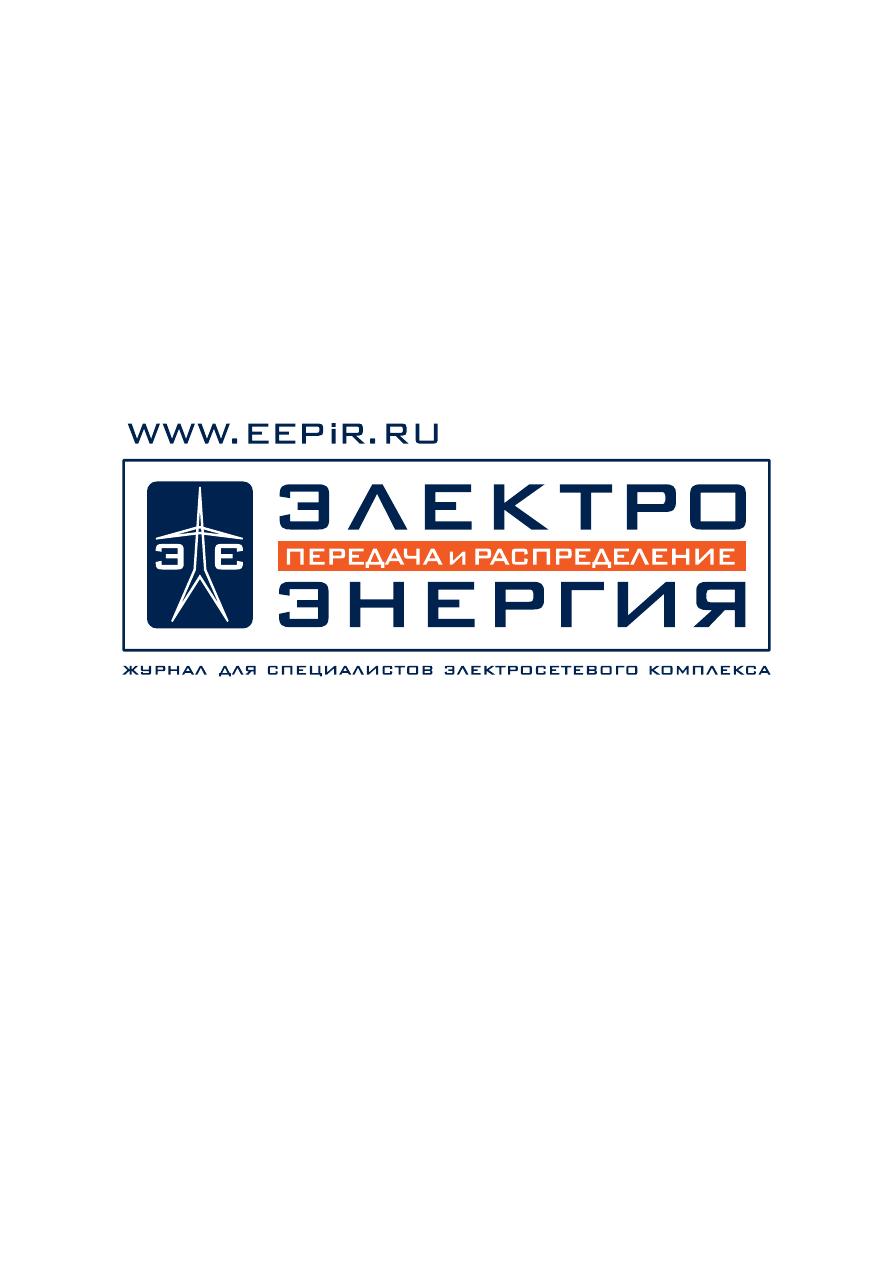
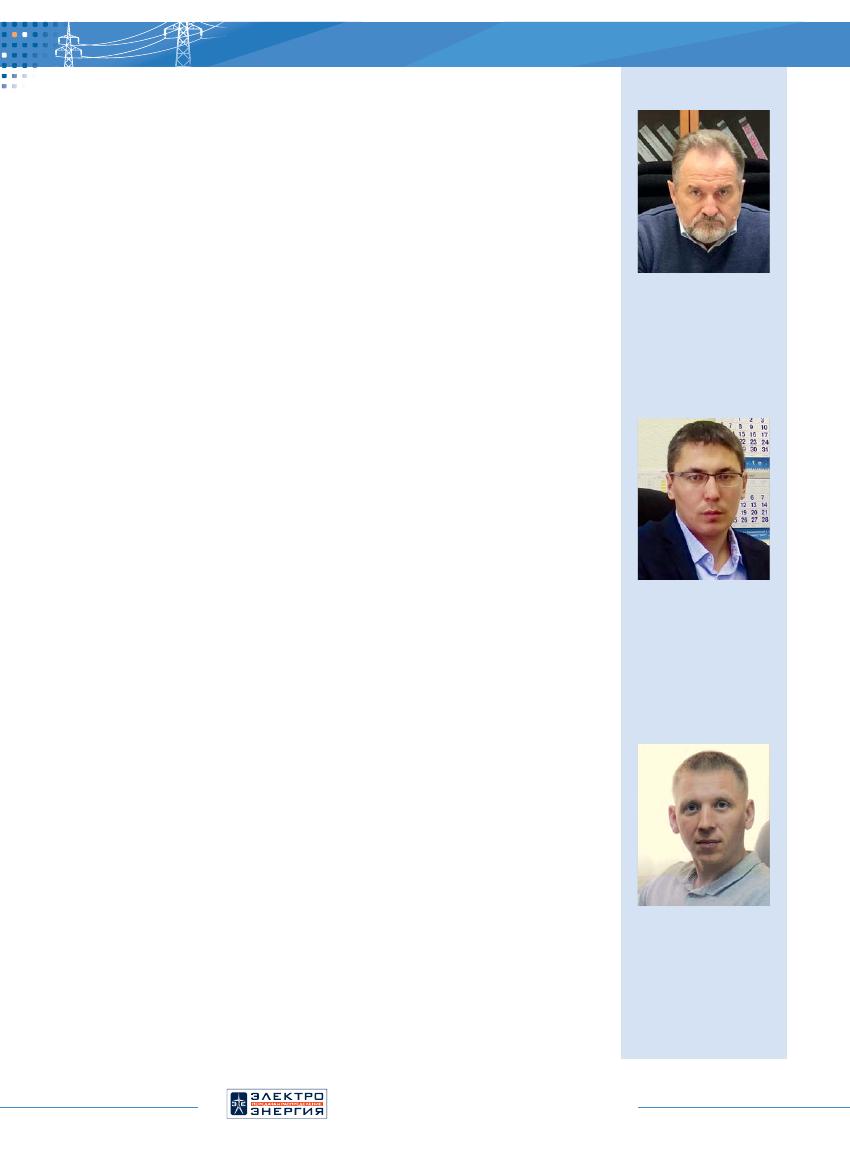
44
Ежеквартальный
спецвыпуск
№
2(9),
июль
2018
Оценка
эксплуатационной
надежности
опорно
-
стержневых
изоляторов
и
покрышек
маломасляных
выключателей
методом
ультразвукового
нераз
-
рушающего
контроля
О
дними
из
основных
задач
энергетических
компаний
является
надежное
электро
-
снабжение
потребителей
и
безопасность
обслуживающего
персонала
.
