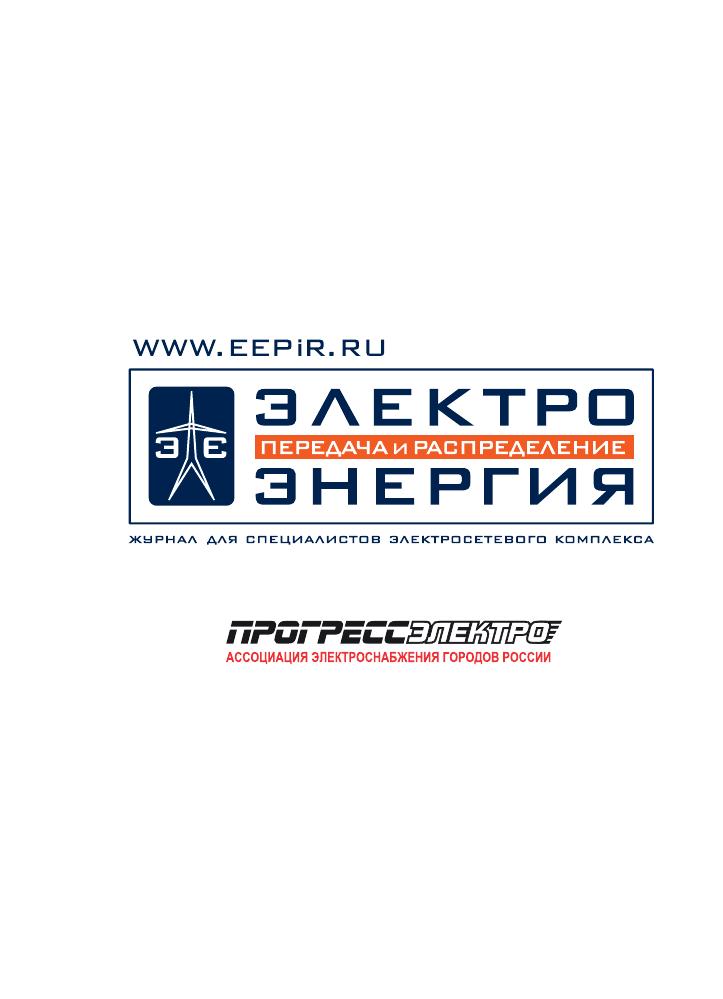
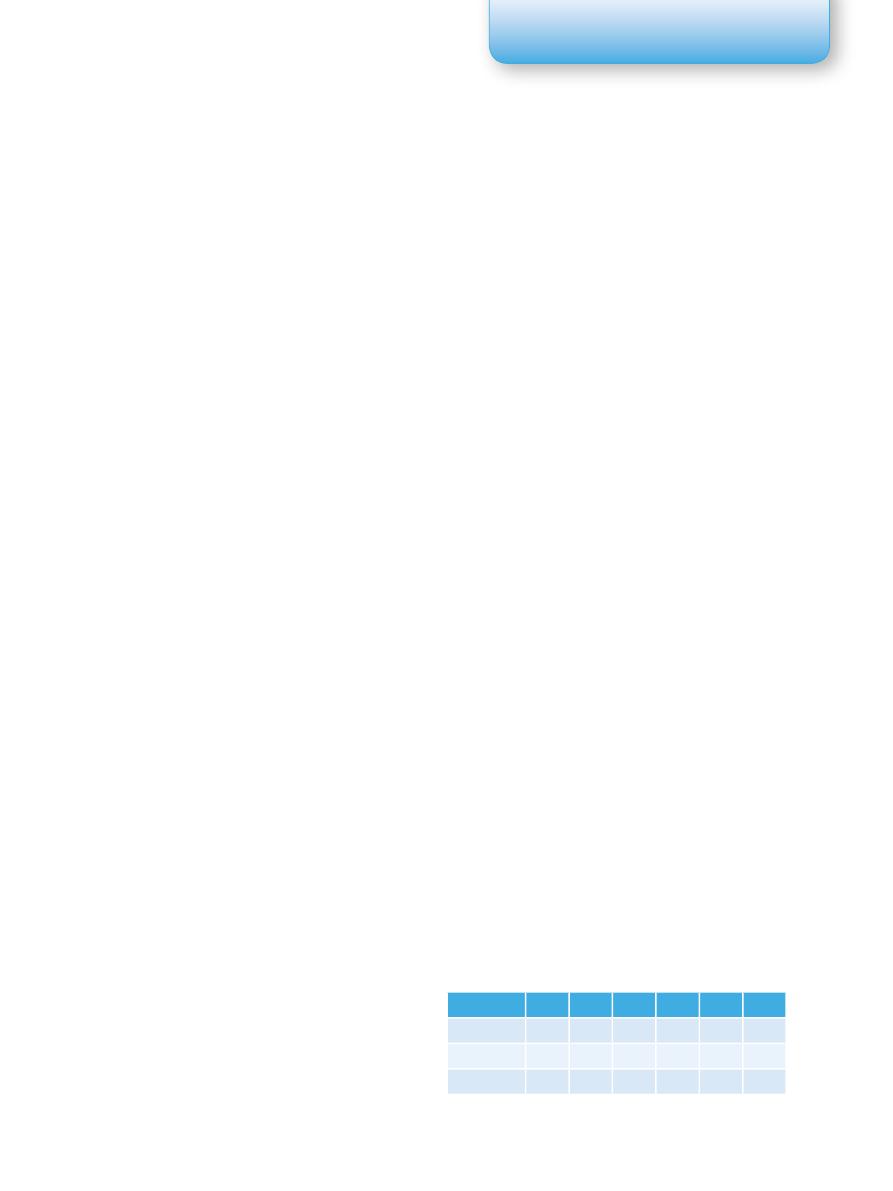
КАБЕЛЬ−news / № 8 / август 2009
57
Технологии расчетов
Главным достоинством нанесения лака на провод
с помощью калибров является возможность регули-
рования толщины наносимого слоя, что позволяет
оптимизировать время испарения Растворителя и
время структурирования. В слоях одинаковой тол-
щины степень завершенности химической реакции
будет постоянной. Следовательно, многослойна
изоляция эмалированного провода будет более
однородной по своим свойствам.
В настоящее время нет достаточно приемле-
мой для инженерного расчета методики подбора
маршрута калибров, температурного и скоростно-
го режима эмалирования. В большинстве случаев
решение этих проблем при изготовлении эмали-
рованных проводов производится опытным путем,
исходя из многолетней практики обслуживания
эмальагрегатов. И как показывает практика, под-
бор маршрутов калибров для эмалирования опыт-
ным путем не всегда дает оптимальный результат.
В связи с указанным, на разных заводах, при изго-
товлении одного и того же типоразмера провода,
применяемые маршруты калибров не совпадают
при одинаковом числе проходов. Провода получа-
ются разного качества и различной по цвету эма-
левой пленкой.
Методика расчета маршрута калибров, приве-
денная в работе [1], требует нахождения большого
количества вспомогательных величин, что значи-
тельно усложняет расчет, особенно для современ-
ных высокоскоростных эмальагрегатов с большим
числом проходов.
На кафедре злектроизоляционной и кабельной
техники Томского политехнического института была
разработана и на ЗАО «Сибкабель» апробирована
инженерная методика расчета размеров калибров
для производства эмалированных проводов про-
мышленного применения.
Расчет диаметра калибров
Для проводов диаметром d
0
выше 0,1 мм, которые
изготовляются с применением неразъемных кали-
бров. Диаметр первого калибра d
1
К
должен быть
больше диаметра провода на величину диаметраль-
ной толщины наносимого слоя лака
d
1
k
=
d
0
+ δ
ж
.
(1)
Толщина слоя лака, наносимого за один проход,
определяется числом проходов проволоки через
ванну с лаком, скоростью эмалирования, вязкостью
[1,2]. Стабильность толщины наносимого слоя лака
(δ
ж
=
const
) является одним из основных условий,
определяющих однородность физико-механических
и электрических свойств изоляции эмалированного
провода.
