению с по-
лиэтиленом. Эффективность загрузки и плавления
ниже, что приводит к снижению производительности
до 40% по сравнению с полиэтиленом при том же
самом шнеке. Гомополимеры по сравнению с сопо-
лимерами перерабатываются немного хуже, но оба
типа материала характеризуются заметно меньшей
эффективностью экструзии по сравнению с поли-
этиленом. Экструдеры для переработки полипро-
пилена часто имеют большую длину, соответству-
ющую пропорции 24:1, поскольку производитель-
ность увеличивается почти линейно с увеличением
длины цилиндра экструдера. Экструдер 30:1 по срав-
нению с экструдером 24:1 обладает производитель-
ностью, большей примерно на 20—25%. Экструдер
30:1 будет обладать еще большей производитель-
ностью. Оптимальным типом шнека в этой ситуации
будет барьерный/смесительный шнек, который бу-
дет иметь отличия от шнеков для переработки поли-
этилена или поливинилхлорида в начальной барьер-
ной точке и в объеме канала для расплава. Раньше
использовались дозирующие шнеки, а в более позд-
нее время — шнеки смесительного типа (как и для
переработки полиэтилена).
НЕЙЛОН
К наиболее распространенным разновидностям
нейлона относятся nylon-6 и nylon-6/6. Для дости-
жения наибольшей производительности экструдера
определенного типа обе эти марки нейлона лучше
всего перерабатываются с помощью шнеков барьер-
ного/смесительного типов. При невысокой произво-
дительности можно использовать дозирующие шне-
ки или барьерные шнеки без смесительной секции.
При переработке вышеупомянутых марок нейлона
характеристики экструзии имеют небольшие раз-
личия, но можно сконструировать один шнек, при-
годный для переработки обеих марок нейлона неза-
висимо от того, какой именно тип шнека выбран. В
экструдерах для нейлона обычно используется воз-
душное охлаждение, даже в больших экструдерах,
поскольку применяются более высокотемператур-
ные режимы, а с помощью воздуха можно регулиро-
вать надлежащим образом температуру и в больших
экструдерах. Для изготовления шнеков и цилиндров
экструдеров используются такие же металлы, как
для переработки полиэтилена или поливинилхлори-
да. На конце экструдера для обеспечения нагрева
предпочтительно использовать зажимные кольца
или нагревательные фланцы, поскольку для ней-
лона характерна повышенная температура плавле-
ния. Целесообразно использовать короткую полость