Для
обеспечения
безаварийной
работы
электроустановок
,
выполненных
из
электротехнического
фарфора
,
необходимо
иметь
объективную
оценку
их
механического
состояния
.
Надежность
работы
разъединителей
и
высоковольтных
вы
-
ключателей
в
значительной
степени
зависит
от
качества
опорно
-
стержневых
изоляторов
и
фарфоровых
покрышек
.
Повреждаемость
разъединителей
и
выключателей
из
-
за
поло
-
мок
изоляторов
в
результате
развития
внутренних
дефектов
остается
высокой
.
Для
контроля
состояния
фарфоровой
изоляции
разработаны
и
применяются
более
де
-
сяти
методов
диагностики
,
таких
как
:
метод
регистрации
сигналов
акустической
эмиссии
,
вибрационный
метод
,
метод
сквозного
прозвучивания
,
метод
,
основанный
на
выявлении
коронного
и
частичных
разрядов
,
и
т
.
д
.
В
филиале
АО
«
Тюменьэнерго
» —
Сургутские
электрические
сети
,
начиная
с
середины
90-
х
годов
были
,
опробованы
различные
методы
Настоящий
информационный
материал
посвящен
вопросу
оценки
эксплуатационной
надежности
изоляционных
конструк
-
ций
электроустановок
,
выполненных
из
электротехнического
фарфора
.
Для
выявления
основных
видов
дефектов
,
снижа
-
ющих
эксплуатационную
надежность
опорно
-
стержневых
изо
-
ляторов
,
покрышек
маломасляных
выключателей
,
использу
-
ется
ультразвуковой
неразрушающий
контроль
.
Представлены
некоторые
статистические
данные
результатов
обследования
в
процессе
эксплуатации
и
при
входном
контроле
фарфоровых
изделий
.
Проведено
комплексное
обследование
опорно
-
стерж
-
невых
изоляторов
разных
производителей
.
В
целях
подтверж
-
дения
выявленных
дефектов
выполнено
вскрытие
изоляторов
и
осмотр
их
составных
частей
.
Ильяр
УРАЗАЛИЕВ
,
заместитель
началь
-
ни
ка
Службы
изо
-
ляции
и
защиты
от
перенапряжений
филиала
АО
«
Тюмень
-
энерго
» —
Сургутские
электрические
сети
Дмитрий
БЕДА
,
мастер
1
группы
Службы
изоляции
и
защиты
от
пере
-
напряжений
филиала
АО
«
Тюменьэнерго
» —
Сургутские
электри
-
ческие
сети
Виталий
БУТКЕВИЧ
,
первый
заместитель
директора
—
главный
инженер
филиала
АО
«
Тюменьэнерго
» —
Сургутские
электри
-
ческие
сети
Диагностика
и
мониторинг
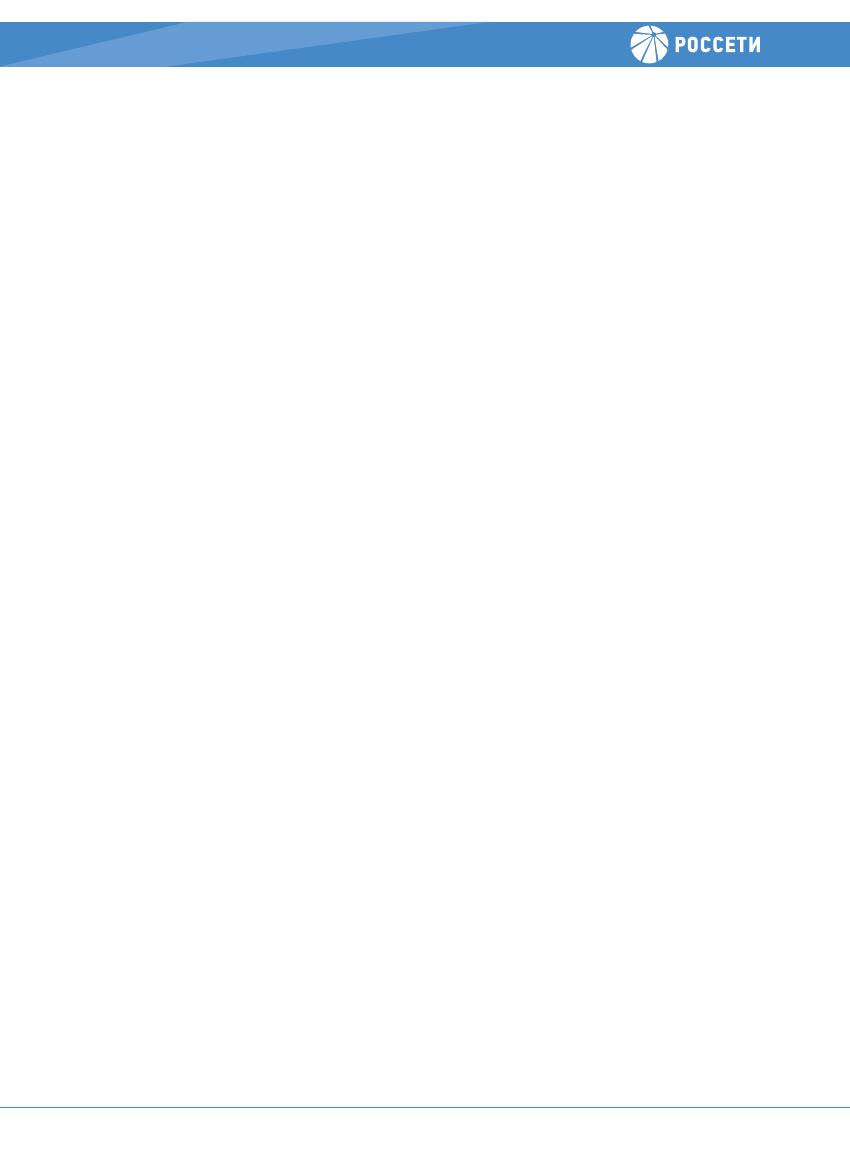
45
определения
механического
состояния
изделий
из
электро
-
технического
фарфора
,
в
том
числе
и
ультразвуковой
нераз
-
рушающий
контроль
.
