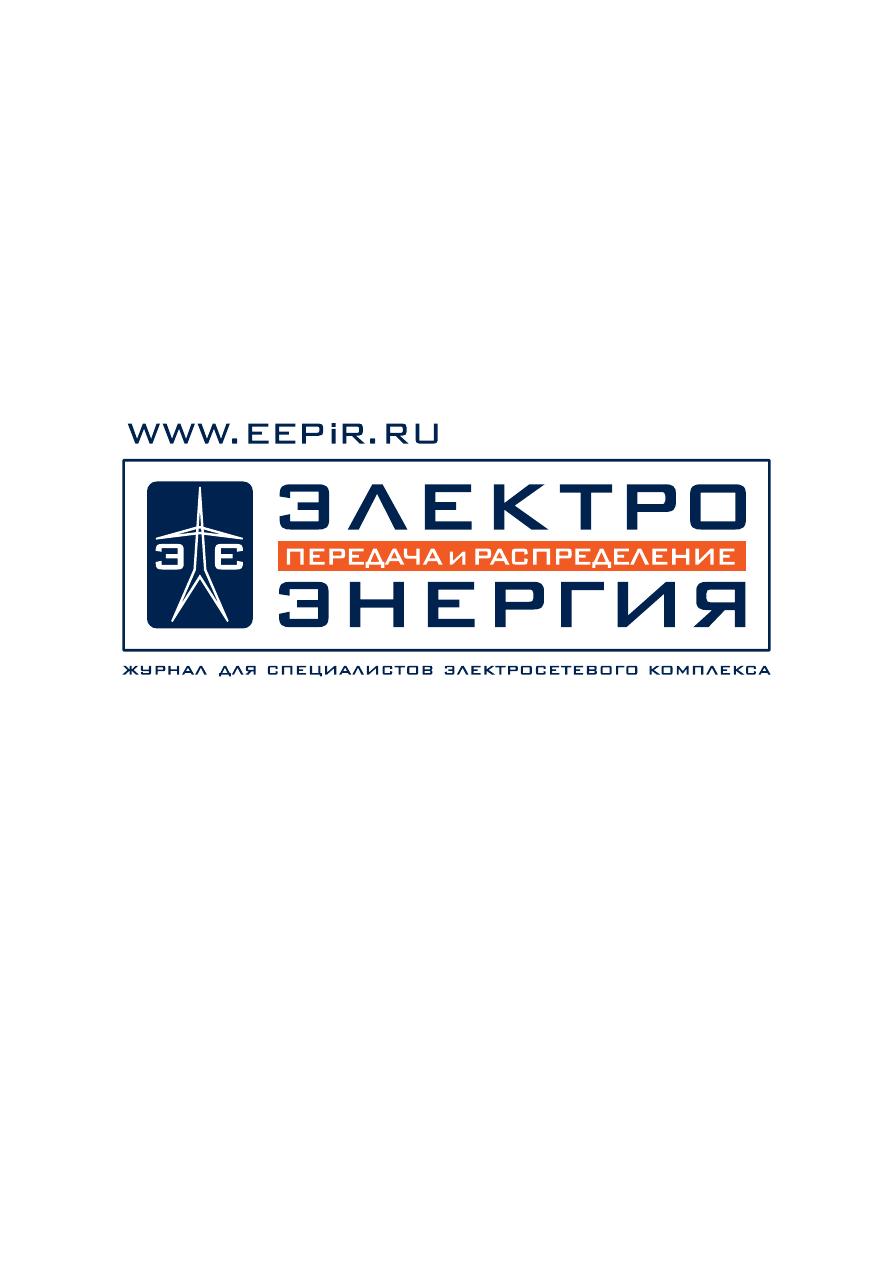
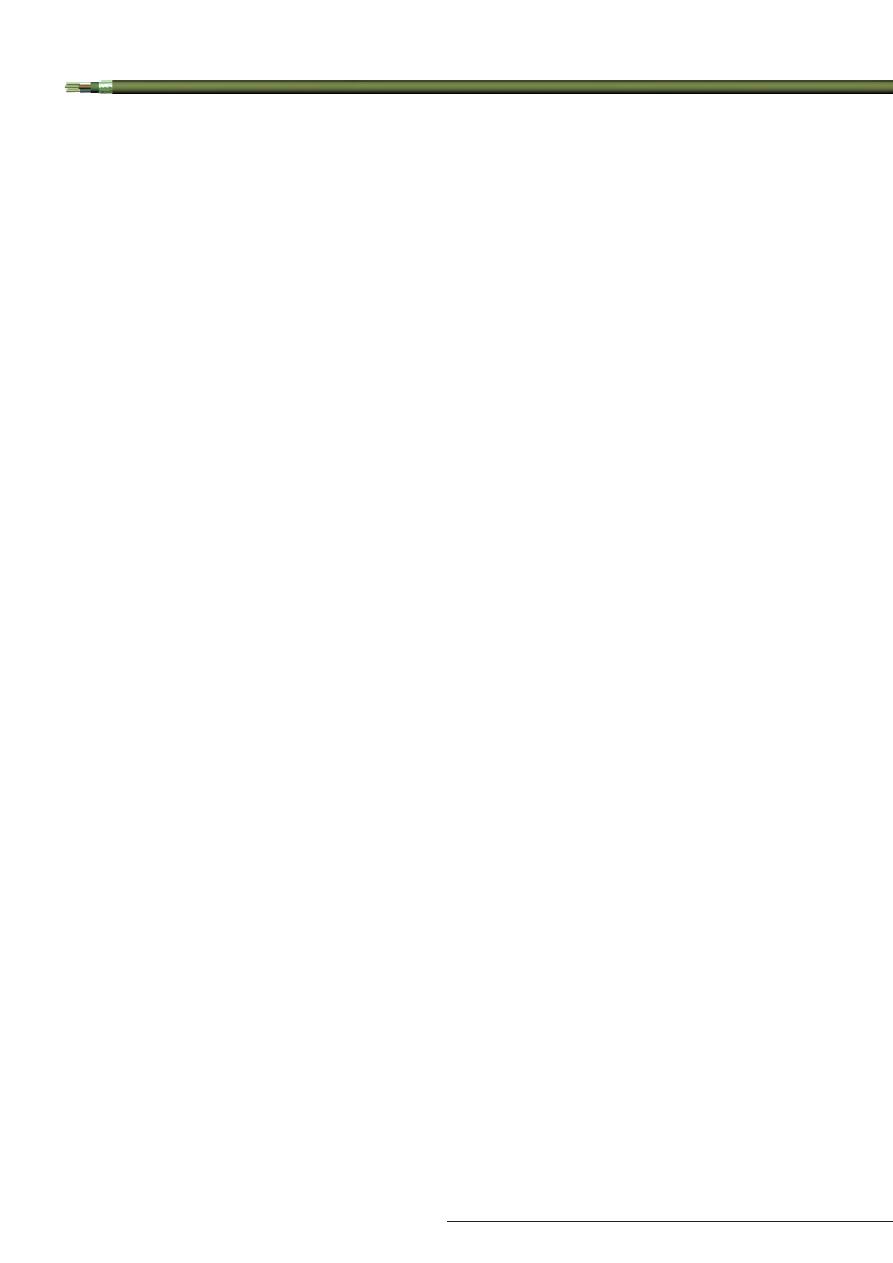
«КАБЕЛЬ-news», № 5, 2013, www.kabel-news.ru
22
Производство
ÎÁÌÎÒÎ×ÍÛÅ ÏÐÎÂÎÄÀ
Новое поколение
эмалированных
алюминиевых обмоточных
проводов
Тадеуш КНЫЧ, Анджей МАМАЛА, Михал ЯБЛОНЬСКИ и Пётр УЛЬЯШ
Э
малированные провода уже давно исполь-
зуются для изготовления обмоток в элек-
трических моторах, трансформаторах и
катушках, но области их применения рас-
ширились с развитием электроники (драйверы жёст-
ких дисков в компьютерах или наушники), также они
активно используются в современных источниках
питания (инверторы или коммутирующие элементы
и источники электрического тока) [1—3]. Эмалиро-
ванные обмоточные провода имеют проводящую
электрический ток сердцевину, покрытую внешним
слоем изоляции из таких материалов, как поливи-
нил, полиуретан, полиэстер, полиэфиримид, полиа-
мидимидные и полиэмидные эмали [4]
.
Требования к эмалированным проводам можно
разделить на пять основных групп: тепловые, элек-
трические, химические, физические и экономиче-
ские. Тепловые свойства определяют поведение
изоляции при повышенных температурах и характер
«теплового удара». Электрические свойства харак-
теризуют диэлектрическую прочность изоляции.
В некоторых случаях требуется химическая устойчи-
вость к воздействию трансформаторного масла или
охлаждающих сред. Физические свойства связаны
с гибкостью, эластичностью или сопротивлением
слоёв изоляции истиранию. Перечисленные параме-
тры определяются условиями работы, в то время как
физические свойства — адгезия к металлу, темпе-
ратура вулканизации или вязкости лака при темпе-
ратурах эксплуатации проводов — являются крайне
важными технологическими факторами. Кроме того,
экономические аспекты, такие, как цена лака, эф-
фективность производства или конечные свойства
провода, также должны приниматься во внимание.
Детальный анализ различных видов эмалей пред-
ставлен в ряде публикаций [5—7].
Медь является наилучшим материалом после
серебра для применения в электротехнических из-
делиях благодаря высокой проводимости. Для ис-
пользования в обмотках катушек рассматривалось
применение алюминия, но такое решение оказалось
экономически нецелесообразным, и в настоящее
время эмалированные медные провода широко при-
меняются как в силу экономических факторов, так
и за счёт некоторых критически важных технологи-
ческих особенностей. Обычная электролитическая
технически чистая медь наиболее часто использу-
ется для изготовления обмоток. Для этих же целей
довольно часто применяется электролитическая
медь, не содержащая кислорода. Фундаментальный
анализ влияния качества меди на свойства эмалиро-
ванных проводов опубликован в работе [8]. В зави-
симости от условий работы эмалированные провода
различаются по термическим свойствам, механиче-
ской прочности, способности подвергаться пайке и
самосклеиваться. Готовые эмалированные провода
проходят многочисленные лабораторные испытания
[9—14].
