В 2022 году АО «ИНТЕРА» исполнилось 20 лет. Начав в 2002 году как дистрибьютор нескольких американских и европейских компаний, уже через три года мы разработали, изготовили и поставили на первый энергообъект систему мониторинга трансформаторного оборудования «СКУ». А еще через два года начали разработку приборов анализа газовлагосодержания трансформаторного масла, и было принято стратегическое решение заниматься исследованиями, разработкой и производством промышленного оборудования для энергетики.
Лаптев А.В., к.т.н., генеральный директор АО «ИНТЕРА»
Калашников С.В., начальник отдела ИТ АО «ИНТЕРА»
В год двадцатилетия компания имеет производственные площади, аттестованные лаборатории и все основания называть себя отечественным производителем, работающим над вопросами импортозамещения уже более 17 лет. Система мониторинга и приборы газового анализа производства АО «ИНТЕРА» внесены в государственный реестр средств измерений и поставляются не только на энергообъекты страны, но и за рубеж.
Опыт поставок и последующей эксплуатации на энергообъектах разного класса напряжения позволил накопить статистику и сформировать ассортиментный ряд оборудования, позволяющий обеспечить контроль необходимых параметров на объектах разного уровня ответственности с учетом экономической целесообразности приобретения системы мониторинга трансформаторов и первичных датчиков — приборов газового анализа. В последние годы мы предлагаем несколько вариантов комплексной поставки оборудования, совокупность которых мы условно назвали матрицей решений (таблица 1).
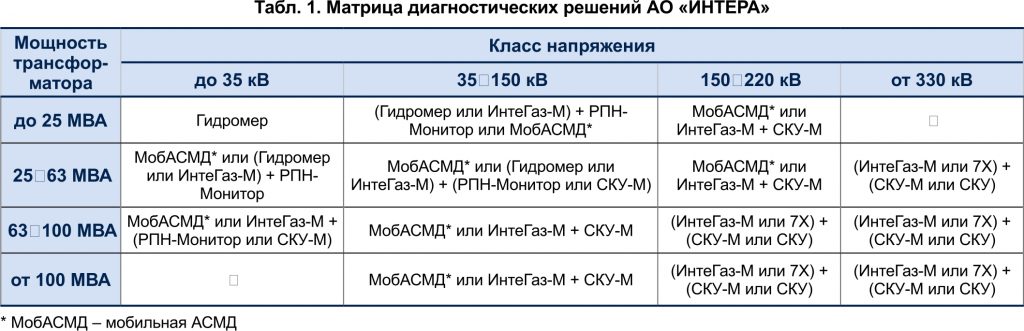
Важнейшее направление работы — постоянное совершенствование серийного оборудования и новые разработки. Меняются технологии, потребности заказчика, и мы это хорошо понимаем. Если сравнивать оборудование разных лет, то устройства, показанные в узлах матрицы, при сохранении их производственного наименования и общего функционального назначения меняются идеологически в среднем каждые два года. Элементная база не просто обновляется, идет постоянный и достаточно успешный поиск новых технологий и решений, повышается надежность, растет объем применения компонентов и материалов, производимых в России и дружественных странах.
К настоящему моменту на энергообъекты поставлено более 900 единиц промышленных анализаторов газовлагосодержания трансформаторного масла «ИнтеГаз» и хроматографов «7Х». Исследование методов извлечения газов и анализа газовлагосодержания ведется постоянно. Мы продолжаем развивать и модернизировать оборудование, базирующееся на хроматографическом методе измерений, однако параллельно активно инвестируем собственные средства в исследование и разработку приборов на совершенно новых технологиях и видим в них перспективу дальнейшего развития.
Санкции несколько затормозили работу, но, сделав недоступными западные технологии, активизировали поиск аналогов — мы ищем и находим разработчиков и исследователей у нас. Пока изделия не настолько законченные и проверенные, как западные образцы, но можно уверенно сказать, что есть база для разработки новых приборов с применением лазерных технологий.
На первых порах использование этих устройств будет в разы дороже, чем применение хроматографического метода и не для всех объектов их применение технически и экономически оправдано, однако мы рассчитываем на постепенное удешевление и самих технологий и конечного продукта.