в сердечнике (на три первых витка) на тот случай,
когда происходит сгущение расплава из-за недо-
статочности охлаждения в данном экструдере. Это
особенно важно в случаях замедления или остано-
вок во время работы линии, на которой изготавлива-
ется провод с покрытием. Охлаждение первых трех
витков шнека (они расположены в зоне загрузки) не
влияет на производительность, как это наблюдается
при охлаждении шнека по всей длине, но помогает
предотвратить преждевременное расплавление ней-
лона, который может налипать на основание шнека
и либо снизить производительность, либо привести
к полной остановке экструдера.
ФТОРПОЛИМЕРЫ
Это семейство материалов требует высоких тем-
ператур при переработке, при этом шнеки и цилин-
дры экструдеров должны быть изготовлены из кор-
розионноустойчивых материалов. Шнеки обычно
изготавливаются из сплавов Hastelloy или Inconel
с высоким содержанием никеля, и, как показала
практика, они обладают хорошей устойчивостью к
воздействию фторидов, которые должны удалять-
ся в процессе экструзии. Материалы, из которых
изготавливаются фильера и внутреннее покрытие
цилиндра экструдера, также должны содержать
много никеля. Охлаждение обычно воздушное, по
всей длине шнека. Для нагрева используются, как
правило, нагревательные элементы из другого ма-
териала. Обычно в экструдерах используются литые
алюминиевые нагреватели, которые не могут полно-
ценно работать во всем требуемом для переработки
фторполимеров диапазоне температур. Вместо них
целесообразно использовать бронзовые или кера-
мические нагреватели. Типы используемых шнеков —
дозирующие или дозирующие/смесительные. Как
правило, экструдеры работают с умеренной произ-
водительностью в соответствии с требованиями к
расплаву на выходе фильеры. При умеренной про-
изводительности и небольших скоростях вращения
шнека, как показала практика, дозирующие шнеки
обеспечивают достаточную стабильность продав-
ливания. Шнеки для фторполимеров не слишком
прочные, и поэтому существует необходимость про-
Производство
ÎÁÎÐÓÄÎÂÀÍÈÅ
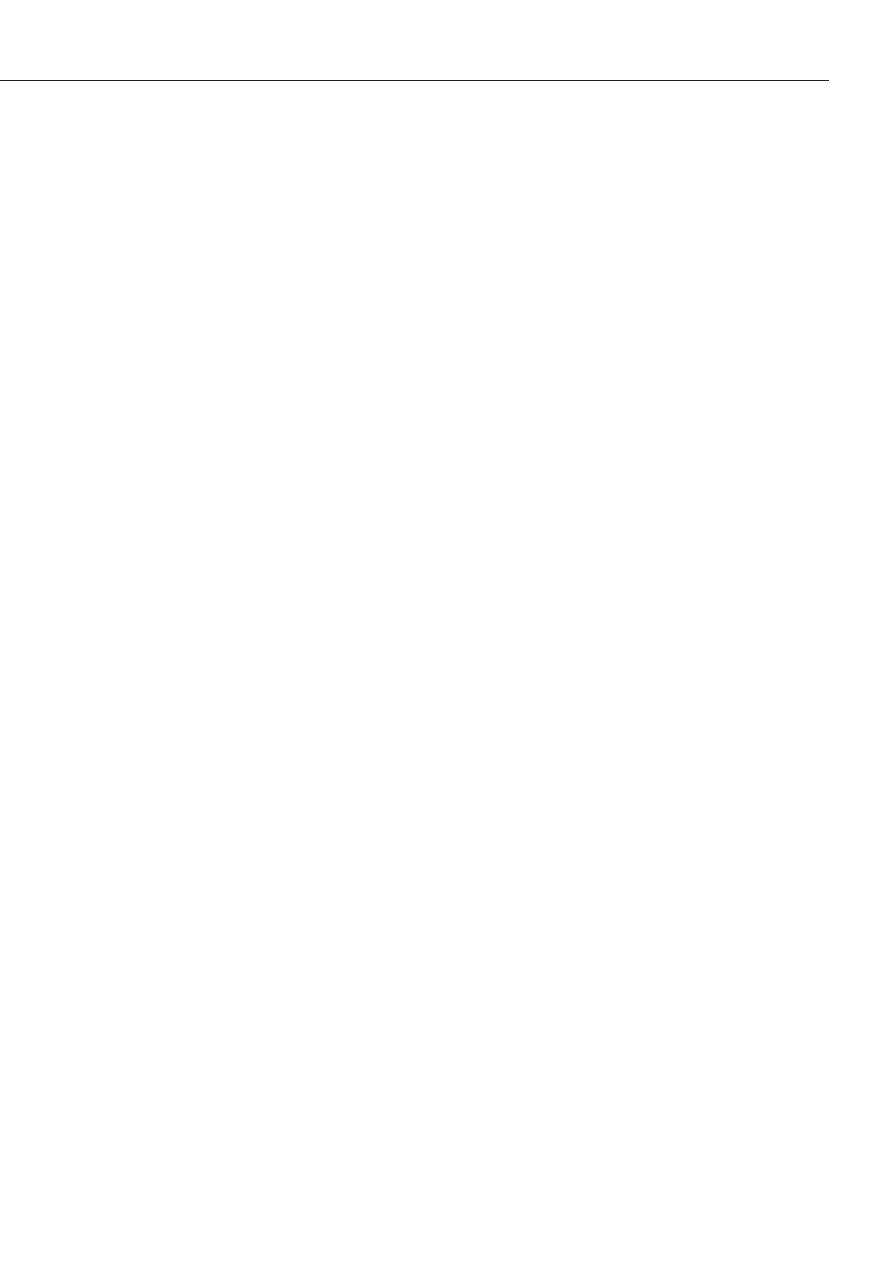
«КАБЕЛЬ-news», № 9, 2010
31
верять их способность выдерживать прилагаемые
вращательные усилия для того, чтобы минимизиро-
вать возможность поломки.
РЕЗИНА
К резинам относятся EPR, EPDM, натуральный
каучук и разнообразные многокомпонентные смеси.