БАЗОВЫЙ АНАЛИЗ
Цена на медь существенно выросла после 2004 г.
Это обстоятельство сделало дешёвый алюминий
привлекательной альтернативой, но применение
этого материала связано с техническими проблема-
ми удовлетворения наиболее важных требований.
Для решения этих проблем было проведено тща-
тельное исследование нового поколения алюминие-
вых эмалированных проводов.
В табл. 1 показаны фундаментальные различия
чистой меди и алюминия при использовании этих ме-
таллов для изготовления эмалированных проводов.
Причиной отличий являются физические свойства
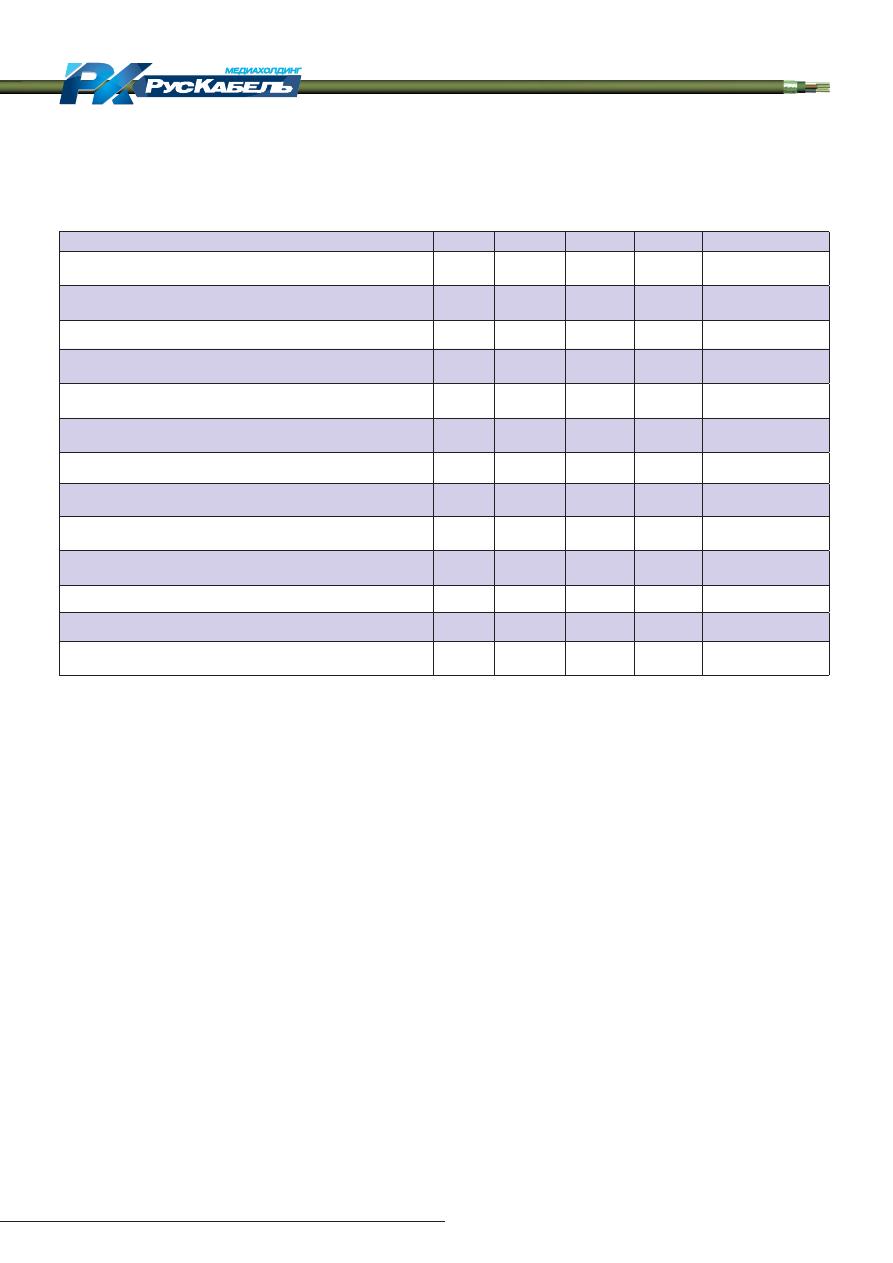
«КАБЕЛЬ-news», № 5, 2013, www.kabel-news.ru
23
Производство
ÎÁÌÎÒÎ×ÍÛÅ ÏÐÎÂÎÄÀ
Табл. 1. Сравнение алюминия и меди, используемых для изготовления эмалированных проводов
(x — алюминий лучше или разница отсутствует)
Параметры
Cu
Al
AlCu
Баланс
Эффект
Удельное электрическое сопротивление при 20
о
С,
нОм·м
17,2
27,3 1,6
–
Техническое
обслуживание
Начальное сопротивление провода длиной 1 км,
одинаковая величина для меди и алюминия, мОм·км
172
172
1
0
х
Тепловой коэффициент сопротивления, 1/K
0,004
0,004
1
0
х
Поперечное сечение провода, мм
2
1
1,6
1,6
–
Техническое
обслуживание
Диаметр провода, мм
1,13
1,43
1,3
–
Техническое
обслуживание
Масса провода длиной 1 км, г
432
0,5
+
Техническое
обслуживание
Цена металла, долл. США
0,2
0,9
0,15
+
Экономия
Объём лака при изоляции толщиной 50 мкм, мм
3
/км
264
265 1,3 –
Экономия
Теплоёмкость, Дж/гК
0,385
0,9
2,3
+
Техническое
обслуживание
Допустимый ток, адиабатический режим, А
0,26
0,27
1,1
+
Техническое
обслуживание
Предел текучести, МПа
100
40
0,4
–
Технология
Модуль Юнга материала, ГПа
120
70
0,6
0
х
Упругая деформация, %
0,8
0,6
0,8
+
Техническое
обслуживание
материалов. В первой строке показано, что удельное
электрическое сопротивление меди намного меньше,
чем у алюминия. Во второй строке даны результаты
анализа свойств алюминиевых и медных эмалиро-
ванных проводов, обладающих одинаковым сопро-
тивлением. В п. 4 и 5 табл. 1 показано, что площадь
поперечного сечения и диаметр алюминия больше,
чем у меди, что является недостатком при миниатю-
ризации. Однако из п. 6 видно, что масса таких про-
водов намного меньше, что является жизненно важ-
ным фактором в тех случаях, когда снижение массы
продукта имеет критическое значение. Из п. 7 видно,
что стоимость алюминия намного меньше стоимости
меди. Рассмотрение стоимости 1 км эмалированного
провода показывает, что цена эмалированных алю-
миниевых проводов намного меньше цены медных
проводов, несмотря на больший объём переработан-
ного материала и на большее количество использо-
ванного лака. Теплоёмкость алюминия примерно в
два раза больше, чем у меди. Это очень важно, по-
скольку для увеличения температуры той же массы
алюминия требуется намного больше энергии. В рас-
смотренных областях применения повышение тем-
пературы вызывается протеканием тока. Предельно
допустимый ток для обоих проводов будем считать
одинаковым. Для сравнения в табл. 1 приведены рас-
считанные адиабатические условия — допустимая
величина тока равна корню квадратному из массы,
теплоёмкости и увеличения температуры продукта,
разделённых на сопротивление провода. Это обстоя-
тельство имеет большое значение в электрических
устройствах из-за больших плотностей тока и темпе-
ратурных перегрузок.
Следующая группа параметров, связанных с тех-
нологическими процессами изготовления проводов
или обмоток, таких, как механические свойства,
имеет большое значение для процесса нанесения
эмали и во время изготовления обмоток. В то вре-
мя как расчётное упругое последействие алюминия
меньше, чем у меди (требуется только изменение
настройки оборудования), худшие механические
свойства алюминия создают реальные проблемы
при намотке тонких проводов. Данный анализ осно-
ван на базовых физических свойствах алюминия и
меди. Существуют и другие причины, по которым
алюминию отдаётся предпочтение для изготовле-
ния обмоточных проводов. Во многих электронных
устройствах частота электрического тока высока и
скин-эффект определяет характер протекания тока
в материале. В подобных случаях импеданс алюми-
ниевых и медных катушек одинаков, но алюминие-
вые катушки легче и дешевле [1].