Кризис электроники развивался независимо от санкций и достаточно длительное время. Причиной называли пандемию, сбои в поставках кремния, пожары на ряде заводов по производству микросхем. Однако мы почувствовали кризис иначе — появилось большое количество контрафактных микросхем. Доходило до того, что партии поставленных отечественными компаниями микросхем были нерабочими. Цены на микросхемы взлетели, и поставщики не давали гарантии не только на качество поставляемых изделий, но даже на сам факт поставки.
Такая ситуация потребовала полностью переделать схемотехнику приборов, взяв за основу модульную систему, позволяющую решать многие задачи ограниченными мощностями процессора. Процессоры были выбраны самые доступные, но они не стали от этого менее надежными. Каждый процессор решает свои задачи, и нагрузка на центральный процессор уменьшилась, его ресурсы освободились для задач связи. В некоторых случаях замена внесла коррективы в работу приборов, что положительно сказалось на их функционировании. Например, применение модульной системы позволило унифицировать блоки, упростить диагностику, наладку и калибровку, техническое обслуживание и обеспечить возможность оперативного устранения неполадок на объекте просто заменой блока.
В процессе исследований по-новому посмотрели на проблему отбора и анализа пробы, и появились новые, неожиданно интересные решения, позволяющие уменьшить погрешность измерений. Применение этих решений было подготовлено более глубоким знанием проблем эксплуатации, наличием исследовательского опыта, которых не было в начале работы. Например, был существенно модернизирован анализатор «ИнтеГаз». В ближайшее время появятся новые версии газоанализаторов Гидромер и хроматографа «7Х». Ожидается, что они станут дешевле с одновременным расширением функционала. У них появится новый интерфейс на базе протоколов МЭК 61850 и/или МЭК 608705-104. Судя по лабораторным испытаниям, должна повыситься стабильность работы и уровень самодиагностики.
Применение протокола МЭК 61850 и/или МЭК 60870-5-104 станет в дальнейшем стандартом для всех изделий компании. Это позволит применять их как в составе других систем, так и самостоятельно.
На однокристальных микроконтроллерах выпущены первые образцы нового оборудования, которое станет коробочным продуктом, удобным в настройке, интуитивно понятным и более дешевым, нежели оборудование на промышленных контроллерах.
Контроль вводов «КИВ-МК», где реализованы следующие функциональные возможности:
- измерение токов утечки основной изоляции вводов;
- измерение фазного напряжения;
- расчет tgδ и Δtgδ;
- расчет С1 и ΔС1;
- расчет тока и фазы вектора небаланса;
- контроль температуры окружающей среды;
- контроль обрыва каналов измерения тока и напряжения;
- формирование релейной и световой сигнализации (аварийной и предупредительной) при выходе значений контролируемых параметров за значения заданных уставок;
- накопление данных и хранение истории в энергонезависимой памяти прибора;
- передача данных в системы верхнего уровня и сеть заказчика по стандартным цифровым интерфейсам (Ethernet 10/100 BASE-ТХ — протокол Modbus TCP; RS-485 — протокол Modbus RTU);
- синхронизация «КИВ-МК» с системой единого времени энергообъекта по протоколу NTP.