Резины могут использоваться в гранулах, но чаще
всего в виде полосок. В последнем случае на экстру-
дере необходима специальная загрузочная секция и
приводной ролик для подачи резины на соответству-
ющую секцию шнека, которая имеет достаточно боль-
шую длину и удвоенную глубину канала. Шнеки —
или дозирующего типа с глубоким каналом или ба-
рьерного без смесительной секции. Барьерная сек-
ция не отделяет расплав от твердого материала, что
обычно для экструдеров, перерабатывающих поли-
меры, поскольку в действительности резина не пла-
вится. Резина размягчается под воздействием тепла
и энергии продавливания, а барьерная секция спо-
собствует приведению материала в однородное по
температуре состояние (она работает как зона по-
степенного смешения). Барьерный шнек уменьшает
влияние любой нестабильности процесса загрузки и
обеспечивает улучшение консистенции продавлива-
емого материала подобно тому, как это происходит в
зоне экструзии при переработке полимеров. При ра-
боте с гранулированной резиной нет необходимости
в загрузочных прокатных валках, но определенные
преимущества в этом случае можно получить, ис-
пользуя конструкцию шнеков с глубокими каналами
и небольшой величиной зазора между гребнем шне-
ка и цилиндром экструдера, как при загрузке резины
в виде полосок. В большей части экструдеров для
переработки резины используется водяное охлаж-
дение, поскольку рабочие температуры в цилиндре
экструдера достаточно низкие (150—200
о
F), а при
таких условиях эффективность воздушного охлаж-
дения невелика. Резина обычно имеет большую
вязкость, а в экструдере при этом необходимы боль-
шие крутящие усилия. Например, для 4,5-дюймово-
го экструдера требуется мотор мощностью 150 л.с.
при максимальной скорости вращения шнека
50 об/мин. Поскольку в действительности резина не
расплавляется, а ее природная большая вязкость
требует повышенных энергозатрат, в большинстве
машин для переработки резины используются бо-
лее короткие цилиндры экструдеров по сравнению
с переработкой пластиков. В типовом оборудовании
отношение длины цилиндра к диаметру шнека долж-
но быть 15:1 или 20:1, в то время как в машинах для
переработки пластиков это отношение равно 24:1
или 30:1. Шнек делается полым, а для регулирова-
ния его температуры используется горячая вода или
нагретое масло. При экструзии резины регулировка
температуры позволяет осуществлять управление
качеством экструдата.
Силикон относится к семейству резин, и при его
переработке используются еще более низкие тем-
пературы цилиндра экструдера (50—60
о
F). В этих
условиях для охлаждения шнека используется вода.
Сами шнеки, как правило, имеют конструкцию до-
зирующего типа, аналогичную конструкции двух-
витковых или одновитковых шнеков с уменьшенной
высотой витка, когда допустимо повышенное давле-
ние в фильере (рис 1, фиг. 1 и 3). Длина экструдеров
для переработки силикона еще меньше по сравне-
нию с переработкой резины и лежит в диапазоне
L/D=(8-12):1. Силикон обычно загружается в экстру-
дер в виде полосок, при этом, как правило, исполь-
зуются прокатные валки. В машинах ранних поколе-
ний прокатные валки не использовались, в то время
как эффективная прокатка исходного сырья облег-
чает процесс управления загрузкой и обеспечивает
повышенную управляемость стабильностью продав-
ливания перерабатываемого материала.
ПОЛИУРЕТАН
Уретаны различаются по величине твердости.
Это различие влияет на правильный выбор значения
зазора между вершиной витка шнека и цилиндром
экструдера, определяющего возможность полного
расплавления экструдата и получения гладкой по-
верхности материала на выходе. Многокомпонент-
ные уретаны характеризуются набором дюроме-
тров, из которого формируется конечный дюрометр,
что затрудняет работу шнека, поскольку необходи-
мо плавить и смешивать компоненты с различной
вязкостью. При переработке уретана часто трудно
обеспечить хорошую стабильность продавливания
расплавленной смеси. Проблемы преждевременно-
го расплавления, связанные с плавлением твердого
материала в зоне загрузки, являются характерными
и при переработке многих типов полиуретана. При
этом лучшим способом обеспечить хорошую ста-
бильность продавливания является использование
правильно сконструированного шнека барьерного
типа. Дозирующие шнеки должны иметь дозиру-
ющую секцию большой длины. Это обеспечивает хо-
рошую возможность достижения нужной стабильно-
сти продавливания за счет демпфирования имевших
место изменений давления продавливания. Однако
это не позволяет полностью исключить проблему не-
стабильности давления, в то время как с помощью
барьерного шнека эта проблема решается. Для пе-
реработки полиуретанов необходимы повышенные
крутящие моменты — от средних до высоких значе-
ний, в некоторых случаях как при переработке по-
лиэтиленов HDPE или LLDPE (линейный полиэтилен
низкой плотности).