Другой особенностью эмалированных алюми-
ниевых проводов является более продолжительный
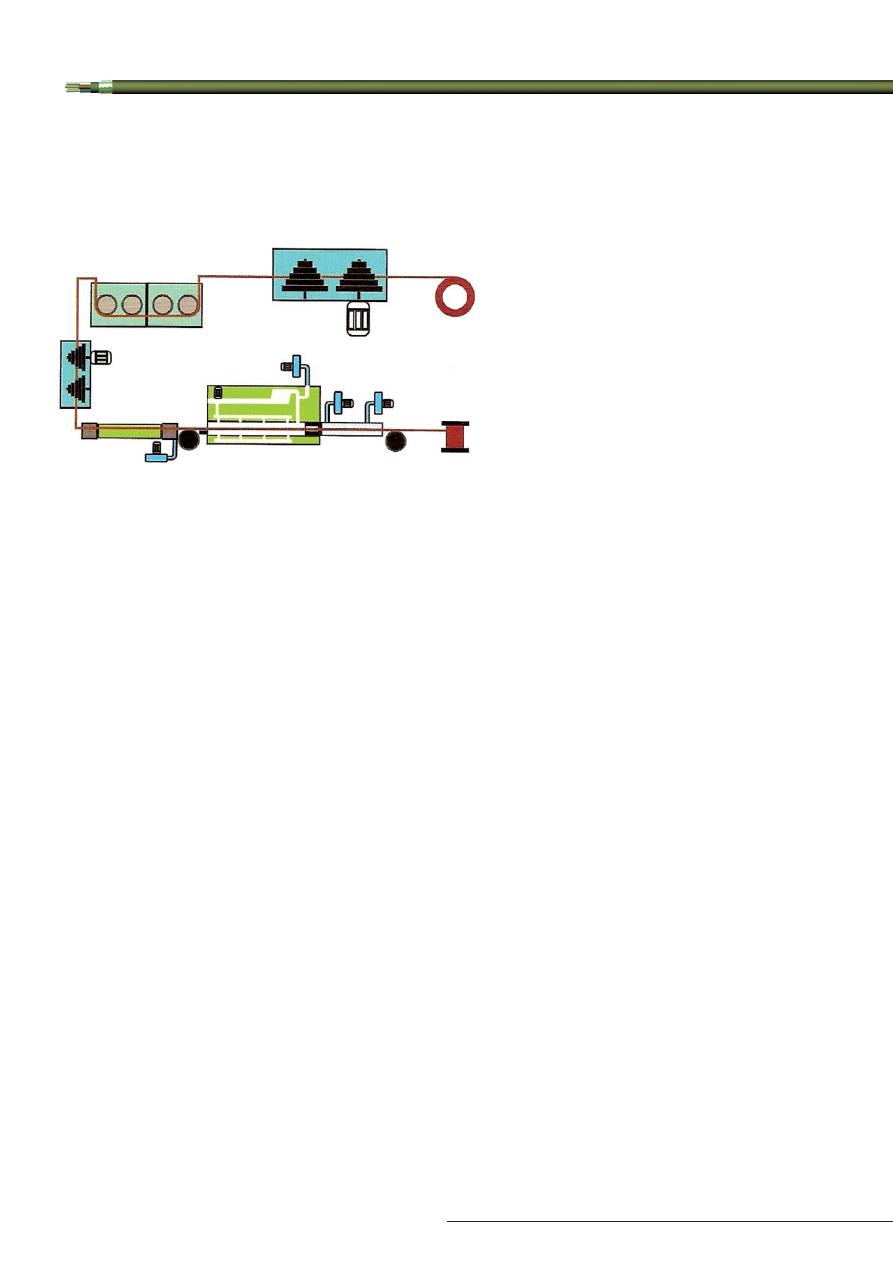
«КАБЕЛЬ-news», № 5, 2013, www.kabel-news.ru
24
срок их службы. Слой изоляции на проводах не явля-
ется идеально однородным. Существуют небольшие
дефекты, трещины и микроотверстия, которые де-
лают возможным контакт окружающей атмосферы
и металлической жилы. Во время процесса вулкани-
зации возникают некоторые газообразные продук-
ты, которые могут вступать в реакцию с металлом,
что приводит к образованию окисей металла на гра-
ничном слое между металлом и изоляцией. На по-
верхности алюминия быстро образуется очень тон-
кий слой окислов, который защищает внутренние
части от окисления, а на поверхности меди образу-
ются различные виды пористых окислов, и процесс
окисления проникает глубоко в материал. При этом
локальные поперечные сечения медного проводни-
ка уменьшаются, температура повышается в резуль-
тате нагрева джоулевым теплом, а характеристики
продукта ухудшаются. Таким образом, как показали
детальные исследования [15], алюминий обладает
большим сроком службы.
Ещё одной проблемой являются структура и
свойства материала для конкретных применений.
Эмалированные провода достаточно мягкие, но
тепловые удары и продолжительный нагрев вслед-
ствие протекания в структуре материала опреде-
лённых физических процессов, сопровождающихся
диффузией (причина — нагрев), могут вызывать
микроскопические изменения. Прочность на раз-
рыв уменьшается. Исследования показали, что
в процентном отношении у медных проводов
уменьшение прочности на разрыв больше, чем
у алюминиевых [16].
ПРОИЗВОДСТВО ЭМАЛИРОВАННЫХ
АЛЮМИНИЕВЫХ ПРОВОДОВ
Для изготовления алюминиевого эмалиро-
ванного провода используются два основных
технологических процесса: волочение и эмали-
рование, при этом технология производства не
является простой (рис. 1).
Поскольку конечные диаметры проводов
различны (больше и меньше 1 мм), возможны
два варианта выбора, связанных с конструк-
циями волочильных машин. Классическое во-
лочение алюминия на волочильной машине
позволяет изготавливать провода с конечным
диаметром более 1,2 мм. В процессе волочения
обычно используется масло с высокой вязко-
стью при скоростях изготовления свыше 30 м/с.
Система смазки делает поверхность провода
непригодной к нанесению эмали, при этом соз-
даётся необходимость в специальных линиях
очистки, которые дают возможность наносить
эмаль в специальных одноэтапных волочиль-
ных машинах. Провода меньшего диаметра из-
готавливаются на машинах дополнительного
волочения, сопряжённых с машинами для нанесения
эмали. Поскольку процесс эмалирования должен
проходить при пониженных скоростях, волочильные
машины вместе с оборудованием для эмалирования
могут работать со смазочным материалом в виде
водных эмульсий при наличии в нём масла с помо-
щью горячей воды и пара. Между двумя процессами
волочения возможна термообработка провода для
восстановления пластичности материала. После ре-
кристаллизации в паровой сушилке готовый провод
проходит через камеру для нанесения эмали, где лак
вулканизируется. Эмаль наносится с помощью спе-
циальных фильер при многократном проходе про-
вода. Качество продукта на выходе определяется
числом проходов, скоростью и температурой мате-
риала. Температуры и продолжительность вулкани-
зации эмали отличаются величинами по сравнению
со случаем использования меди. Более того, из-за
более слабой адгезии эмали к поверхности алюми-
ния иногда необходимо использовать специальную
грунтовку.
Технология волочения алюминия и меди отлича-
ется в двух аспектах. Во-первых, для обеспечения
смазки для меди используется эмульсия, а для алю-
миния — масло, и несмотря на то, что масло имеет
высокую адгезию к поверхности провода, эта по-
верхность должна быть тщательно очищена перед
эмалированием. Во-вторых, отличием является ис-
Рис. 1. Схема технологического процесса изготовления
эмалированного провода
1 — материал на входе (алюминиевый пруток);
2 — механизм влажной прокатки;
3 — система очистки;
4 — машина промежуточного влажного волочения,
сопряжённая с оборудованием для эмалирования;
5 — камера с горячей водой;
6 — паровая сушилка;
7 — узел для нанесения эмали;
8 — оборудование для вулканизации эмали;
9 — камера для охлаждения;
10 — конечный продукт (эмалированный алюминиевый провод).
1
3
2
10
9
8
7
6
5
4
Производство
ÎÁÌÎÒÎ×ÍÛÅ ÏÐÎÂÎÄÀ
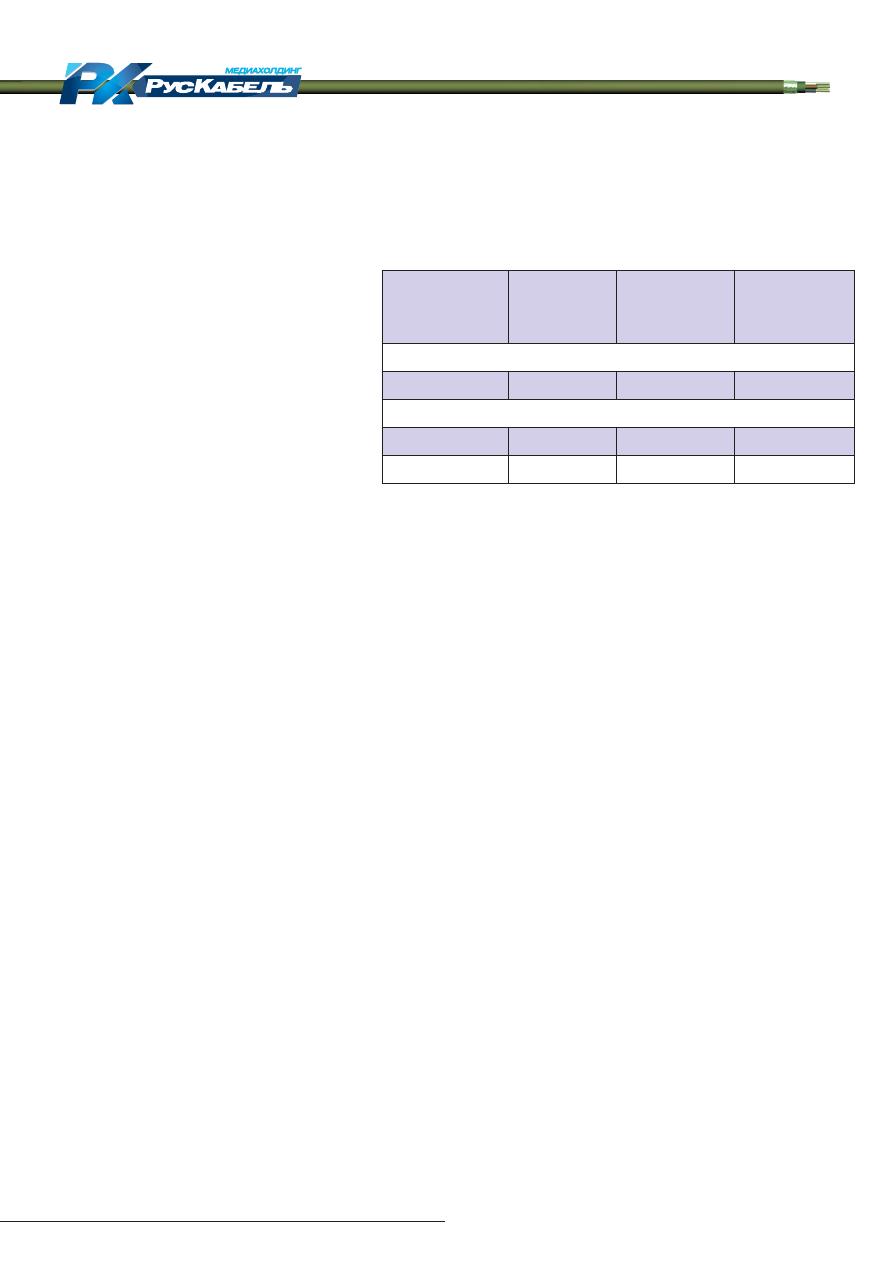
«КАБЕЛЬ-news», № 5, 2013, www.kabel-news.ru
25
Табл. 2. Технические требования к алюминию и
алюминиевым сплавам для изготовления эмалированных
проводов в соответствии со стандартами EN и NEMA
(* — зависит от диаметра провода)
Номинальное
удельное
сопротивление,
нОм.м
Минимальное
удлинение, %
Минимальный
предел
текучести,
МПа
Минимальный
предел
прочности на
разрыв, МПа
EN 6037
27,89
10—15* —
70—90*
ANSI/NEMA 100-2008
27,898
12—15*
48,3—55,2*
89,6
28,450
12—15*
48,3—55,2*
89,6
пользование разного оборудования для
отжига (при применении меди использует-
ся оборудование непрерывного отжига, а
алюминия — традиционное).