Управление системой охлаждения трансформатора «БУС-МК», где реализованы следующие функциональные возможности:
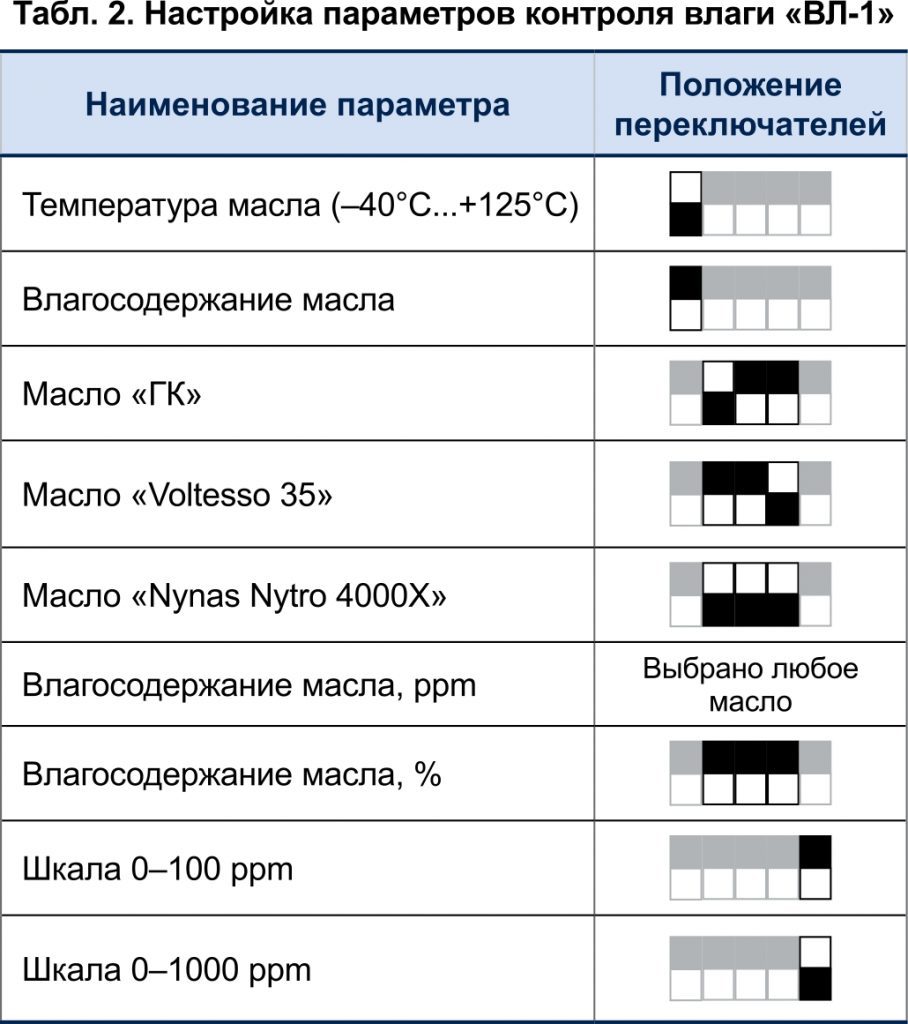
- измерение температуры верхних слоев масла;
- измерение температуры наиболее нагретой точки стороны высшего напряжения / тока стороны высшего напряжения;
- измерение температуры наиболее нагретой точки стороны среднего напряжения / тока стороныт среднего напряжения / тока стороны низшего напряжения при расщепленной обмотке / тока общей обмотки;
- измерение температуры наиболее нагретой точки стороны низшего напряжения / тока стороны низшего напряжения;
- измерение температуры окружающей среды;
- автоматическое управление системой охлаждения (М, Д, ДЦ), позволяющее поддерживать тепловой режим трансформаторного оборудования в заданных пределах по сигналам датчиков температуры;
- принудительный запуск ступеней охлаждения по сигналу с дискретных входов;
- контроль температуры в корпусе прибора;
- управление обогревом шкафа;
- накопление данных и хранение истории в энергонезависимой памяти прибора;
- передача данных в системы верхнего уровня по стандартному цифровому интерфейсу RS-485 (протокол Modbus RTU).
Контроль влаги в масле «ВЛ-1» стоит отдельно в этом ряду. Он не требует питания и имеет токовый выход, по которому передаются показатели либо влаги, либо температуры. Настройка выполняется в соответствии с переключателями, находящимися под крышкой. Пример настройки приведен в таблице 2.
Контроль РПН «РПН-МК». Структурная схема приведена на рисунке 1. Есть несколько дискретных и аналоговых входов, дискретные выходы по уровням аварии. Две линии цифрового интерфейса — Ethernet 10/100 BASE-TX с реализованными web-интерфейсами и протоколом Modbus TCP (опционально МЭК 61850 и/или МЭК 60870-5-104) и RS-485 с протоколом Modbus RTU.