Диаметр следующего калибра
d
2
k
определяется
величиной сухого остатка лака
P
=
δ
T
/
δ
Ж
и толщи-
ной слоя эмали. Если маршрут калибров подобран
таким образом, что δ
Ж
=
const
по всем проходам,
тогда постоянной будет и толщина слоя эмали
δ
Т
=
const
, наносимая на каждом проходе. В этом
случае диаметр калибра
d
kn
для любого номера про-
хода
n
будет равен
d
kn
=
d
0
+ δ
Ж
+ (
n
–1)
·
δ
Ж
·
P
.
(2)
Была проведена сравнительная оценка резуль-
татов расчета маршрута калибров по методике,
изложенной в работе Пешкова И.Б и по предлагае-
мой методике. В качестве сравнения был взят при-
мер расчета калибров при эмалировании лаком
ВЛ-931 (винифлекс) медной проволоки диаметром
d
0
= 0,67 мм для обеспечения наложения изоляции
диаметральной толщиной δ = 0,04 мм при коли-
честве проходов
n
= 6,
P
= 10 [1]. Величину сухого
остатка (
Р
) приводится в технической документации
этого лака.
Результаты расчетов приведены в таблице 1,
из которых следует, что рассчитанные по пред-
лагаемой методике размеры калибров находятся
в хорошем соответствии с данными работы [1] и
толщина лака, наносимая за каждый проход, ле-
жит в пределах 68–71 мкм при расчетной величине
δ
Ж
= 67 мкм.
Расчет диаметра калибров
для эмалирования проволоки
Таблица 1. Расчетные диаметры калибров мкм
№ калибра
1
2
3
4
5
6
По Пешкову
0,740
0,744
0,752
0,758
0,766
0,776
Автор
0,737
0,744
0,750
0,757
0,764
0,771
δ
Ж
, мкм
70
67
68
67
69
71
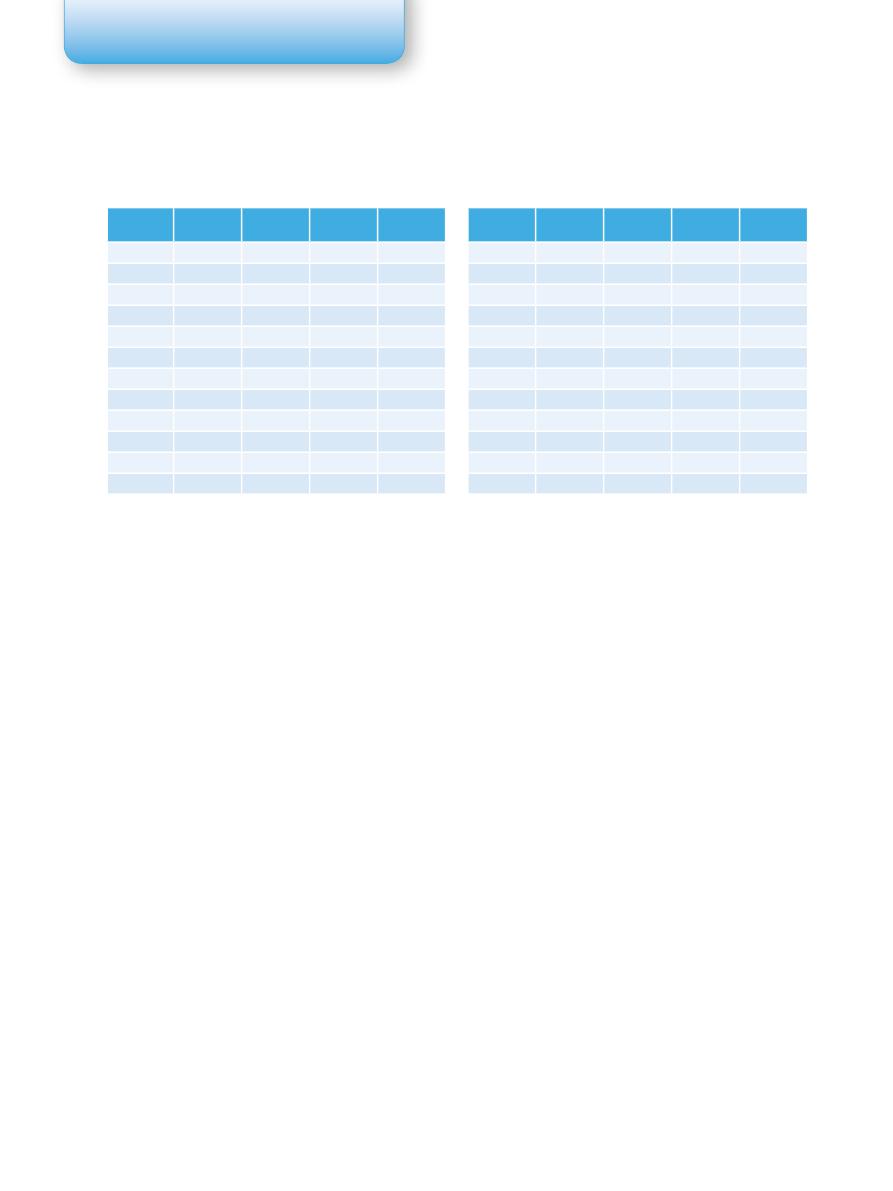
КАБЕЛЬ−news / № 8 / август 2009
58
Технологии расчетов
Апробация результатов работы
Предлагаемая методика расчета калибров была
апробирована на эмальобмоточном производстве
ЗАО «Сибкабель». Целью этой работы являлась
оценка качества технологических параметров эма-
лирования и их оптимизация. В табл.2 приведен
пример одного из маршрутов калибров, приме-
нявшемся ранее на эмальагрегате VS-900 при эма-
лировании провода
ПЭТВ-2
лаком
ПЭ
-943.
Исходя из применяемых на производстве марш-
рутов калибров при эмалировании провода ПЭТВ-2
лаком ПЭ-943 диаметром от 0,8 до 2,5 мм путем ста-
тистической обработки результатов было рассчи-