Ещё одной проблемой является реак-
ция материала при высоких температурах
во время вулканизации лака в оборудо-
вании для нанесения эмали. Для типовых
эмалей предпочтительно использование
высоких температур, но материалы, из ко-
торых изготавливаются провода, не дают
возможности применять высокотемпера-
турные режимы — при этом необходимы
специальные составы эмали. Кроме того,
поскольку температура вулканизации при
применении алюминия высока, для дости-
жения гарантированных свойств конечно-
го продукта необходимо использовать спе-
циальные материалы.
ТРЕБОВАНИЯ К АЛЮМИНИЮ
Требования к свойствам алюминия сформулиро-
ваны во многих национальных стандартах, основ-
ными из которых являются: EN [10], общепринятый
в Европе, и NEMA [17], применяемый в Северной
Америке. В табл. 2 приведены типовые требования
к механическим и электрическим свойствам алюми-
ния для изготовления эмалированных проводов в
соответствии со стандартами EN и NEMA. Данные,
приведённые в этой таблице, относятся к круглым
проводам.
Анализ величин, приведённых в табл. 2, пока-
зывает, что сочетание характеристик эмалирован-
ных проводов нетипично для термообработанного
(полностью отожжённого) материала. Например,
стандартный мягкий алюминий (EN AW 1370), класс
обработки О (EN 515), имеет удельное электриче-
ское сопротивление в диапазоне 27,3—27,6 нОм·м,
предел прочности на разрыв приблизительно 60—
80 МПа и удлинение на уровне 20—40%. Эти харак-
теристики заметно отличаются от приведённых в
табл. 2.
Удлинение эмалированного провода намного
меньше, сопротивление немного больше, а предел
прочности на разрыв такой же или выше, как у мяг-
кой проволоки. Американские стандарты допускают
применение сплавов, обладающих меньшим, чем
чистый металл, сопротивлением.
Из данных табл. 2 видно, что для изготовления
эмалированных проводов может быть использо-
ван не только чистый алюминий, но и алюминий со
специальными микродобавками; также возможно
применение сплавов алюминия. Существуют че-
тыре причины, по которым вместо чистого алюми-
ния используют сплавы и легированный алюминий.
Первая — лучшие механические свойства сплавов
в окружающих условиях хорошо подходят для про-
цесса намотки, когда провод передвигается при
натяжении и изгибается при формировании витков
катушки. Такие материалы в большей степени по-
зволяют достигать соответствия продукта техниче-
ским требованиям. Вторая — лучшие механические
свойства сплавов при высоких температурах. Во
время нанесения эмали провод нагревается и до-
полнительно растягивается при вулканизации лака,
при этом процессы пластической деформации и
ползучести вызывают изменения диаметра прово-
да. Третья причина — более высокая температура
рекристаллизации сплавов. До нанесения лака на
провод материал рекристаллизуется в паровой су-
шилке, и сплав обладает более высокой прочностью
на разрыв в начале процесса нанесения эмали. Чет-
вёртая причина — некоторые сплавы обладают бо-
лее высокой пластичностью при волочении по срав-
нению с чистым алюминием. Это имеет большое
значение для электротехнических устройств, в кото-
рых используются тонкие провода (диаметр от 0,8 до
0,2 мм). Перечисленные выше причины гарантируют
соответствующее эксплуатационным требованиям
поведение провода в процессах волочения, эмали-
рования и производства электротехнических узлов с
обмоточными проводами.
МАТЕРИАЛЫ, В ОСНОВЕ КОТОРЫХ
ИСПОЛЬЗУЕТСЯ АЛЮМИНИЙ
Как было отмечено выше, чистый алюминий,
алюминий с микродобавками и алюминиевые спла-
вы могут быть использованы для изготовления алю-
миниевых эмалированных обмоточных проводов.
Комплексный анализ материалов для применения
в электротехнике, в основе которых использован
алюминий, и исследование их свойств были про-
ведены Иричибаром (Iricibar) [18] и Кнычем (Knych)
[19]. В настоящем разделе рассматриваются только
Производство
ÎÁÌÎÒÎ×ÍÛÅ ÏÐÎÂÎÄÀ
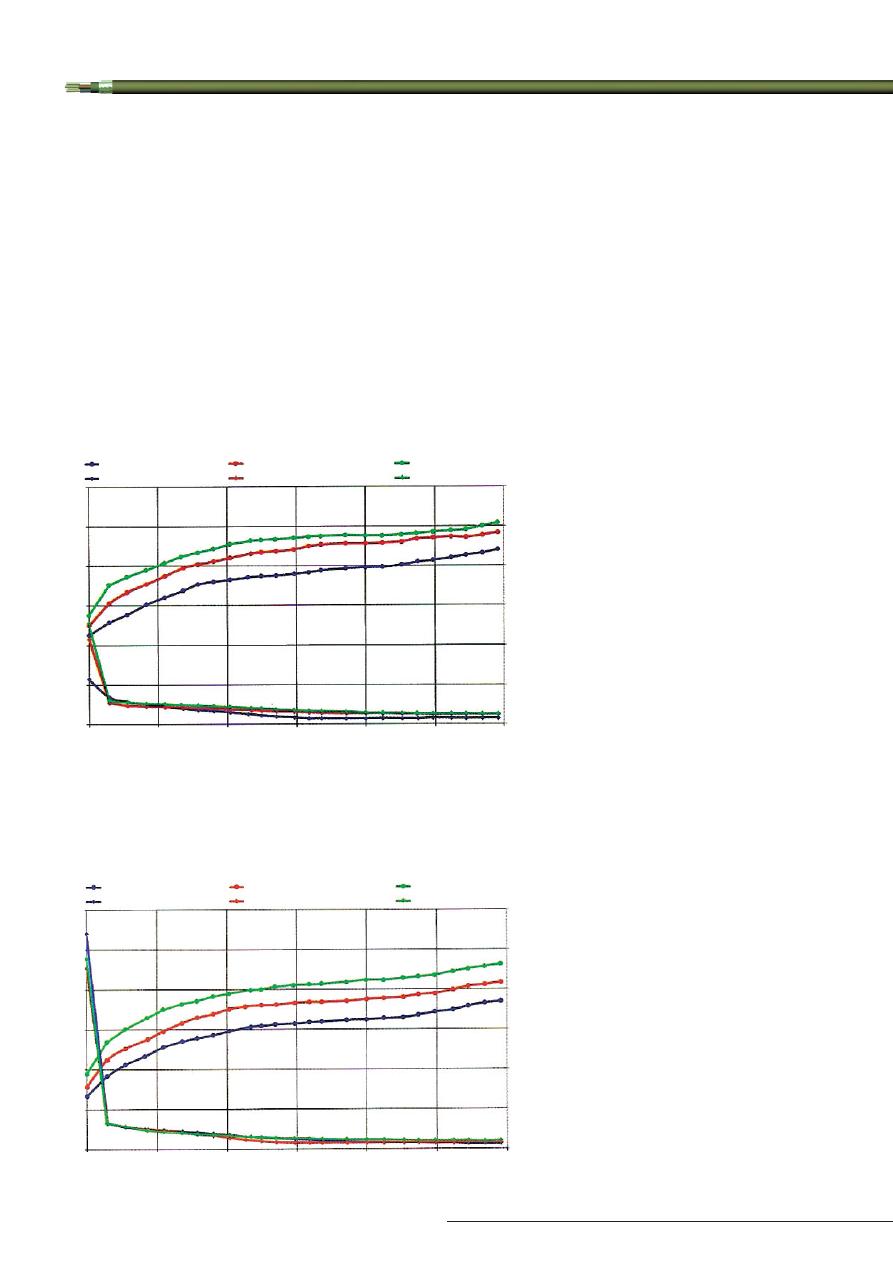
«КАБЕЛЬ-news», № 5, 2013, www.kabel-news.ru
26
новые материалы, выбранные для изготовления об-
моточных проводов.
Алюминиевые провода, предназначенные для
эмалирования, должны обладать требуемыми меха-
ническими свойствами и хорошей электропровод-
ностью. Примеси в алюминии уменьшают электро-
проводность материала, но элементы примеси в
твёрдом растворе вызывают большее уменьшение
электропроводности, чем элементы, находящие-
ся в различных фазах. Тяжёлые элементы, такие,
как V, Cr, Mn и Zr, значительно ухудшают электро-
проводность, их наличие в сплавах, применяемых
в электротехнических изделиях, недопустимо. Но
такие элементы, как B, Cu, Mg и Si, проводимость
снижают незначительно. Некоторые элементы при
одинаковых уровнях концентрации могут находиться
в твёрдом растворе или второй фазе в соответствии
с условиями термообработки, и твёрдость материа-
ла должна анализироваться при рассмотрении во-
просов технологии. Элементы в твёрдом растворе
оказывают положительное влияние
на увеличение температуры рекри-
сталлизации и вызывают небольшое
увеличение прочности, но элементы,
расположенные вне алюминиевой
матрицы, вызывают большее уве-
личение прочности на разрыв. Во
многих случаях химический состав
материала для изготовления эмаль-
проводов является компромиссным
с точки зрения обеспечения требуе-
мой электропроводности, разрывной
прочности и температуры рекри-
сталлизации.