В
последующие
годы
и
по
настоящее
время
для
выявления
основных
видов
дефектов
,
снижающих
эксплуатационную
надежность
опорно
-
стержневых
изолято
-
ров
(
ОСИ
)
и
покрышек
маломасляных
выключателей
,
при
-
меняется
метод
ультразвукового
неразрушающего
контроля
.
За
все
эти
годы
для
приобретения
необходимого
опыта
при
-
менения
данного
метода
и
отработки
практических
навыков
и
для
выполнения
части
объема
работ
филиалом
Сургутские
электрические
сети
неоднократно
привлекались
специалисты
(
разработчики
метода
УЗНК
)
АООТ
НИИ
«
Электрокерамика
»
(
в
дальнейшем
ООО
«
Центр
испытаний
высоковольтного
обо
-
рудования
и
материалов
»).
ОБЩИЕ
СВЕДЕНИЯ
ОБ
УЛЬТРАЗВУКОВОМ
НЕРАЗРУШАЮЩЕМ
КОНТРОЛЕ
Ультразвуковой
неразрушающий
контроль
позволяет
выяв
-
лять
дефекты
в
фарфоровых
изделиях
,
возникающие
в
про
-
цессе
эксплуатации
и
при
нарушении
технологии
изготовле
-
ния
изоляторов
.
К
таким
дефектам
можно
отнести
наличие
трещин
,
зон
растрескивания
в
оконечностях
изоляторов
,
по
-
лости
,
различные
включения
,
макроскопическая
пористость
.
Все
указанные
дефекты
могут
быть
выявлены
с
помощью
ультразвуковой
дефектометрии
.
Нормативно
-
техническая
документация
на
высоковольт
-
ный
электротехнический
фарфор
и
изделия
из
него
достаточ
-
но
подробно
регламентирует
дефекты
,
выявляемые
визуаль
-
но
,
где
недопустимыми
,
критическими
признаются
наружные
трещины
[3,
стр
. 18].
Визуальный
контроль
в
эксплуатации
позволяет
выявить
только
ярко
выраженные
трещины
при
ос
-
мотре
фарфоровых
изделий
с
земли
,
однако
малозаметные
трещины
определить
гораздо
сложнее
,
а
в
заармированных
зонах
—
невозможно
.
Ультразвуковая
дефектометрия
основана
на
способности
ультразвуковых
колебаний
распространяться
в
упругой
сре
-
де
.
Ультразвуковые
волны
отражаются
или
рассеиваются
при
взаимодействии
с
внутренним
дефектом
(
трещина
,
раковина
,
зона
растрескивания
,
зона
неоднородной
плотности
и
т
.
д
.),
что
позволяет
обнаруживать
внутренние
дефекты
изделия
.
Ми
-
нимальная
площадь
дефекта
в
плоскости
может
составлять
несколько
квадратных
миллиметров
.
Ультразвуковая
струк
-
турометрия
сводится
к
измерению
скорости
распространения
в
фарфоровом
изделии
ультразвуковых
колебаний
,
с
помо
-
щью
которых
выявляются
дефекты
типа
открытой
микроско
-
пической
пористости
,
нарушения
состава
фарфоровой
массы
.
Действующие
стандарты
на
высоковольтный
электротех
-
нический
фарфор
требуют
полного
отсутствия
микроскопиче
-
ской
пористости
по
всему
объему
изолятора
[1,
стр
. 7].
Откры
-
тая
микроскопическая
пористость
(
ОМИП
) —
дефект
,
который
возникает
только
при
нарушении
технологии
изготовления
из
-
делий
из
электротехнического
фарфора
(«
технологический
»
дефект
),
и
ни
при
каких
условиях
не
может
возникнуть
в
экс
-
плуатации
.
ОМИП
представляет
собой
систему
микроскопиче
-
ских
(
характерный
размер
— 5–7
мкм
)
пор
«
открытого
»
типа
,
то
есть
связанных
между
собой
.
Эти
поры
имеют
,
как
правило
,
вытянутую
форму
,
отличаясь
этим
от
«
закрытых
»,
не
связан
-
ных
между
собой
пор
,
и
позволяют
влаге
проникать
в
фарфор
.
«
Прямое
»
определение
ОМИП
проводится
методом
фуксино
-
вой
пробы
под
давлением
на
специально
отобранных
образ
-
цах
.
Данный
метод
нормирован
действующими
стандартами
на
высоковольтный
электротехнический
фарфор
[2,
стр
. 12].
Существует
почти
линейная
зависимость
между
глубиной
прокраски
фарфора
фуксином
и
скоростью
распространения
ультразвуковой
волны
в
нем
.
Согласно
методике
,
разработанной
АООТ
НИИ
«
Электро
-
керамика
»
и
ООО
«
ЦИВОМ
»,
все
изоляторы
по
результатам
эксплуатационного
ультразвукового
неразрушающего
контро
-
ля
разделяются
на
5
сортов
[3,
стр
. 78]:
I.
Изделия
I
сорта
считаются
полностью
годными
и
контролю
в
дальнейшем
могут
не
подвергаться
,
эксплуатируются
без
ограничений
в
течение
срока
службы
в
качестве
сколь
угод
-
но
ответственных
элементов
изоляционных
конструкций
.
II.