тано усредненное значение величины Р, которое
составило для лака ПЭ-943
Р
= 0,106.
Затем по уравнению (2) рассчитали диаметр ка-
либров по всем проходам, исходя из диаметраль-
ной толщины лака, наносимого на каждом проходе
δ
ж
. Суммарная толщина эмали, после n-го прохода
определялась как ∆
nT
= ∑δ
nT
.
В табл. 2 приведены размеры калибров, приме-
нявшиеся ранее на эмальагрегате, а в табл. 3 даны
размеры калибров для этого же провода, рассчи-
танные по предлагаемой методике. Как следует из
табл. 3 и рис. 1 шаг маршрута калибров уменьшился
почти в два раза с 10 до 5,4 мкм, а толщина эмали, на-
несенная на первом проходе возросла от δ = 30 мкм
до δ = 51 мкм и остается постоянной на всем марш-
руте калибров (сплошные линии рис. 1). Толщина
эмали, наносимая на каждом проходе, составляет
∆ = 5,4 мкм.
Таким образом, рассчитанные по предлагаемо-
му методу калибры для эмалирования проволоки
позволяют максимально оптимизировать техноло-
гический режим эмалирования без больших и слож-
ных для обслуживающего персонала расчетов.
Исходя из изложенного, можно сформулировать
правило проверки маршрута калибров:
произведе-
ние шага калибров на число проходов должно быть
равно толщине наносимой на провод твердой
эмали
.
В качестве примера рассмотрим табл. 2 и табл. 3.
Согласно табл. 2 при числе проходов
n
= 12 и шаге
калибров
h
= 10 мкм. толщина нанесенной на про-
вод эмали должна быть ∆
Т
=120 мкм. Реальная
толщина изоляционного покрытия составляет
∆
Т
= 65 мкм. Следовательно приведенный в табл. 2
маршрут калибров далек от оптимального.
По данным приведенным в табл. 3 притом же
числе проходов среднее значение шага калибров
составляет
h
= 5,4 мкм расчетное значение ∆
Т
= 65
мкм, что соответствует реальной толщине покры-
тия провода.
На рис. 1 представлены эти зависимости от числа
проходов
n
(пунктирные кривые). Из приведенных
результатов можно сделать следующие выводы:
1. Диаметр первого калибра слишком занижен и
при шаге калибров h = 10 мкм толщина пленки лака
δ
ж
постепенно увеличивается от 30 мкм на первом
калибре до 75,6 мкм на 12-м.