Первая группа сплавов, пред-
ставляющая больший интерес, чем
чистый алюминий, — сплавы AlFe.
Анализ диаграммы состояний Al —
Fe показывает, что растворимость
железа в алюминии мала (около
0,04% при эвтектической темпе-
ратуре и пренебрежимо мала при
температуре окружающей среды).
Вследствие малой растворимости
железа в алюминии имеет место
лишь небольшое уменьшение элек-
тропроводности. Добавка железа
к алюминию увеличивает пластич-
ность при волочении материала.
В чистом техническом алюминии в
небольших количествах присутству-
ет кремний. После рекристаллизации
он образует микрочастицы кремния,
которые являются хрупкими, ухуд-
шают качество алюминия и ограни-
чивают пластичность при волочении.
Железо образует новую фазу AlFeSi,
и эта проблема устраняется. Железо
может изменить структуру во время
литья, однако при уровнях концен-
трации, представляющих интерес
для данной работы, этот эффект не-
значителен. На рис. 2—3 показаны
изменения предельной разрывной
прочности и удлинения во время ис-
пытаний на растяжение как функция
Рис. 2. Предельная прочность на разрыв и удлинение — общая
зависимость от величины натяжения для сплавов Al и AlFe;
материал на входе — класс F (готовая заготовка)
Предел проч. на разрыв, AlFe1,1
Удлинение, AlFe1,1
Общая действующая нагрузка
Предельная про
чнос
ть на разрыв, МПа
У
длинение при разрыве, %
Предел проч. на разрыв, Al
Удлинение, Al
Предел проч. на разрыв, AlFe0,5
Удлинение, AlFe0,5
0
2
1
3
4
5
6
300
250
200
150
100
50
0
45,0
37,5
30,0
22,5
15,0
7,5
0,0
Рис. 3. Предельные прочность на разрыв и удлинение — общая
зависимость от величины натяжения для сплавов Al и AlFe;
материал на входе — класс термообработки О
(материал после отжига)
Предел проч. на разрыв, AlFe1,1
Удлинение, AlFe1,1
Общая действующая нагрузка
Предельная про
чнос
ть на разрыв, МПа
У
длинение при разрыве, %
Предел проч. на разрыв, Al
Удлинение, Al
Предел проч. на разрыв, AlFe0,5
Удлинение, AlFe0,5
0
2
1
3
4
5
6
300
250
200
150
100
50
0
45,0
37,5
30,0
22,5
15,0
7,5
0,0
Производство
ÎÁÌÎÒÎ×ÍÛÅ ÏÐÎÂÎÄÀ
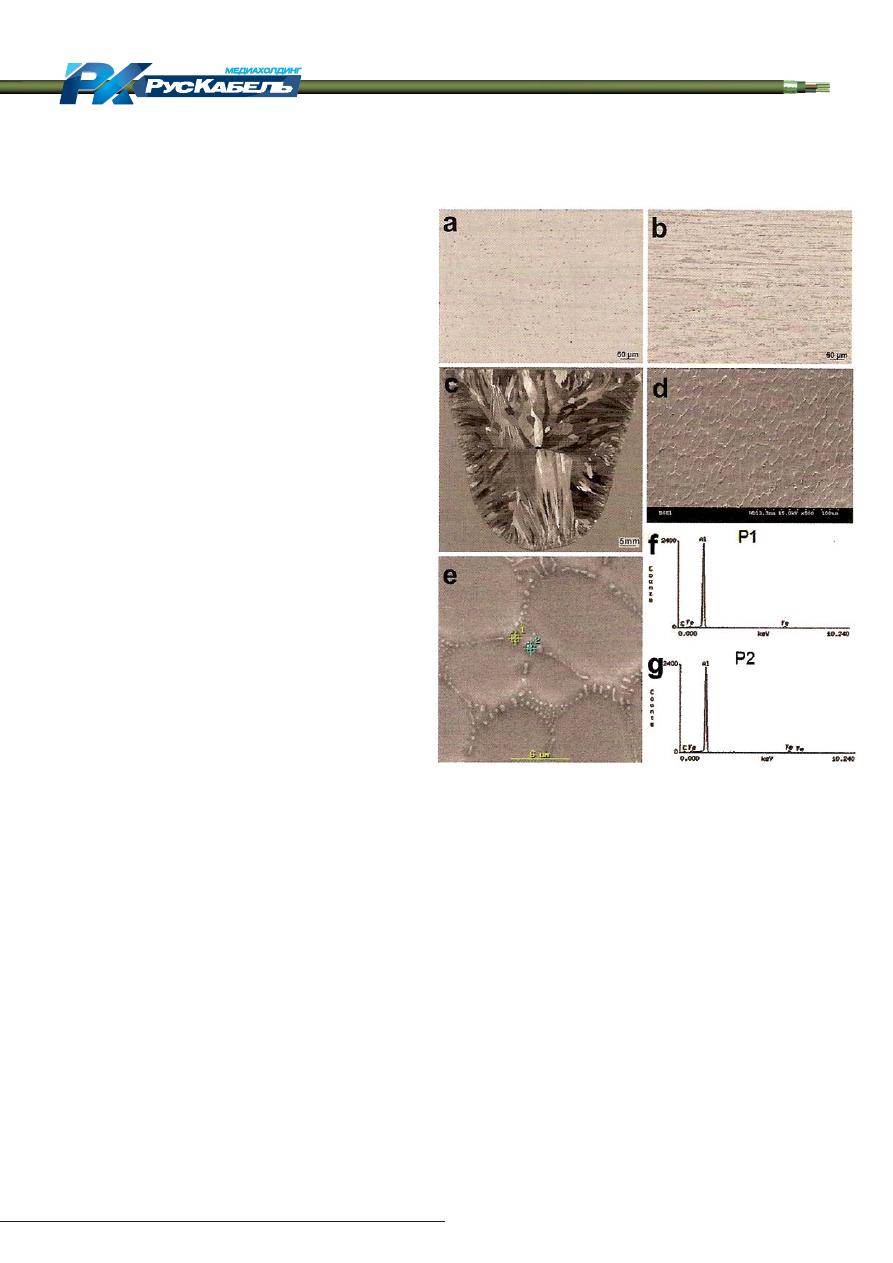
«КАБЕЛЬ-news», № 5, 2013, www.kabel-news.ru
27
а — микроструктура алюминиевого прутка,
термообработка — класс F;
b — микроструктура прутка из сплава AlFe1,1,
термообработка – класс F;
с — макроструктура сплава AlFe1,1, после отливки;
d — фото со сканирующего электронного микроскопа
(СЭМ) микроструктуры сплава AlFe1,1, после отливки;
е — фото со сканирующего электронного микроскопа
(СЭМ) микроструктуры сплава AlFe1,1, после отливки;
f — химический анализ частиц в сплаве AlFe1,1, после
отливки, из рис. 4е — точка 1;
g — химический анализ частиц в сплаве AlFe1,1, после
отливки, из рис. 4е — точка 2.
Рис. 4. Микроструктуры и макроструктуры Al
и сплавов AlFe
общего усилия растяжения во время процесса
волочения сплавов AlFe c различными уровнями
концентрации железа (0,5% Fe и 1,1% Fe). Для
сравнения показаны такие же зависимости для
чистого алюминия (0,07% Fe). На рис. 2 пред-
ставлены материалы, термообработка по классу
F (состояние поставки), а на рис 3 — материалы
после термообработки по классу О [20] (после ре-
кристаллизации).
Представленные данные показывают, что ре-
зультаты деформационного упрочнения всех ма-
териалов, рассмотренных в настоящем анализе,
аналогичны (наклон линий по отношению к оси,
на которой показано усилие). Во время несколь-
ких начальных проходов при волочении рост
прочности выше, а при последующих проходах
прочность является почти линейной функцией от
деформирующей нагрузки. Испытанные материа-
лы обладают различными начальными свойства-
ми. Увеличение концентрации железа приводит
к повышению прочности на разрыв материала,
полученного от производителя, после рекристал-
лизации, а твёрдость материалов соответствует
твёрдости твёрдотянутой проволоки. Более ин-
тересные выводы связаны со свойствами пла-
стичности материала (представлены данными об
удлинении при испытаниях на разрывную проч-
ность). Начальная пластичность материала (в со-
стоянии поставки) возрастает при росте концен-
трации железа. Удлинение проволоки из сплава
AlFe после рекристаллизации меньше, чем у чи-
стого алюминия, но всё ещё не выходит за рамки
требований (табл. 2). Пластичность материалов
после холодной прокатки одинакова у всех мате-
риалов, но она всё ещё больше, чем у сплавов с
железом. При классическом подходе удлинение
во время испытаний на разрывную прочность кор-
релируется с формуемостью и ожидается лучшее
поведение сплава по сравнению со случаем ис-
пользования чистого алюминия.
Конечная разрывная прочность рассматривае-
мых сплавов после рекристаллизации (прутки по-
сле термообработки по классу О) также является
функцией содержания железа. Разрывная проч-
ность чистого алюминия меньше, чем 70 МПа,
сплава AlFe0,5 — 80 МПа, в то время как сплав
AlFe1,1 имеет прочность на разрыв 105 МПа. Эта
величина намного выше, чем требования, приведён-
ные в табл. 2. В этом случае достаточной является
добавка 0,5% алюминия. Как видно из табл. 2, чи-
стый алюминий в мягком состоянии имеет недоста-
точную разрывную прочность. Значение рассматри-
ваемого параметра имеет очень большое значение
вследствие особенностей процесса эмалирования,
в ходе которого провод натягивается при высокой
температуре, и при этом
происходит отжиг.