Изделия
II
сорта
эксплуатируются
также
без
ограничений
,
но
периодически
контролируются
(
проводится
дефекто
-
метрия
оконечностей
).
III.
Изделия
III
сорта
рекомендуется
сохранить
лишь
для
ме
-
нее
ответственных
конструкций
(
шинные
мосты
,
стойки
и
т
.
п
.)
при
условии
периодического
проведения
дефекто
-
метрии
оконечностей
.
IV.
Изделия
IV
сорта
подлежат
первоочередной
замене
и
уча
-
щенному
контролю
до
этого
.
V.
Изделия
V
сорта
(
видимые
трещины
)
подлежат
внеоче
-
редной
замене
.
К
изделиям
V
сорта
относим
также
полно
-
стью
разрушившиеся
изоляторы
.
Отметим
,
что
браковочные
критерии
ультразвукового
не
-
разрушающего
контроля
зависят
от
целого
ряда
факторов
(
со
-
става
фарфоровой
массы
,
типа
изделия
,
особенности
техно
-
логии
,
применяемой
на
заводе
-
изготовителе
фарфора
в
кон
-
кретный
период
).
Поэтому
приходится
определять
браковоч
-
ные
критерии
отдельно
для
различных
партий
изоляторов
.
УЛЬТРАЗВУКОВОЙ
НЕРАЗРУШАЮЩИЙ
КОНТРОЛЬ
ФАРФОРОВЫХ
ОПОРНО
-
СТЕРЖНЕВЫХ
ИЗОЛЯТОРОВ
В
ПРОЦЕССЕ
ЭКСПЛУАТАЦИИ
Диагностирование
опорно
-
стержневых
изоляторов
методом
ультразвукового
неразрушающего
контроля
возможно
про
-
изводить
как
на
месте
установки
,
в
смонтированном
состоя
-
нии
(
разъединители
,
отделители
,
шинные
мосты
и
т
.
д
.)
при
выведенном
оборудовании
в
ремонт
,
так
и
в
виде
одиночных
изделий
вне
электроустановок
.
Обследование
фарфоровых
изоляторов
выполняется
в
соответствии
с
многолетним
графиком
.
В
процессе
экс
-
плуатации
периодическому
контролю
подлежат
изоляторы
,
отнесенные
ко
II
сорту
.
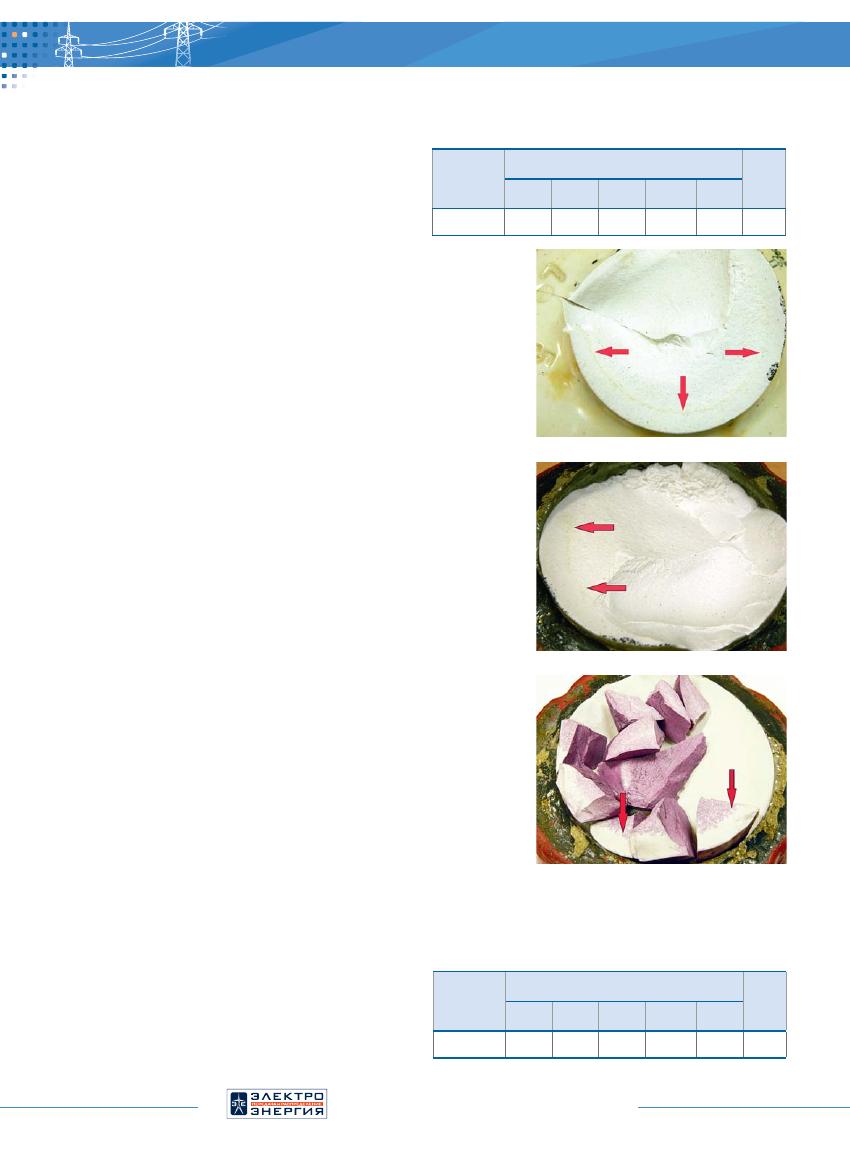
Табл
. 1.
Ультразвуковой
контроль
опорно
-
стержневой
изоля
-
ции
(
в
составе
разъединителей
)
в
эксплуатации
Номиналь
-
ное
напря
-
жение
,
кВ
Количество
обследованных
ОСИ
,
шт
.
Всего
ОСИ
,
шт
.
I
сорт
II
сорт
III
сорт
IV
сорт
V
сорт
110
454
1562
172
242
63
2493
Табл
. 2.
Ультразвуковой
контроль
опорно
-
стержневой
изоляции
в
виде
одиночных
изделий
Номиналь
-
ное
напря
-
жение
,
кВ
Количество
обследованных
ОСИ
,
шт
.
Всего
ОСИ
,
шт
.