2. В самых неблагоприятных условиях формиро-
вания твердого покрытия находятся внешние слои
Табл.2. Размеры калибров по данным ЗАО «Cибкабель».
Провод ПЭТВ-2, лак ПЭ-943,
d
0
= 0,80 мм,
Δ = 0,065 мм,
n
= 12,
р
= 0,106
№
прохода
D
к
, мм
д
ж
, μкм
Д
эм
, μкм
D
эм
, мм
1
0,83
30
3,2
0,803
2
0,84
36,8
7,1
0,807
3
0,85
42,9
11,6
0,812
4
0,86
48,4
16,7
0,817
5
0,87
53,3
22,4
0,822
6
0,88
57,6
28,5
0,829
7
0,89
61,5
35,0
0,835
8
0,90
65,0
41,9
0,842
9
0,91
68,1
49,1
0,850
10
0,92
70,9
56,6
0,857
11
0,93
73,4
64,4
0,864
12
0,94
75,6
72,5
0,873
Табл.3. Расчетные размеры калибров ЗАО «Сибкабель».
Провод ПЭТВ-2, лак ПЭ-943,
d
0
= 0,80 мм,
Δ = 0,065 мм,
n
= 12,
р
= 0,106
№
прохода
D
к
, мм
δ
ж
, μкм
Δ
эм
, μкм
D
эм
, мм
1
0,851
51
5,4
0,805
2
0,856
51
10,8
0,811
3
0,862
51
16,2
0,816
4
0,867
51
21,6
0,822
5
0,873
51
27,0
0,827
6
0,878
51
32,4
0,832
7
0,883
51
37,8
0,838
8
0,889
51
42,3
0,842
9
0,894
51
48,6
0,848
10
0,999
51
54,1
0,852
11
0,905
51
59,5
0,859
12
0,910
51
64,9
0,865
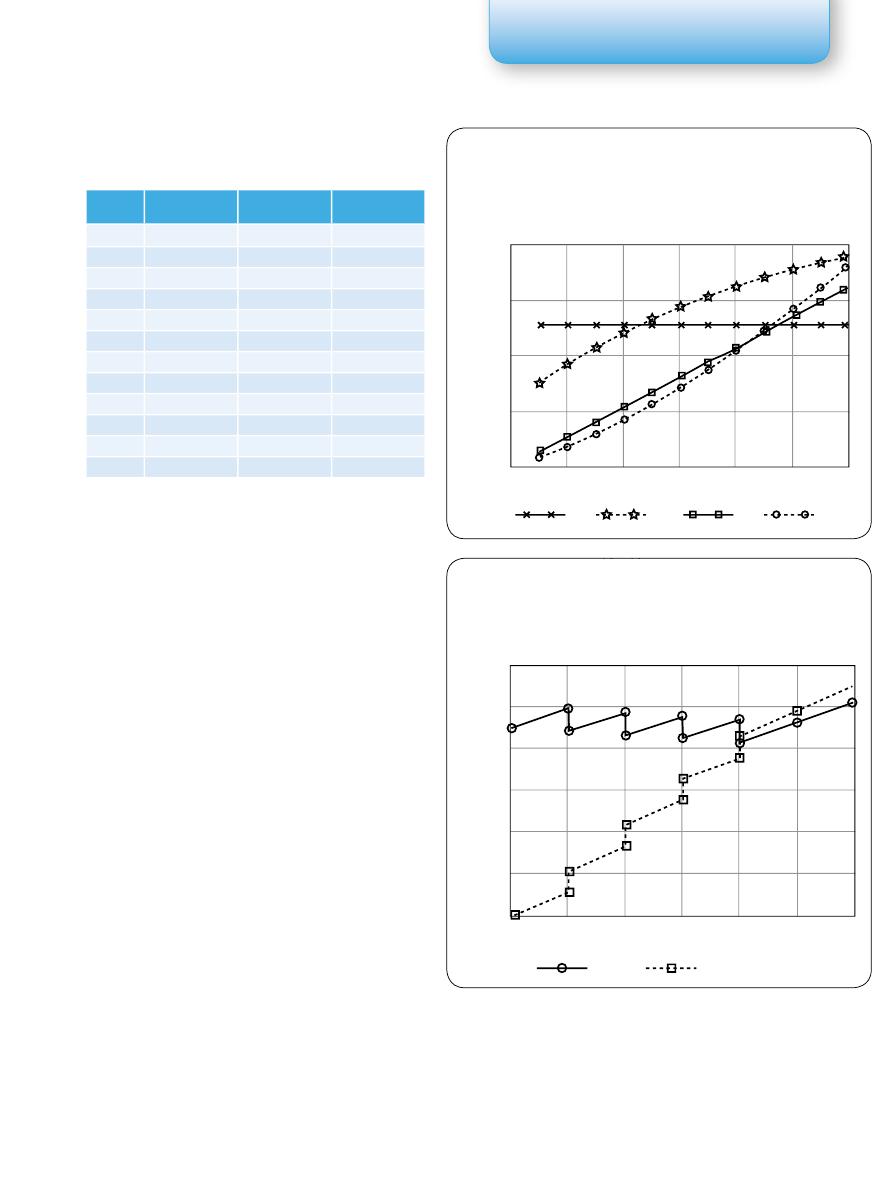
КАБЕЛЬ−news / № 8 / август 2009
59
Технологии расчетов
лака, что может привести их к вскипанию и (или)
недостаточной степени структурирования.
3. Нелинейный рост ∆1 от числа проходов так же
свидетельствует о возрастании толщины слоя эма-
ли, наносимой на каждом проходе от ∆1 = 3,2 мкм.
после первого прохода до ∆1 = 8,1 мкм. на послед-
нем.
В заводской практике не всегда удается подо-
брать размеры калибров в строгом соответствии
с расчетом. В таком случае приходится ставить
калибр ближайшего размера с тем, чтобы откло-