Для определения причин изменения свойств Al
и AlFe необходимо исследовать вид микрострукту-
ры. На рис. 4а и 4b показано продольное сечение
прутков, изготовленных методом литья с последую-
щей прокаткой. На рис. 4 видно различие структур
чистого алюминия (рис. 4а) и сплава AlFe (рис. 4b).
В матрице сплава алюминия AlFe присутствуют не-
большие частицы. На основе диаграммы состояний
можно сказать, что матрица эвтектически дефор-
Производство
ÎÁÌÎÒÎ×ÍÛÅ ÏÐÎÂÎÄÀ
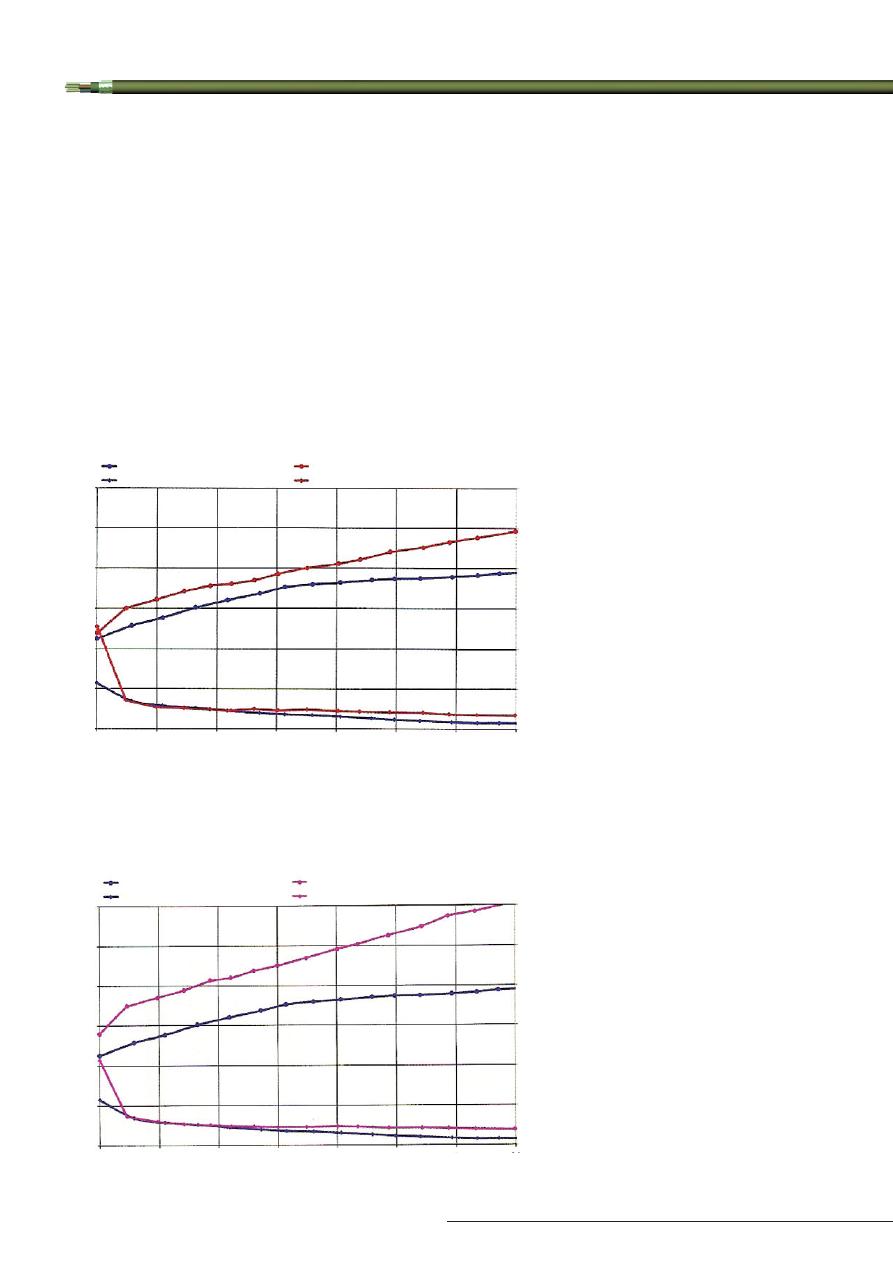
«КАБЕЛЬ-news», № 5, 2013, www.kabel-news.ru
28
мирована в процессе горячей прокатки и по форме
похожа на ленточки. Для более детального изучения
частиц представлены разные структуры AlFe после
литья. На рис. 4с представлена макроструктура спла-
ва AlFe после завершения процесса непрерывного
литья, которая относится к типичным структурам с
дендритами. При большем увеличении (рис. 4d) луч-
ше видно, что на границах зёрен имеется большое
количество частиц. На рис. 4е представлена морфо-
логия частицы, а на рис 4f — результат химическо-
го анализа частиц. Диаграмма состояний и химиче-
ский анализ показывают, что частицы имеют размер
около 1 мкм в фазе Al
x
Fe (равновесная фаза Al
3
Fe).
Эти частицы располагаются на границах зёрен по-
сле литья, а после горячей прокатки прутка более
равномерно распределяются в материале (рис. 4b).
Частицы, рассматриваемые в данном анализе, игра-
ют важную роль в рекристаллизации материала, и
их размер, по всей вероятности, достаточно мал для
того, чтобы замедлить рекристаллизацию.
Второй группой сплавов, хо-
рошо подходящих для процесса
эмалирования, являются сплавы
AlFeMg с небольшими добавками
магния (0,1%). Сплавы AlMg об-
ладают превосходной способно-
стью деформироваться и высокой
коррозионной стойкостью. Магний
хорошо растворяется в алюминии
и содержится в твёрдом растворе.
Однако присутствие кремния (есте-
ственная примесь в алюминии)
делает возможной преципитацию
Mg
2
Si. Это ещё один элемент, ко-
торый делает невозможным суще-
ствование свободного кремния в
алюминии. Удельное электриче-
ское сопротивление не слишком
велико (максимум 0,5 нОм·м при
вычислении по закону Нордхайма),
и ожидаема высокая температура
рекристаллизации (хорошо извест-
но, что добавка 1% магния увеличи-
вает температуру рекристаллиза-
ции). Перриман [21] предполагает,
что в процессе рекристаллизации
алюминия с присадкой магния ско-
рость роста новых зёрен в 10 раз
ниже, чем при рекристаллизации
чистого алюминия. Новые зёр-
на возникают быстрее, чем в чи-
стом алюминии, но сложный про-
цесс рекристаллизации протекает
медленнее. Это очень благопри-
ятное обстоятельство, поскольку
во время отжига в оборудовании
для нанесения эмали образуются
зёрна меньшего конечного разме-
ра и материал обладает большим
пределом текучести (соотношение
Холла-Питча). Добавка магния за-
метно повышает уровень затвер-
девания сплава. На рис. 5, где
показана взаимосвязь между проч-
ностью на разрыв и удлинением во
время испытания на разрыв, мож-
Предел прочности на разрыв, AlFe0,6Mg0,1
Удлинение, AlFe0,6Mg0,1
Общая действующая нагрузка
Предельная про
чнос
ть на разрыв, МПа
У
длинение при разрыве, %
Предел прочности на разрыв, Al
Удлинение, Al
0,0
0,5
1,0
1,5
2,0
2,5
3,0
3,5
300
250
200
150
100
50
0
45,0
37,5
30,0
22,5
15,0
7,5
0,0
Рис. 5. Предельная прочность на разрыв и удлинение — общая
зависимость от усилия растяжения для алюминия и сплава
AlFe0,6Mg0,1, материал на входе: термообработка —
класс F (после изготовления)
Рис. 6. Предельная прочность на разрыв и удлинение — общая зави-
симость от усилия растяжения для алюминия и сплава AlFe0,5Cu0,2,
материал на входе: термообработка — класс F
(после изготовления)
Предел прочности на разрыв, AlFe0,5Cu0,2
Удлинение, AlFe0,5Cu0,2
Общая действующая нагрузка
Предельная про
чнос
ть на разрыв, МПа
У
длинение при разрыве, %
Предел прочности на разрыв, Al
Удлинение, Al
0,0
0,5
1,0
1,5
2,0
2,5
3,0
3,5
300
250
200
150
100
50
0
45,0
37,5
30,0
22,5
15,0
7,5
0,0
Производство
ÎÁÌÎÒÎ×ÍÛÅ ÏÐÎÂÎÄÀ
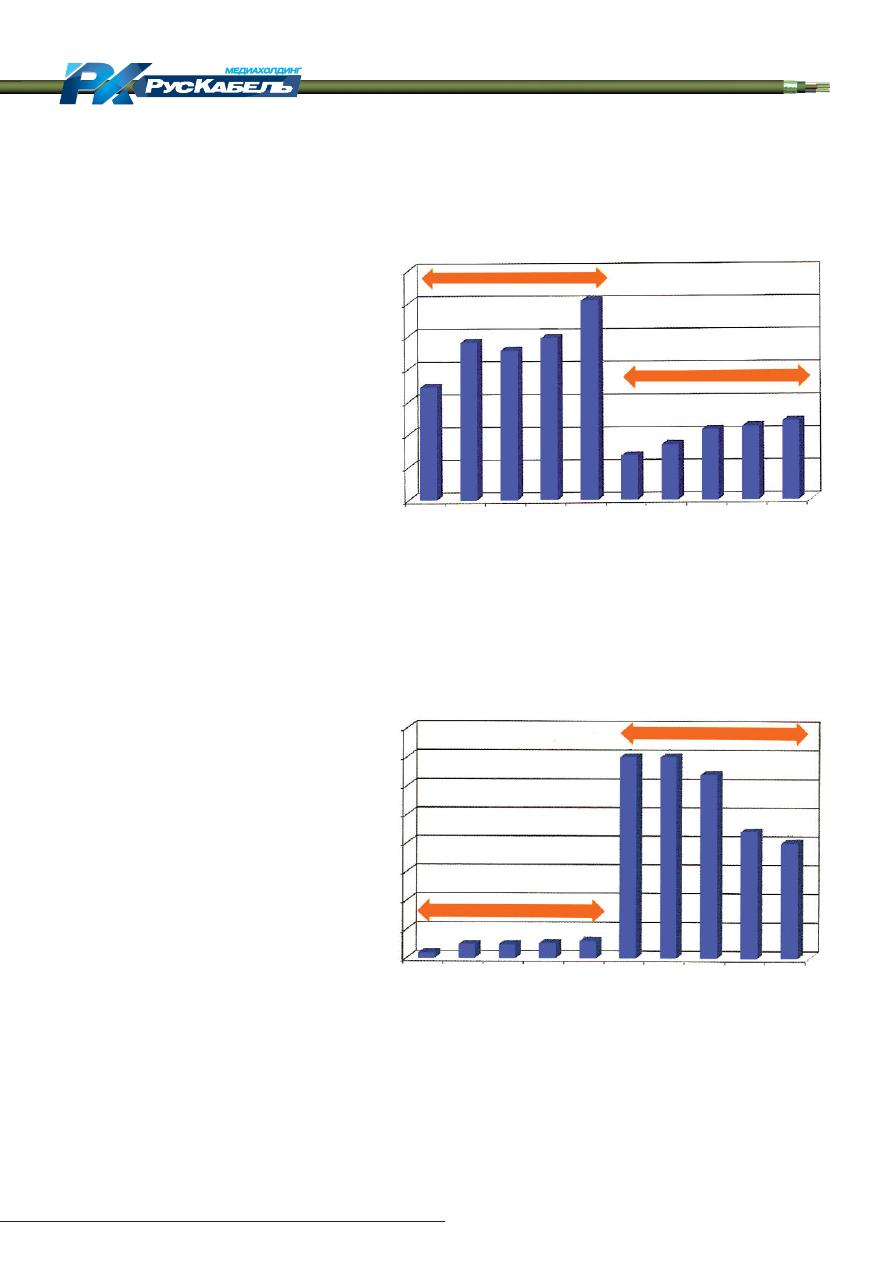
«КАБЕЛЬ-news», № 5, 2013, www.kabel-news.ru
29
но видеть, что начальная прочность
AlFe0,6Mg0,1 такая же, как у AlMg0,5,
хотя твёрдость после волочения с на-
клёпом выше. Начальное удлинение
у AlFe0,6Mg0,1 выше, чем у AlMg0,5
(класс термообработки F), что озна-
чает, что добавление магния можно
рассматривать как введение добавки,
которая увеличивает способность ма-
териала деформироваться.