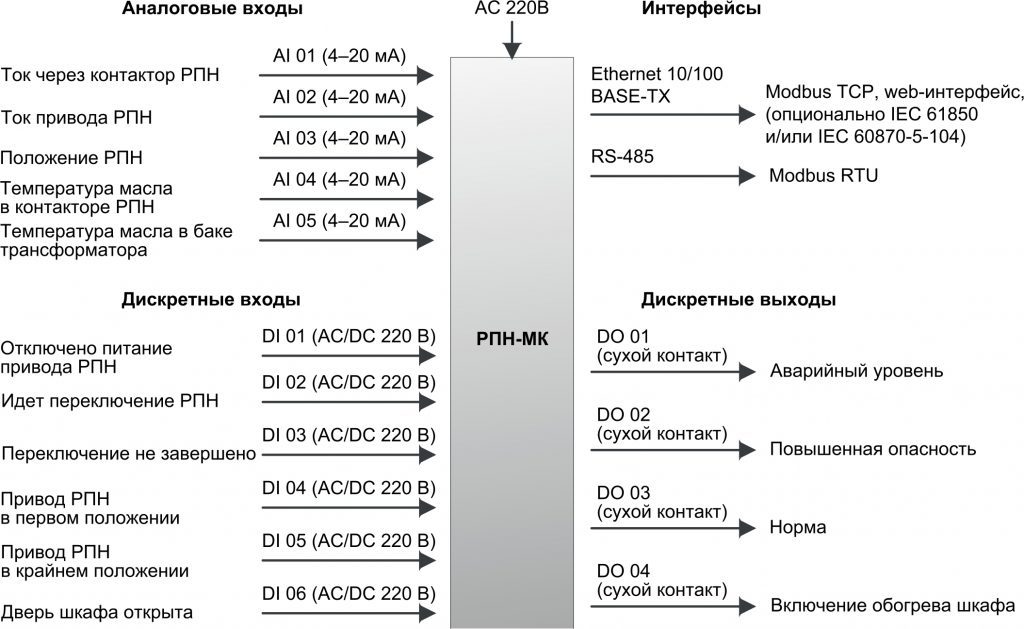
Удаленный доступ к диагностической информации при помощи web-интерфейса. Синхронизация «РПН-МК» с системой единого времени энергообъекта по протоколу NTP. Технические характеристики приведены в таблице 3.
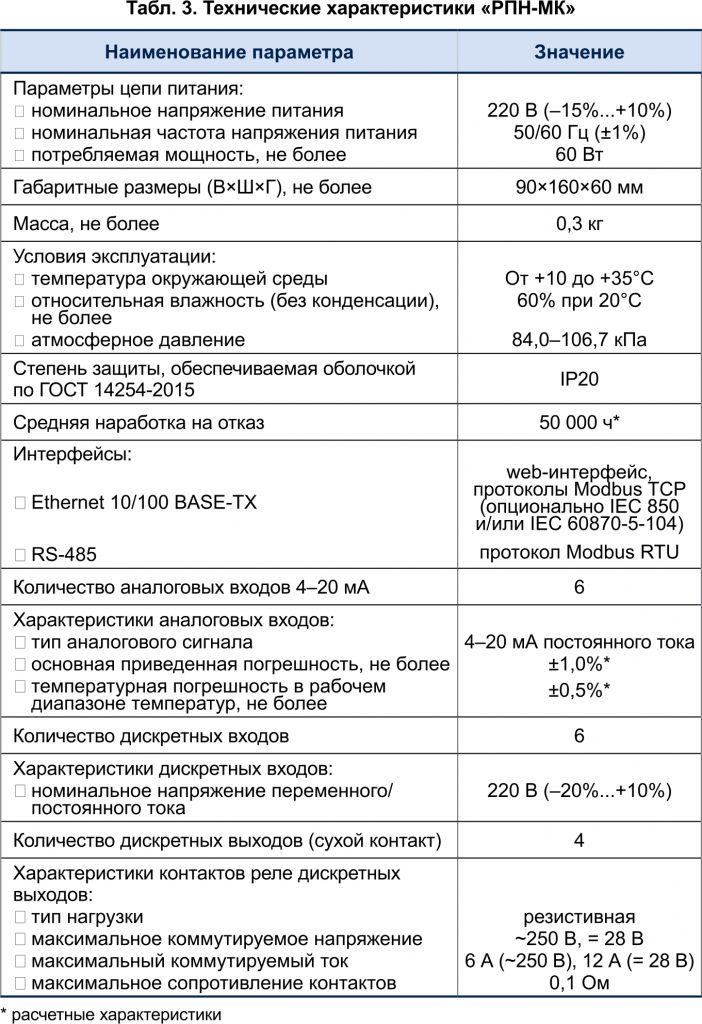
В «РПН-МК» реализованы следующие функциональные возможности:
- непрерывный контроль технических характеристик РПН (питания привода РПН; текущего номера положения РПН; температуры масла в баке контактора РПН, температуры верхних слоев масла в баке трансформатора; температуры в корпусе прибора; тока, протекающего через РПН; тока/мощности, потребляемого приводом РПН; переключения РПН и его завершения; доступа в шкаф привода РПН; обогрева шкафа привода РПН);
- формирование релейной и световой сигнализации (аварийной и предупредительной) при выходе значений контролируемых параметров устройства РПН за значения заданных уставок;
- анализ и обработка контролируемых параметров в режиме реального времени с предоставлением расчета перепада температур масла в баке трансформатора и баке контактора РПН, расчета механического момента переключения, учета времени работы РПН в каждом положении, учета количества переключений РПН (за день, месяц, год), длительности переключения РПН, расчета остаточного механического ресурса контактора РПН, расчета остаточного коммутационного ресурса контактора РПН, контроля ресурса замены масла в контакторе РПН, оповещения о необходимости проведения очередного технического обслуживания;