нение его диаметра от расчетного были мини-
мальны. Такая корректировка маршрута калибров
приводит к увеличению отклонения толщины
покрытия за один проход от его расчетного зна-
чения. При установленном по усредненным
данным маршруте калибров уравнение (2) по-
зволяет рассчитать реальную толщину лака, на-
носимого по каждому проходу и толщину эмали
табл. 2.
При эмалирования провода диаметром 0,8
мм, при расчетном шаге калибров
h
= 0,5 мм,
были установлены калибры диаметром кратным
0,010 мм. Для получения заданной толщины слоя
лака, наносимого на каждом проходе, диаметр ка-
либров увеличивался на 0,01 мм через каждые два
прохода. Разброс толщин слоев лака от прохода
к проходу составлял от 0,048 до 0,056 мм, т. е. не
более 15%.
Как следует из рис. 2, прирост толщины твердого
покрытия на каждом проходе различный. Однако
это различие незначительно и условия структу-
рирования лака по проходам существенно не из-
меняются. Примененный маршрут калибров (табл.
4, рис. 2) близок к оптимальному и существенно
отличается от данных, приведенных в табл. 1 и на
рис. 1.
Табл.4. Усредненные значения маршрута
калибров и толщины изоляции
№
прохода
d
k
мм среднее
δ
Ж
мм
Δ
Т
мм
1
0,85
0,05
0,0053
2
0,86
0,055
0,011
3
0,86
0,049
0,016
4
0,87
0,054
0,022
5
0,87
0,048
0,027
6
0,88
0,053
0,033
7
0,88
0,048
0,038
8
0,89
0,052
0,043
9
0,89
0,047
0,048
10
0,90
0,051
0,054
11
0,91
0,056
0,06
12
0,91
0,051
0,065
80
60
40
20
0
0 2 4 6 8 10 12
δ, ∆ μкм
n
δ
δ1
∆
∆1
Рис. 1. Зависимость толщины слоя лака δ и δ1, наносимого на
каждом проходе и толщины эмали ∆ и ∆1 от номера калибра.