I
сорт
II
сорт
III
сорт
IV
сорт
V
сорт
110
371
477
51
8
1
908
46
Ежеквартальный
спецвыпуск
№
2(9),
июль
2018
Некоторые
статистические
данные
обследованных
опор
-
но
-
стержневых
изоляторов
110
кВ
в
составе
разъединителей
за
период
с
2009
по
2018
года
представлены
в
таблице
1.
В
эксплуатации
были
оставлены
изоляторы
,
отнесен
-
ные
к
I
и
II
сортам
.
Заменено
около
20%
от
общего
количе
-
ства
обследованных
опорно
-
стержневых
изоляторов
.
Полученные
результаты
эксплуатационного
контроля
изоляторов
выборочно
были
проверены
путем
визуального
осмотра
.
Также
произведено
разрушение
изоляторов
,
отне
-
сенных
к
IV
и
V
сортам
,
для
отбора
образцов
,
с
целью
испытания
методом
фуксиновой
пробы
под
давлением
.
На
рисунках
1, 2
и
3
представлен
образец
фарфора
изолятора
типа
ИОС
–110–400
с
дефектом
после
испытания
мето
-
дом
фуксиновой
пробы
под
давлением
[2,
стр
. 12].
Из
приведенного
примера
следует
выделить
открытую
микроскопиче
-
скую
пористость
,
обнаруженную
в
верхней
части
изолятора
.
Не
прокрашен
-
ная
околоповерхностная
часть
образца
указывает
на
достаточную
степень
пропекания
фарфоровой
массы
в
процессе
изготовления
.
Интенсивная
прокраска
образца
внутренней
части
опорно
-
стержневого
изолятора
свиде
-
тельствует
о
наличии
зоны
ОМИП
,
что
и
привело
к
образованию
внутренней
трещины
,
зоны
растрескивания
в
теле
изолятора
.
Трещины
чаще
всего
воз
-
никают
в
заармированной
зоне
изолятора
,
которая
не
доступна
для
визуаль
-
ного
обнаружения
даже
в
случае
выхода
трещины
на
поверхность
изолято
-
ра
.
До
тех
пор
,
пока
армировочный
слой
остается
герметичным
,
наличие
глубинной
ОМИП
отрицательным
образом
не
проявляется
.
При
нарушении
герметичности
армировки
,
целостности
глазури
происходит
пропитывание
влагой
внутренних
областей
изолятора
,
что
при
воздействии
отрицательных
температур
приводит
к
механическому
разрушению
,
растрескиванию
фар
-
фора
.
Это
продемонстрировано
на
примере
рисунков
1, 2
и
3.
Сроки
впиты
-
вания
влаги
фарфором
зависят
от
многих
факторов
и
могут
составлять
от
нескольких
месяцев
до
нескольких
лет
.
УЛЬТРАЗВУКОВОЙ
НЕРАЗРУШАЮЩИЙ
КОНТРОЛЬ
ФАРФОРОВЫХ
ОПОРНО
-
СТЕРЖНЕВЫХ
ИЗОЛЯТОРОВ
ПРИ
ВХОДНОМ
КОНТРОЛЕ
За
тот
же
период
(9
лет
)
в
филиале
проведен
ультразвуковой
неразрушаю
-
щий
контроль
вновь
приобретенных
или
находящихся
в
резерве
908
опорно
-
стержневых
изоляторов
разных
производителей
.
Результаты
проделанной
работы
приведены
в
таблице
2.
В
общем
количестве
за
последние
3
года
по
результатам
проведенного
входного
контроля
изоляторов
разных
производителей
к
III
сорту
были
отне
-
сены
7
штук
,
а
234
присвоен
II
сорт
,
в
результате
чего
все
они
были
возвраще
-
ны
и
заменены
на
новые
(I
сорта
).
В
конце
2017
года
была
проведена
работа
по
оценке
качества
изоляторов
типа
ИОС
-110-400
разных
производителей
.
Обследование
производилось
специалистами
ООО
«
Центр
испытаний
вы
-
соковольтного
оборудования
и
материалов
»
совместно
с
работниками
фи
-
лиала
на
испытательной
площадке
одного
из
заводов
-
из
-
готовителей
высоковольтных
изоляторов
.
Для
проведения
комплексного
обследования
было
отобрано
10
изоляторов
.
В
6
изделиях
при
проведении
ультразвукового
неразрушающего
контроля
в
верхних
и
нижних
«
опасных
»
сечениях
,
то
есть
областью
между
краем
фланца
и
первым
ребром
изолятора
,
были
выявле
-
ны
неоднородности
(
трещины
,
полости
,
включения
и
т
.
д
.).
Рис
. 1.
Верхняя
часть
(«
юбка
»)
изолятора
Рис
. 2.
Верхний
оголовок
изолятора
Рис
. 3.