- накопление данных и хранение истории работы РПН в энергонезависимой памяти.
Пример web-интерфейса приведен на рисунке 2.
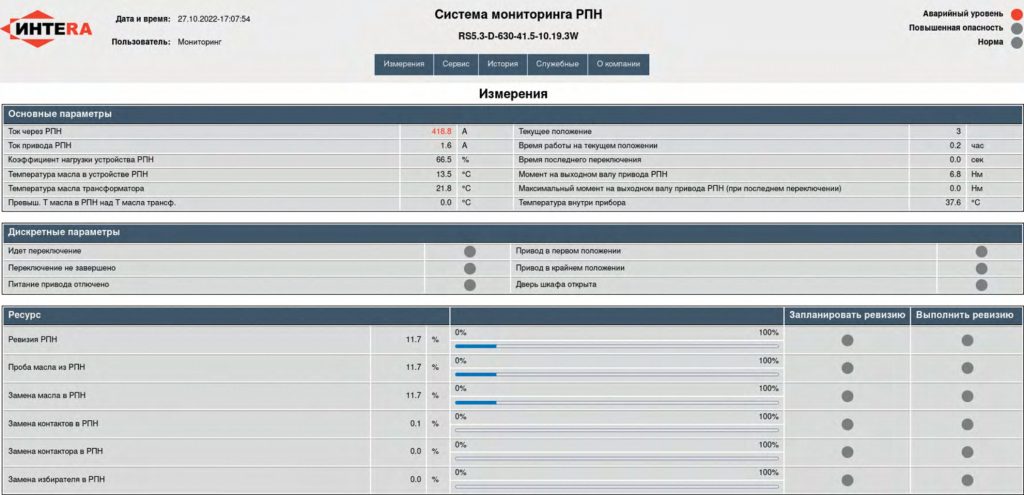
Использование однокристальных микроконтроллеров не ограничивается отдельными приборами и устройствами. На базе анализатора «ИнтеГаз» была разработана и поставлена на несколько объектов автоматизированная система мониторинга и технического диагностирования (АСМД). Готовим к выпуску АСМД на базе хроматографа «7Х». Вариант развития АСМД как коробочного продукта, расширяющего функционал приборов газового анализа, на наш взгляд, перспективен и заслуживает внимания. Продукт стандартизован и может внедряться компаниями-интеграторами.
Несмотря на то, что выше мы говорим в основном о приборах, АО «ИНТЕРА» является одним из старейших производителей комплексных автоматизированных систем мониторинга и диагностики «СКУ». Система поставлена более чем на 100 энергообъектов, включая атомные, тепловые и гидроэлектростанции. В конце 2020 года система мониторинга «СКУ» метрологически аттестована как средство измерений и может поставляться на объекты как измерительная система типа ИС-1 по ГОСТ Р 8.596-2002 либо как средство измерений для интеграции в измерительные системы типа ИС-2. Пример комплексного решения приведен на рисунке 3.