Производство
ÎÁÎÐÓÄÎÂÀÍÈÅ
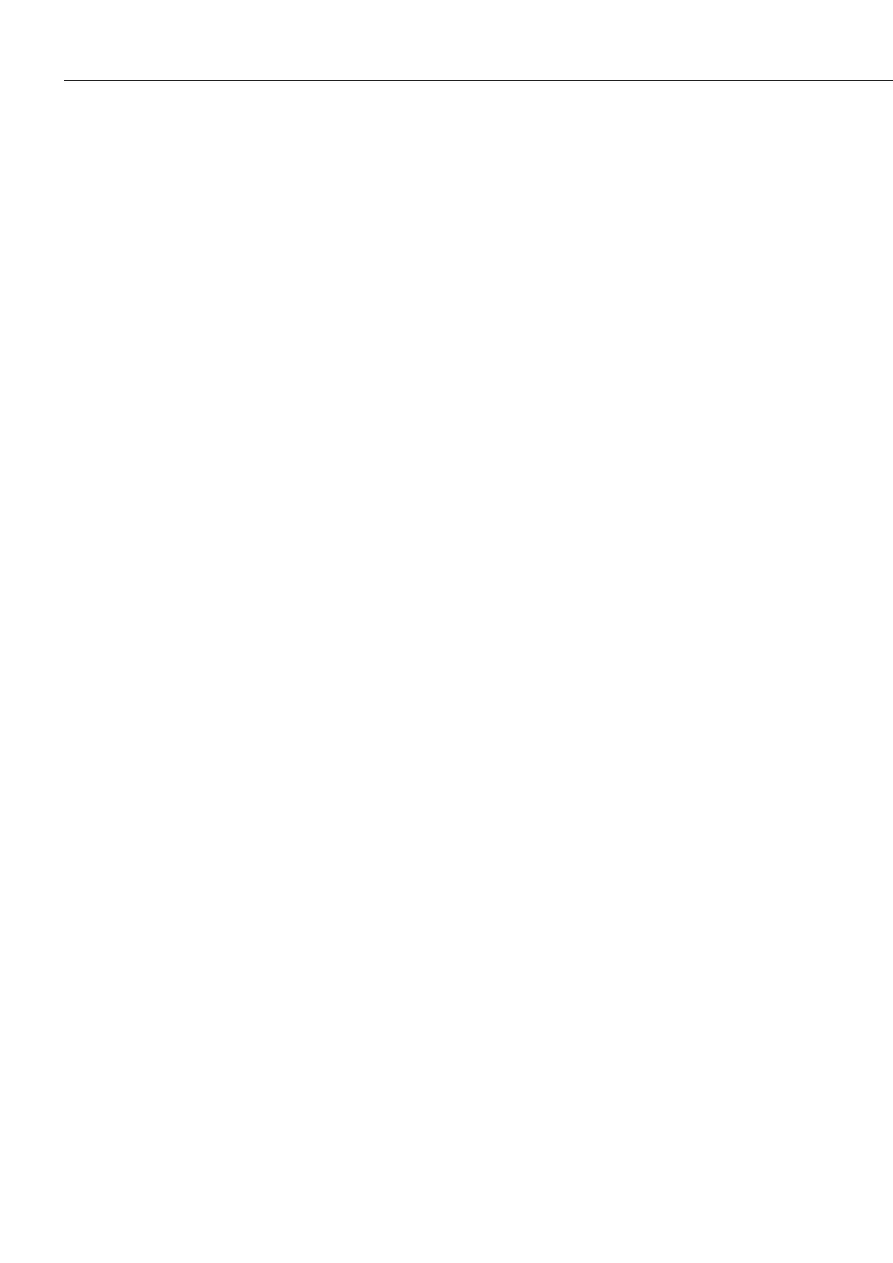
«КАБЕЛЬ-news», № 9, 2010
32
ТЕРМОПЛАСТИЧНЫЕ ЭЛАСТОМЕРЫ
(TPE ИЛИ TPR)
Если в основе этих материалов использован по-
липропилен, то выбор конструкции шнеков произво-
дится так же, как и при переработке полипропилена
(рассматривалось выше). Если основой ТРЕ являет-
ся полиэтилен, то при выборе типа шнека руковод-
ствуются соображениями, рассмотренными выше в
информации о полиэтилене. Поскольку существует
обширное семейство материалов с разными зна-
чениями вязкости, то для переработки конкретного
типа материала следует подбирать необходимое
значение величины зазора между вершиной витка
шнека и цилиндром экструдера.