Эффекты, подобные описанным
выше, могут наблюдаться в сплавах
AlFe0,5Cu0,2, также относящихся
к материалам, которые подверга-
ются отжигу в процессе нанесения
эмали на провода. Медь хорошо
растворяется в алюминии при высо-
ких температурах, но в сравнении с
магнием его растворимость при тем-
пературе окружающей среды пре-
небрежимо мала. Как следствие —
дисперсионное твердение мате-
риала может быть осуществлено в
фазе упрочнения Al
2
Cu. Медь обыч-
но оказывает небольшое влияние на
электропроводность материала. Уве-
личение удельного сопротивления,
рассчитанное по формуле, предло-
женной Нордхаймом, не превышает
0,8 нОм·м при наличии 0,2% меди
в твёрдом растворе. К сожалению,
медь, добавленная в алюминий, сни-
жает коррозионную стойкость, но
для эмалированных проводов с изо-
лированной от контакта с атмосфе-
рой металлической частью провода
этим эффектом можно пренебречь.
Связь между механическими свой-
ствами сплава AlFe0,5Cu0,2 и общим
натяжением во время волочения
(рис. 6) показывает, что этот матери-
ал по сравнению с алюминием имеет
высокую прочность и хорошую пла-
стичность.
ЗАКЛЮЧЕНИЕ
Алюминий с добавками Fe, Mg и
Cu может быть интересной альтерна-
тивой чистому алюминию для изго-
товления обмоточных проводов. Тех-
нические свойства рассмотренных в
настоящей работе сплавов гораздо лучше, чем у чи-
стого алюминия, и их применение может увеличить
эффективность технологического процесса изготов-
ления эмалированных проводов. Технологии изго-
товления эмалированного провода из Al, AlFe0,5 и
Рис. 7. Предельная прочность на разрыв материалов после
холодной прокатки и отжига — Al, сплавов AlFe0,5; AlFe1,1;
AlFe0,6Mg0,1 и AlFe0,5Cu0,2
Материал
Предельная про
чнос
ть на разрыв, МПа
300
250
200
150
100
50
0
172
240
228
247
304
67
84
107
112
120
Al
AlFe0,5
AlFe1,1
AlFe0,5Cu0,2
AlFe0,6Mg0,1
Al
AlFe0,5
AlFe1,1
AlFe0,5Cu0,2
AlFe0,6Mg0,1
Рис. 8. Удлинение материалов при разрыве после холодной
прокатки и отжига в испытании на растяжение для алюминия и
сплавов AlFe0,5; AlFe1,1; AlFe0,6Mg0,1 и AlFe0,5Cu0,2
Материал
У
длинение при разрыве, %
40
35
30
25
20
15
10
5
0
0,9
2,4
2,4
2,6
3,0
35
35
32
22
20
Al
AlFe0,5
AlFe1,1
AlFe0,5Cu0,2
AlFe0,6Mg0,1
Al
AlFe0,5
AlFe1,1
AlFe0,5Cu0,2
AlFe0,6Mg0,1
AlFe0,6Mg0,1 были в полном масштабе применены
на заводе TELE-fonika Kable Sp. z o.o. S.K.A. Сплав
AlFe0,5, по нашему мнению, можно считать опти-
мальным материалом для изготовления типовых
и тонких эмальпроводов, а сплав AlFe0,6Mg0,1 —
Производство
ÎÁÌÎÒÎ×ÍÛÅ ÏÐÎÂÎÄÀ
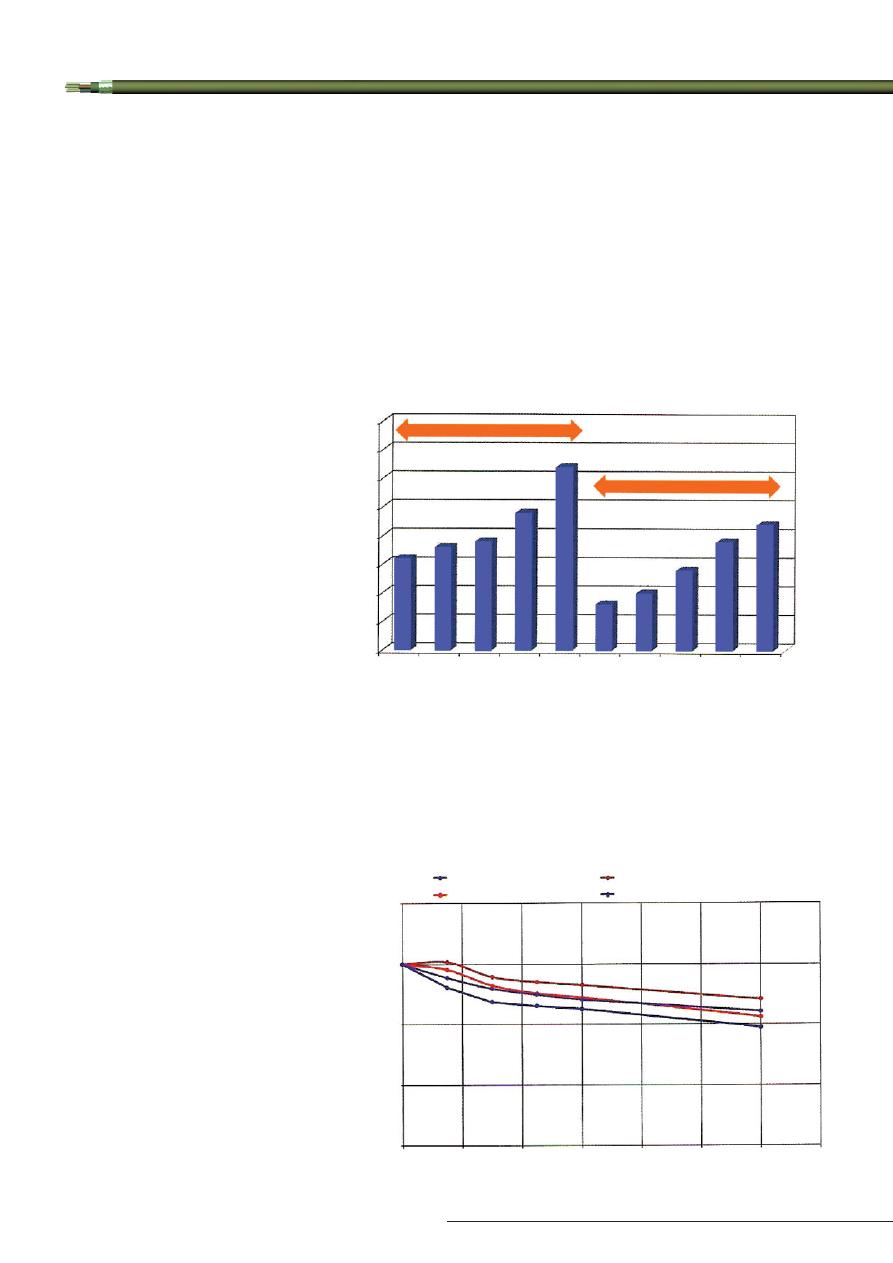
«КАБЕЛЬ-news», № 5, 2013, www.kabel-news.ru
30
для изготовления эмалированных проводов из спла-
вов.