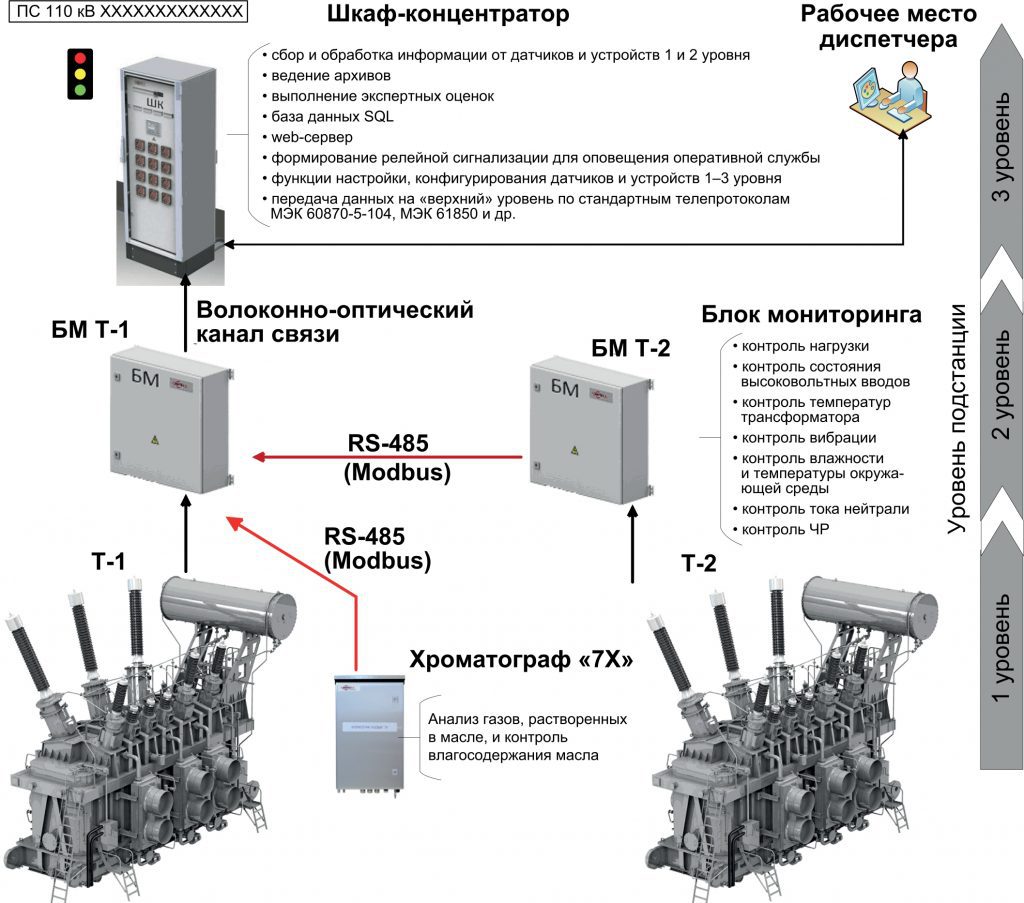
Изначально при разработке системы мониторинга мы ориентировались на web-интерфейс для формирования отчетов и визуализации (рисунок 4). По желанию заказчика была разработана SCADA-система (рисунок 5), но web-технологии развиваются и становятся машинонезависимыми, поэтому остаются наиболее предпочтительными при выборе системы визуализации (поскольку не зависит от производителя и одинаково работает как под управлением системами UNIX, так и под Windows).