Образец
фарфора
верхней
части
изо
-
лятора
после
испытания
методом
фуксино
-
вой
пробы
под
давлением
Диагностика
и
мониторинг
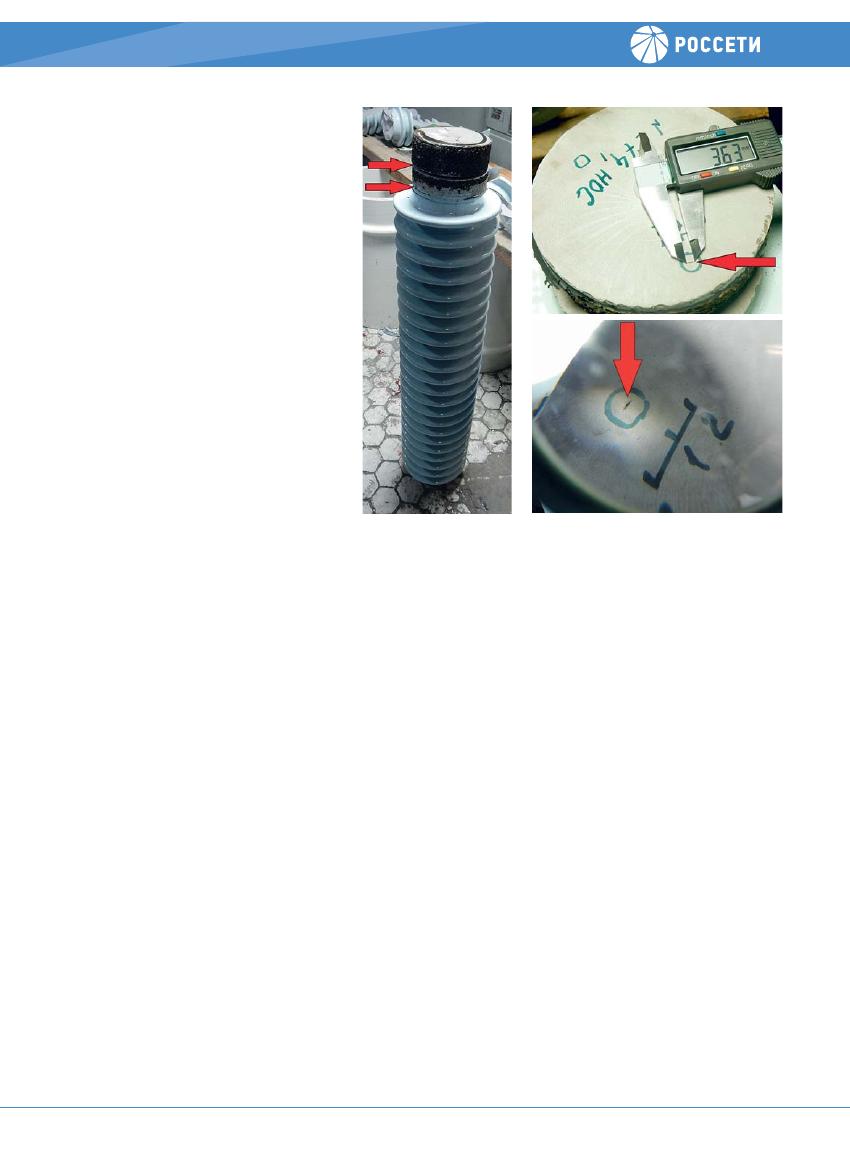
47
Действующий
ГОСТ
[2]
регламентирует
про
-
ведение
ультразвуковой
дефектометрии
в
«
ак
-
сиальном
»
направлении
,
то
есть
с
торцевой
поверхности
изолятора
.
Для
оценки
объектив
-
ности
результатов
при
проведении
ультразву
-
ковой
дефектометрии
в
«
радиальном
»
направ
-
лении
из
шести
«
дефектных
»
изоляторов
было
выбрано
одно
изделие
для
более
детального
обследования
.
Фланцы
этого
изолятора
были
удалены
распиливанием
на
4
части
(
рисунок
4)
и
проведено
прозвучивание
как
в
«
аксиальном
»
направлении
,
так
и
в
«
радиальном
»,
то
есть
с
боковой
поверхности
изолятора
.
Сам
изо
-
лятор
был
распилен
алмазным
диском
в
ниж
-
нем
«
опасном
»
сечении
,
а
именно
,
в
области
,
определенной
по
результатам
измерений
,
при
«
аксиальном
»
и
«
радиальном
»
прозвучивании
выявлен
макроскопический
дефект
—
полость
в
виде
трещины
(
рисунок
5).
В
соответствии
с
требованиями
ГОСТ
[2]
данный
изолятор
счи
-
тается
«
не
выдержавшим
испытания
».
Необхо
-
димо
отметить
,
что
обсуждаемый
дефект
был
выявлен
опеределением
зоны
его
нахождения
как
при
«
аксиальном
»,
так
и
при
«
радиальном
»
прозвучивании
с
совпадением
результатов
.
Дополнительно
,
для
оценки
качества
изоля
-
торов
,
были
проведены
механические
испытания
,
а
именно
:
–
термоудар
,
то
есть
резкое
изменение
температуры
путем
погружения
изоляторов
в
ванны
с
холодной
и
с
горячей
водой
;
–
испытание
на
изгиб
,
то
есть
приложением
изгибающей
нагрузки
к
верхнему
фланцу
при
закрепленном
нижнем
в
четырех
направлениях
;
–
удар
свободнопадающим
грузом
,
то
есть
горизонтально
закрепленные
за
нижний
фланец
изоляторы
подверга
-
ются
воздействию
одиночного
удара
по
верхнему
флан
-
цу
свободно
падающим
грузом
.
Все
изоляторы
продемонстрировали
заявленную
меха
-
ническую
прочность
,
соответствующую
требованиям
ГОСТ
[3,
стр
. 78],
но
наличие
внутренних
трещин
не
позволяет
часть
из
них
отнести
к
категории
пригодных
к
эксплуатации
из
-
за
возможности
развития
дефектов
в
процессе
эксплу
-
атации
.
Влияние
таких
дефектов
на
эксплуатационную
надеж
-
ность
изолятора
зависит
от
формы
,
размеров
,
ориентации
и
местоположения
дефекта
,
а
также
от
вида
эксплуатацион
-
ной
нагрузки
.
Поскольку
изоляторы
ИОС
-110-400
эксплуати
-
руются
в
«
одноэтажных
»
колонках
,
более
опасными
дефек
-
тами
являются
расположенные
в
нижней
части
изолятора
вблизи
от
боковой
поверхности
в
зоне
механических
напря
-
жений
растяжения
.
Кроме
того
,
при
длительных
эксплуатаци
-
онных
нагрузках
не
исключено
развитие
дефектов
,
имеющих
трещинообразную
часть
.
Обнаруженные
трещины
в
нижних
и
верхних
опасных
сечениях
могут
свидетельствовать
о
воз
-
можном
наличии
заметного
количества
дефектов
по
всему
телу
изоляторов
,
что
подтвердилось
как
при
изломах
изоля
-
торов
в
ходе
испытаний
«
на
изгиб
до
разрушения
»,
так
и
при
разрезании
изолятора
.
При
проведении
ультразвуковой
структурометрии
не
-
которых
изоляторов
было
обращено
внимание
на
гранич
-
ные
скорости
распространения
ультразвуковых
колебаний
для
изоляторов
130
подгруппы
,
заявленной
в
заводской
документации
.
В
связи
с
этим
,
для
определения
состава
применяемой
фарфоровой
массы
в
специализированных
лабораториях
были
проведены
химический
анализ
образ
-
цов
фарфора
и
определение
кажущейся
плотности
и
по
-
ристости
.