ОГНЕСТОЙКИЕ КОМПАУНДЫ
При использовании огнестойких добавок и на-
полнителей следует тщательно подходить к выбору
типа шнека и учитывать необходимость упрочнения
как цилиндра экструдера, так и шнека. Как пра-
вило, необходимо использовать шнеки барьерно-
го/смесительного типа и обеспечить небольшой за-
зор между вершиной витка шнека и цилиндром экс-
трудера. Раньше использовались дозирующие или
дозирующие/смесительные шнеки с глубокими ка-
налами, которые вполне удовлетворительно работа-
ли на низких оборотах, что часто было единственной
возможностью из-за термочувствительности этих
материалов. Когда температура многих огнеупор-
ных материалов достигает 400
о
F, тепловая реакция
вызывает выделение газов. При этом в продукте на
выходе экструдера могут появляться пузырьки. Как
и для большинства материалов с высокой вязко-
стью, лучшим выбором типа шнека является шнек,
который обеспечивает минимальный зазор между
вершиной витка и цилиндром экструдера, величи-
на которого все еще позволяет получать хорошее
качество расплава. Типичной особенностью экстру-
деров, определяемой необходимостью переработ-
ки материалов с высокой абразивностью применя-
емых наполнителей, является использование упроч-
нения шнеков и цилиндров экструдера карбидом
вольфрама.
СШИТЫЙ ПОЛИЭТИЛЕН (XLPE)
Переработка этих материалов требует тщатель-
ного подхода к выбору шнеков для экструдеров. По-
лупроводящие материалы XLPE обычно перераба-
тываются с помощью дозирующих или дозиру-ющих/
смесительных шнеков, которые дают вполне удо-
влетворительные результаты с точки зрения обеспе-
чения необходимого качества расплава и устойчиво-
го режима его продавливания. Черные углеродные
добавки, обеспечивающие полупроводящие свой-
ства, облегчают процесс плавления за счет улуч-
шения теплоотдачи в полимер, продавлива-емый по
длине экструдера. Расплавление происходит ста-
бильно, что повышает производительность по срав-
нению с переработкой исходного ПЭ полимера.
Полупроводящие материалы XLPE обычно пере-
рабатываются в экструдерах с коротким цилиндром,
как правило, типоразмера 20:1 и реже 15:1 (отно-
шение L/D). Непроводящие материалы XLPE лучше
всего перерабатываются с помощью барьерных/
смесительных шнеков с отношением диаметра шне-
ка к длине цилиндра экструдера 24:1 при средних
или малых величинах зазора между витком шнека и
цилиндром экструдера. На витки шнека наплавляет-
ся упрочняющий материал, обычно упрочнение тре-
буется при экструзии HDPE или LLDPE.
При переработке нескольких полимеров с помо-
щью одного шнека необходимо тщательное рассмо-
трение особенностей экструдеров, предназначенных
для нанесения покрытия на провода. Лучше всего
для этой цели подходят современные барьерные
шнеки, но и в этом случае остаются ограничения при
расширении ряда перерабатываемых материалов.
Шнеки дозирующего типа также позволяют пере-
рабатывать разные материалы, но результаты экс-
трузии будут хуже, чем при использовании шнеков
барьерного типа. При принятии решения в процессе
выбора оптимальной конструкции шнека необходи-
мо рассматривать такие факторы, как типы перера-
батываемых полимеров, выходная производитель-
ность, требуемая эффективность продавливания и
необходимые величины давления на конце шнека.
ЗАКЛЮЧЕНИЕ
Поскольку невозможно выбрать одну-единст-
венную конструкцию шнека, которая подходила бы
для всех возможных случаев, опыт переработки
конкретного полимера дает возможность рекомен-
довать определенный тип шнека, который может
обеспечить выполнение требований к производи-
тельности экструдера и стабильности продавлива-
ния расплавленного материала.
Когда необходимо перерабатывать разные мате-
риалы с помощью одного шнека, следует установить
допустимые пределы ухудшения качества перера-
ботки материала для того, чтобы быть уверенным
в правильности сделанного выбора. При принятии
решения о выборе оптимальной конструкции шнека
необходимо принимать во внимание типы перераба-
тываемых полимеров, требуемую величину произво-
дительности, стабильность продавливания и прием-
лемое значение давления на конце шнека.
Журнал Wire Journal International, June 2009
Перевод — Святослав ЮРЬЕВ
Производство
ÎÁÎÐÓÄÎÂÀÍÈÅ
Оригинал статьи: Выбор шнеков и конструкций экструдеров для нанесения покрытий
К экструдерам, применяемым для нанесения покрытий на провода, часто предъявляется требование перерабатывать несколько типов полимеров и/или одинаково работать в различных эксплуатационных режимах. Выбор соответствующего типа шнека для оптимального удовлетворения комплексу требований является весьма важным шагом для оптимизации качества продукции и снижения издержек производства.