δ и ∆ — рассчитанный маршрут калибров
δ1 и ∆1 — — — маршрут калибров, установленный ранее на
эмальагрегате
0,065
0,055
0,045
0,035
0,025
0,015
0,0053
0,85 0,86 0,87 0,88 0,89 0,9 0,91
δ, ∆ мм
d
K
мм
δ
∆
Рис. 2. Влияние усреднения расчетных диаметров калибров на
толщину лака наносимого на каждом проходе (—) и толщину
изоляции провода по проходам (- - -).
d
0
= 0,8 мм
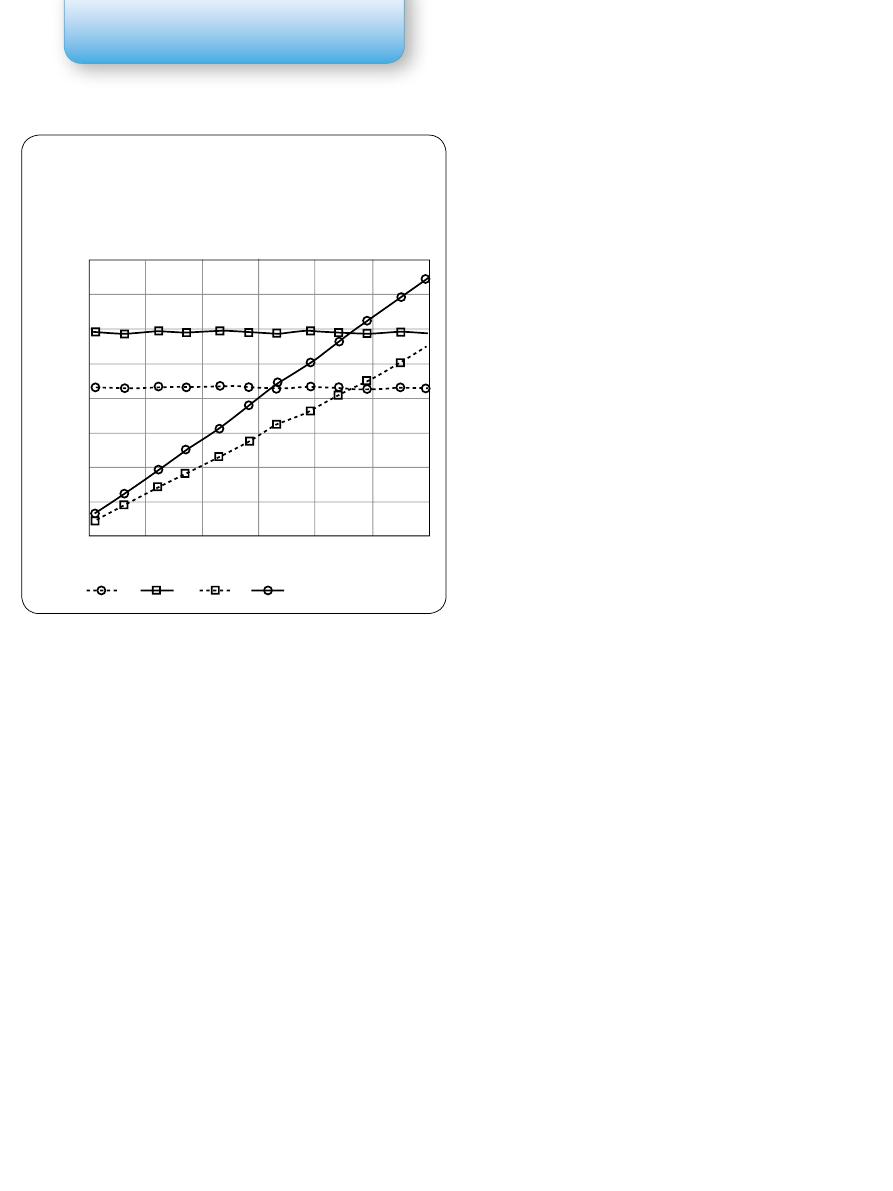
КАБЕЛЬ−news / № 8 / август 2009
60
Технологии расчетов
В заводской практике при расчете маршрута ка-
либров стараются учесть все возможные факторы,
приводящие к уменьшению толщины слоя нане-
сенной эмали, например, вытяжку провода, допуск
на диаметр провода и т.д.