Результаты
химического
анализа
показали
,
что
представленная
фарфоровая
деталь
не
может
быть
отне
-
сена
к
подгруппе
130,
а
соответствует
требованиям
ГОСТ
20419-83 [6]
для
глиноземистого
электротехнического
фар
-
фора
подгруппы
«120».
Аналогичные
выводы
были
сделаны
при
определении
кажущейся
плотности
и
пористости
.
Полная
замена
всех
смонтированных
опорно
-
стержне
-
вых
изоляторов
в
действующих
электроустановках
на
новые
без
проведения
диагностирования
методом
ультразвуково
-
го
неразрушающего
контроля
(
как
входного
,
так
и
эксплу
-
атационного
)
с
целью
исключения
аварийных
событий
по
причине
разрушения
опорной
изоляции
не
даст
ожидаемого
результата
.
В
филиале
АО
«
Тюменьэнерго
» —
Сургутские
электрические
сети
технологических
нарушений
,
связан
-
Рис
. 4.
Опорно
-
стержневой
изолятор
ИОС
-110-400
без
нижнего
фланца
Рис
. 5.
Нижнее
«
опасное
»
сечение
,
макроско
-
пический
дефект
—
полость
в
виде
трещины
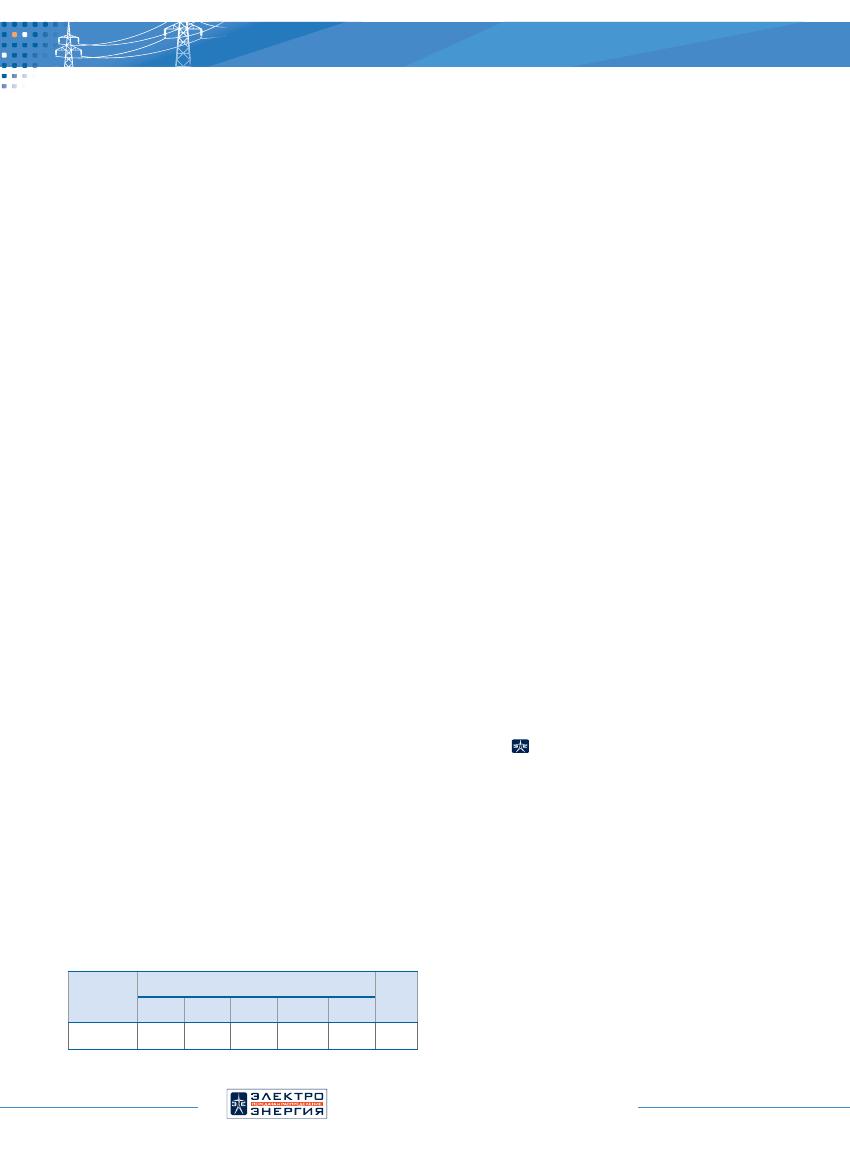
Табл
. 3.
Ультразвуковой
контроль
покрышек
маломасляных
выключателей
Номиналь
-
ное
напря
-
жение
,
кВ
Количество
обследованных
ОСИ
,
шт
.
Всего
ОСИ
,
шт
.
I
сорт
II
сорт
III
сорт
IV
сорт
V
сорт
110
631
167
38
40
–
876
48
Ежеквартальный
спецвыпуск
№
2(9),
июль
2018
ных
с
повреждением
обследованных
фарфоровых
опорно
-
стержневых
изоляторов
,
не
было
.
УЛЬТРАЗВУКОВОЙ
НЕРАЗРУШАЮЩИЙ
КОНТРОЛЬ
ФАРФОРОВЫХ
ПОКРЫШЕК
МАСЛЯНЫХ
ВЫКЛЮЧАТЕЛЕЙ
Надежность
работы
высоковольтных
маломасляных
выклю
-
чателей
типа
ВМТ
110
кВ
в
значительной
степени
зависит
от
качества
изготовления
и
отсутствия
технологических
и
экс
-
плуатационных
дефектов
фарфоровых
покрышек
типа
ПВМо
.
В
филиале
состояние
покрышек
контролируется
мето
-
дом
ультразвукового
неразрушающего
контроля
при
вы
-
полнении
средних
ремонтов
(
проводится
с
периодичностью
,
рекомендуемой
заводом
-
изготовителем
),
а
также
в
процессе
эксплуатации
,
в
зависимости
от
сортности
покрышек
.
В
про
-
цессе
среднего
ремонта
выключателя
выполняется
измере
-
ние
скорости
распространения
ультразвуковых
колебаний
в
фарфоровой
покрышке
и
сравнивается
с
минимальной
(
граничной
)
скоростью
,
при
которой
открытая
микропори
-
стость
в
изделиях
данного
типа
еще
отсутствует
.