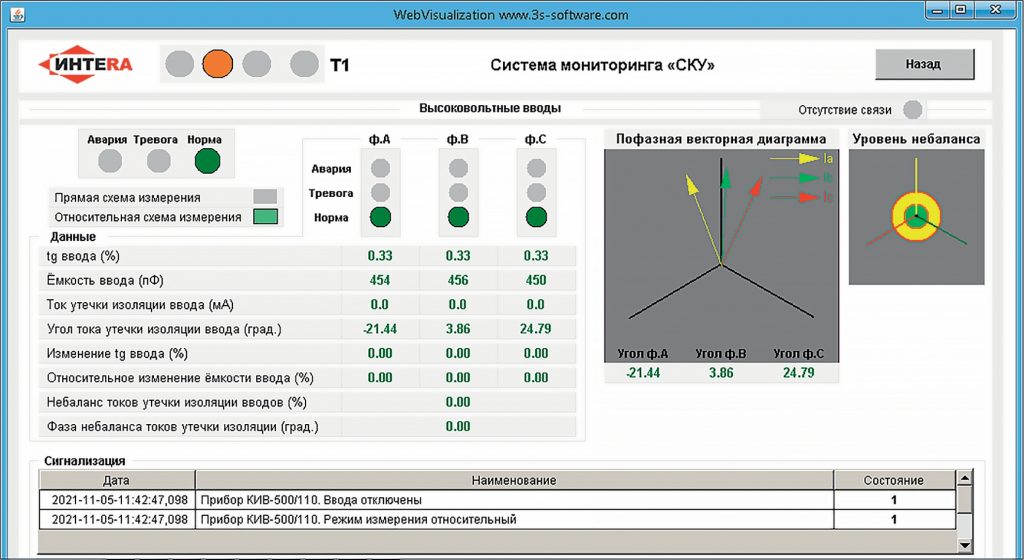
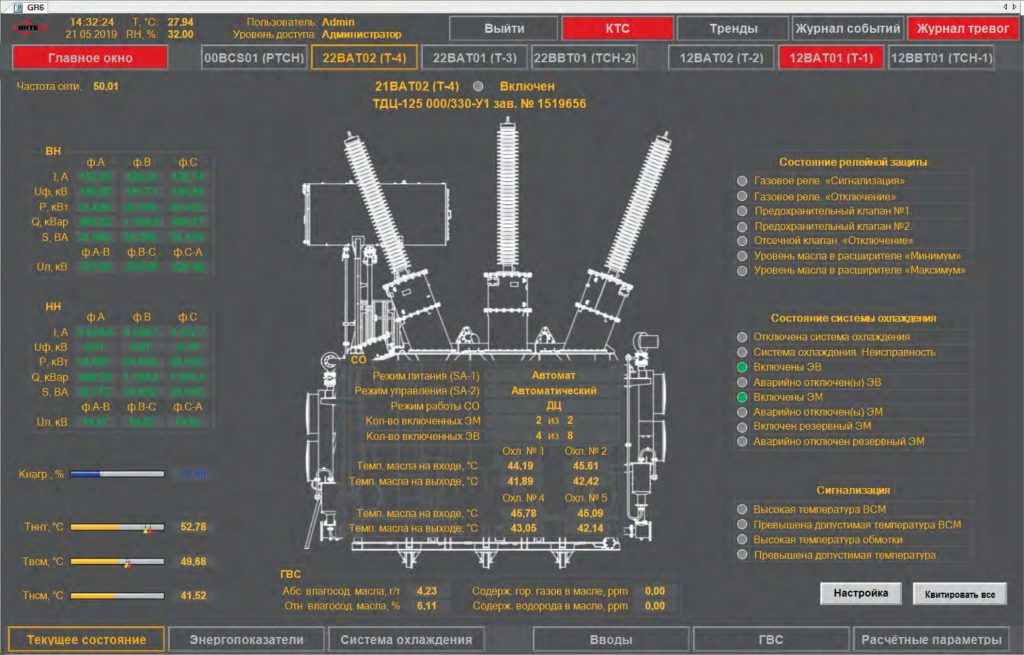
Одной из особенностей нашей системы мониторинга является то, что она имеет встроенную систему прогнозирования развития дефектов трансформатора. Основана она на моделях старения изоляции и рассчитывает остаточный срок службы трансформатора. У нас есть модель для расчета работы охладителя, по которой можно судить о степени его износа, модель расчета ресурса двигателей, модель старения и износа контактов РПН. Мы активно исследуем возможности моделирования и прогнозирования дефектов основного оборудования, но при этом понимаем, что для обеспечения доверия к прогнозу надо собирать статистику, анализировать взаимное влияние многих факторов. В ряде случаев точность расчета моделей зависит от исходных данных, которые может предоставить только производитель трансформатора.