По приведенному уравнению (2) были рассчи-
таны: маршрут калибров для номинального диа-
метра провода
d
0
= 0,8 мм при средней толщине
изоляции Δ
т
= 0,56 мм, толщина слоя лака, нано-
симого за один проход и толщина эмали (рис. 3).
Как следует из этого рисунка, если эмалируется
провод с максимальным положительным допу-
ском
d
0
= 0,8 + 0,008 мм, толщина лака, наносимо-
го за один проход, составляет 0,042 мм, а полная
толщина изоляции Δ
т
= 0,055 мм. При эмалиро-
вании на этом же маршруте калибров провода с
отрицательным допуском
d
0
= 0,8 – 0,008 мм тол-
щина наносимого за один проход лака увеличи-
вается до 0,059 мм, а полная толщина эмали до
Δ
т
= 0,075 мм.
Таким образом, если даже не учитывать допуск
на диаметр провода, то при правильно подобран-
ном маршруте калибров толщина нанесенной
на провод изоляции будет находиться в преде-
лах, допускаемых техническими условиями на
эмалированные провода. Решение по уточне-
нию маршрута калибров с целью экономии лака
принимает технолог по производству эмаль-
проводов.
Предлагаемая методика расчета калибров для
эмалирования провода была использована на ЗАО
«Сибкабель» при изготовлении провода ПЭТВ-2
диаметром 0,335, 0,80, и 1,0 мм и показала по-
ложительные результаты. Рассчитанные марш-
руты калибров обеспечили более равномерную
толщину элементарных слоев лака наносимых
за каждый проход в процессе эмалирования,
увеличение минимальных значений пробивно-
го напряжения и механической прочности изо-
ляции и как следствие — увеличение скорости
эмалирования.
Выводы
При расчете маршрута калибров необходимо
учитывать следующие требования:
1. Толщина наносимой пленки лака должна быть
одинаковой по всем проходам для создания оди-
наковых условий поликонденсации.
2. Шаг ступени калибров
h
=
d
i
+1
—
d
i
должен
быть одинаковым по всему маршруту.
3. Толщина твердого покрытия эмали, наносимая
за каждый проход, равна шагу маршрута калибров
δ
T
=
h
=
δ
Ж
·
P
.
4. Толщина слоя жидкой эмали, наносимая на
первом проходе, должна быть такой же, как и на
остальных проходах.
А. В. Петров
, доцент кафедры
«Электроизоляционная и кабельная техника»
Томского политехнического университета
Г.Н. Дзюбань
, начальник эмальобмоточного
производства ЗАО «Сибкабель»
О.Н. Елисеева
, начальник технологического
бюро эмальобмоточного производства
ЗАО «Сибкабель»
Литература
1. Основы кабельной техники: Учебник для студентов
высших учебных заведений / Леонов В.М., Пешков И.Б.,
Рязанов И.Б., Холодный С.Д. / Под ред. И.Б. Пешкова. —
М.: Изд. центр «Академия», 2006. — 432 с.
2. Пешков И.Б. Обмоточные провода. — М.: Энергия,
1995. — 416 с.
3. Холодный С.Д. Технология термообработки изоля-
ции кабелей и проводов. — М.: МЭИ, 1994. —160 с.
0,08
0,07
0,06
0,05
0,04
0,03
0,02
0,01
0
0,85 0,86 0,87 0,88 0,89 0,9 0,91
δ, ∆ мм
d
K
мм
δ1
δ1
δ2
δ2
∆1
∆1
∆2
∆2
Рис. 3. Рассчетные зависимости диаметральной толщины лака
наносимого на каждом проходе (δ1, δ2) и толщины изоляции провода
(∆1, ∆2) по каждому проходу.
d
K
— диаметры калибров маршрута эмалирования.
Диаметр провода d
0
= 0,8 мм
Оригинал статьи: Расчет диаметра калибров для эмалирования проволоки
Главным достоинством нанесения лака на провод с помощью калибров является возможность регулирования толщины наносимого слоя, что позволяет оптимизировать время испарения Растворителя и время структурирования. В слоях одинаковой толщины степень завершенности химической реакции будет постоянной. Следовательно, многослойна изоляция эмалированного провода будет более однородной по своим свойствам.