Измерение
скорости
распространения
продольных
ультразвуковых
ко
-
лебаний
выполняется
методом
«
сквозного
»
прозвучивания
.
При
проведении
диагностики
в
процессе
эксплуатации
на
смонтированном
оборудовании
измерение
скорости
про
-
изводится
методом
«
сквозного
»
прозвучивания
с
боковой
поверхности
покрышки
в
тангенциальном
направлении
(«
по
хорде
»).
При
контроле
состояния
покрышек
выключателей
в
про
-
цессе
среднего
ремонта
(
демонтированных
или
отдельно
поставляемых
покрышек
)
выявление
и
оценка
сосредото
-
ченных
дефектов
(
трещины
,
сколы
,
зоны
растрескивания
)
производится
при
аксиальном
прозвучивания
ультразвуко
-
вым
импульсным
эхо
-
методом
.
Диагностика
покрышек
маломасляных
выключателей
типа
ВМТ
110
кВ
позволила
значительно
повысить
надеж
-
ность
их
работы
и
избегать
аварийных
ситуаций
по
причине
повреждения
фарфоровых
изделий
.
Некоторые
статистические
данные
ультразвукового
не
-
разрушающего
контроля
покрышек
маломасляных
выключа
-
телей
типа
ВМТ
110
кВ
на
период
с
2009
по
2018
года
пред
-
ставлены
в
таблице
3.
В
эксплуатации
были
оставлены
покрышки
,
отнесенные
к
I
и
II
сортам
.
Заменено
около
15%
от
общего
количества
обследованных
покрышек
маломасляных
выключателей
,
находящихся
в
эксплуатации
.
В
дальнейшем
при
определении
технического
состоя
-
ния
выключателя
в
объем
обязательных
работ
и
проверок
включается
ультразвуковой
неразрушающий
контроль
по
-
крышек
.
В
результате
проведения
ультразвукового
неразрушаю
-
щего
контроля
фарфоровых
опорно
-
стержневых
изоляторов
и
покрышек
маломасляных
выключателей
110
кВ
,
выполнен
-
ных
на
объектах
филиала
АО
«
Тюменьэнерго
» —
Сургут
-
ские
электрические
сети
,
была
сформирована
база
данных
,
что
в
дальнейшем
помогло
нам
давать
правильную
оценку
состояния
изделий
различных
типов
и
заводов
-
изготовите
-
лей
,
учитывая
особенности
технологии
изготовления
,
при
-
меняемой
на
заводе
в
конкретный
период
.
ВЫВОДЫ
1.
Эксплуатационный
контроль
состояния
фарфоровых
изоляторов
в
составе
разъединителей
,
опорно
-
стержневой
изоляции
,
покрышек
маломасляных
выключателей
110
кВ
методом
ультразвукового
неразрушающего
контроля
,
по
-
зволил
свести
к
минимуму
технологические
нарушения
по
причине
разрушения
фарфоровой
изоляции
.
2.
Опытным
путем
подтверждено
совпадение
результатов
по
выявлению
дефектов
ОСИ
при
прозвучивании
как
в
«
ак
-
сиальном
»,
так
и
в
«
радиальном
»
направлениях
.
В
связи
с
этим
можно
предложить
внести
изменения
в
ГОСТ
26099-
84,
относящиеся
к
оценке
качества
фарфора
изоляторов
,
дополнив
его
требованием
о
проведении
ультразвуковой
дефектометрии
в
«
радиальном
»
направлении
.
3.
При
замене
фарфоровых
изоляторов
на
новые
,
не
про
-
шедшие
входной
ультразвуковой
контроль
,
и
невыполнении
эксплуатационного
ультразвукового
контроля
в
действую
-
щих
электроустановках
не
исключается
возможность
за
-
мены
абсолютно
годных
фарфоровых
изделий
на
дефект
-
ные
.
Следовательно
,
массовая
замена
опорно
-
стержневой
изоляции
без
диагностирования
может
не
дать
ожидаемого
результата
.
ЛИТЕРАТУРА
1.
ГОСТ
Р
52034-2008.
Изоляторы
керамические
опорные
на
на
-
пряжение
свыше
1000
В
.
М
.:
Государственный
стандарт
Рос
-
сийской
Федерации
, 2003. 23
с
.
2.
ГОСТ
26093-84.
Изоляторы
керамические
.
Методы
испытаний
.
М
.:
Государственный
комитет
СССР
по
стандартам
, 1986. 15
с
.
3.
Шейкин
А
.
А
.,
Таджибаев
А
.
И
.,
Омельченко
Ю
.
А
.
Технологии
оценки
состояния
фарфоровых
изоляционных
конструкций
высоковольтных
установок
.
СПб
.:
ПЭИПК
Минэнерго
России
,
2002. 74
с
.
4.
Методические
указания
по
контролю
механического
состояния
фарфоровых
опорно
-
стержневых
изоляторов
разъединителей
110
кВ
и
выше
,
и
покрышек
высоковольтных
воздушных
и
мас
-
ляных
выключателей
в
эксплуатации
/
ОАО
«
ФСК
ЕЭС
».
М
.,
2004. 61
с
.
5.
ГОСТ
20419-83.
Материалы
керамические
электротехниче
-
ские
.
Классификация
и
технические
требования
.
М
.:
Государ
-
ственный
комитет
СССР
по
стандартам
, 1985. 8
с
.
Диагностика
и
мониторинг
Оригинал статьи: Оценка эксплуатационной надежности опорно-стержневых изоляторов и покрышек маломасляных выключателей методом ультразвукового неразрушающего контроля
Настоящий информационный материал посвящен вопросу оценки эксплуатационной надежности изоляционных конструкций электроустановок, выполненных из электротехнического фарфора. Для выявления основных видов дефектов, снижающих эксплуатационную надежность опорно-стержневых изоляторов, покрышек маломасляных выключателей, используется ультразвуковой неразрушающий контроль. Представлены некоторые статистические данные результатов обследования в процессе эксплуатации и при входном контроле фарфоровых изделий. Проведено комплексное обследование опорно-стержневых изоляторов разных производителей. В целях подтверждения выявленных дефектов выполнено вскрытие изоляторов и осмотр их составных частей.