На рис. 7—9 показаны рассчитанные механиче-
ские и электрические характеристики материалов,
проходивших испытания. На рис. 9 также дана элек-
тропроводность. На рис.10 представлены результа-
ты испытаний быстрым отжигом опытных образцов
проводов. Испытания проводов с
другими добавками к алюминию
должны быть продолжены.
ЛИТЕРАТУРА
1. Ch. Sullivan. Aluminum windings
and other strategies for high-fre-
quency magnetics design in an
era of high copper and energy
costs. IEEE Transactions On
Power Electronics, Vol. 23, № 4,
July 2008, pp. 2044—2051.
2. H. Kuroki. Fine rectangular mag-
net wires with ultra thin insulation
and its applications. Elec. Insu-
lation Conference and Electrical
Manufacturing & Coil Winding
Conference Proceedings, 1999,
p. 489—495.
3. Y. Tatematsu, M. Mesaki, A. Hi-
gashiura, F. Sano and T. Demo-
to. Development of selflubricat-
ing magnet wires for alternative
refrigerant. Electrical Electronics
Insulation Conference and Elec-
trical Manufacturing & Coil Wind-
ing Conference Proceedings,
1995, pp. 427—430.
4. K. Ueda. Progress of magnet
wire technology in Japan. IEEE
Electrical Ins. Mag., Vol. 5, № 3,
May/June 1989, pp. 18—26.
5. M. Winkeler. Magnet Wire Enam-
els: Which One? IEEE Electrical
Ins. Mag., Vol. 7, № 4, July/Au-
gust 1991, pp. 61—66.
6. L.J. Payette. The properties of a
universal magnet wire enamel.
IEEE Electrical Ins. Mag., Sept.
1986, pp. 40—43.
7. F.R. Bohm, K. Nagel and H.
Schindler. A new generation of
wire enamel for the production
of magnet wires with outstanding
corona resistance. Elec. Insula-
tion Conference and Electrical
Manufacturing & Coil Winding
Conference Proceedings, 2003,
pp. 109—113.
Рис. 9. Удельное сопротивление после холодной прокатки и
отжига в испытании на растяжение для алюминия и сплавов
AlFe0,5; AlFe1,1; AlFe0,6Mg0,1 и AlFe0,5Cu0,2
Материал
У
дельное э
лек
трическ
ое сопротивление, нОм
. м 30,5
30
29,5
29
28,5
28
27,5
27
26,5
28,1
28,3
28,9
28,4
27,3
27,5
27,9
28,4
28,7
29,7
Al
AlFe0,5
AlFe1,1
AlFe0,5Cu0,2
AlFe0,6Mg0,1
Al
AlFe0,5
AlFe1,1
AlFe0,5Cu0,2
AlFe0,6Mg0,1
Рис. 10. Изменение (в %) начальной предельной прочности на
разрыв после нагрева в течение различных периодов времени
для Al, AlFe0,5, AlFe0,6Mg0,1 и AlFe0,5Cu0,2; температура 200
о
С,
печь с масляной ванной
AlFe0,6Mg0,1
AlFe0,5Cu0,2
Время, с
Изменение на
чальной про
чнос
ти на
разрыв, %
Al
AlFe0,5
0
20
40
60
80
100
120
140
110
100
90
80
70
8. H. Pops. The conductor role in the manufac-
ture and performance of magnet wire. IEEE
Elec. Ins. Mag., Vol. 11, Sept./Oct. 1995,
pp. 17—23.
9. G.P. Brown, D.T. Haarr and A. Metlay. The use of
thermal analysis methods for the estimation of ther-
mal life ratings of magnet wire enamels. IEEE Tran.
Производство
ÎÁÌÎÒÎ×ÍÛÅ ÏÐÎÂÎÄÀ
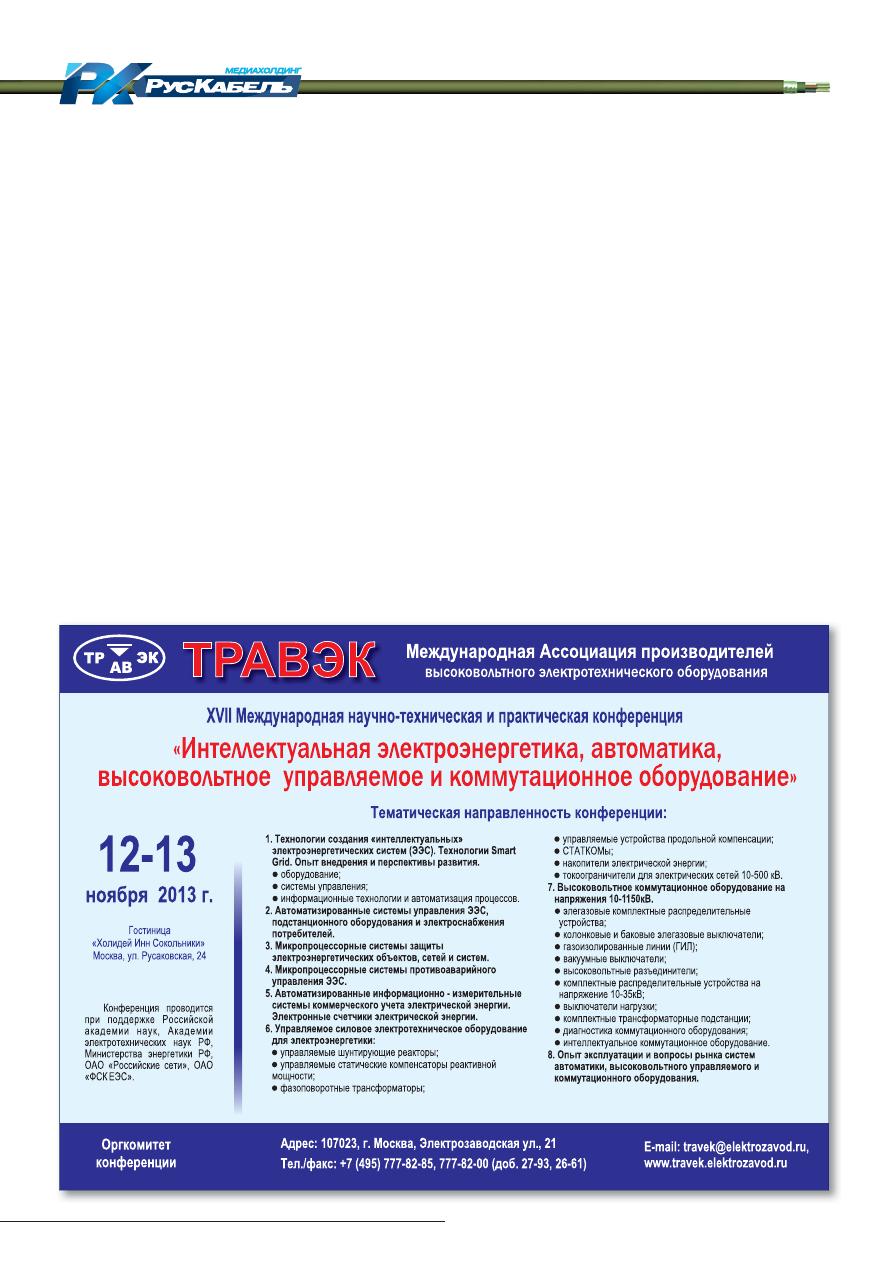
«КАБЕЛЬ-news», № 5, 2013, www.kabel-news.ru
31
On Electrical Insulation, Vol. EI-8, № 2, June 1973,
pp. 36—41.
10. EN 60317. Specs for winding wires.
11. IEC 60851. Winding wires, test methods.
12. D.J. Barta. Revisions of periodic conformance test
procedures in NEMA MW 1000 magnet wire standart.
Elec. Ins. Conf. Elec. Mfg. Expo Proc., 2005.
13. K. Kimura, S. Ushirone, T. Koyanagi and M. Hikita.
PDIV characteristics of twisted-pair of magnet wires
with repetitive impulse voltage. IEEE Trans. On Di-
electrics and Electrical Ins. Vol. 14, № 3, June 2007,
pp. 744—750.
14. J.F. Dexter. Thermal evaluation of enameled magnet
wire, power apparatus and systems. III. Trans. of the
American Institute of Electrical Eng., April 1956, pp.
40—44.
15. J.H. Thomas and J.F. Dexter. Effect of wire metal on
the thermal life of enameled magnet wire, power ap-
paratus and systems, part III, Trans. of the American
Institute of Electrical Eng., Dec. 1957, pp. 1009—
1013.
16. C. Araki and T. Taguchi. Thermal degradation of
polyesterimide magnet wire. Electrical Insulation and
Dielectric Phenomena Conference, 1993, pp. 526—
531.
17. ANSI/NEMA MW 1000-2008 magnet wire.
18. R. Iricibar, C. Pampillo and H. Chia. Metallurgical
aspects of al. alloys for electrical applications, alu-
minum transformation technology and applications.
ASM, 1978, pp. 241—303.
19. T. Knych. Power overhead conductors: theory, mate-
rials, applications. In Polish, 2010, wyd. AGH.
20. EN 515. Aluminum/aluminum alloys. Wrought prod-
ucts.
21. E.C. Perryman. Relationship between recovery and
recrystallization in super-purity aluminum. Journal of
Metals (Trans. AIME), Vol. 9, 1955, pp. 1053—1064.
Источник: A new generation
of aluminum enameled winding wires.
T. Knych, A. Mamala, M. Jablonski and P. Uliasz.
Wire Journal International. 1012, V.45,
№ 1, pp. 55—61.
Перевод Святослава ЮРЬЕВA
Производство
ÎÁÌÎÒÎ×ÍÛÅ ÏÐÎÂÎÄÀ
Оригинал статьи: Новое поколение эмалированных алюминиевых обмоточных проводов
Эмалированные провода уже давно используются для изготовления обмоток в электрических моторах, трансформаторах и катушках, но области их применения расширились с развитием электроники — драйверы жёстких дисков в компьютерах или наушники, также они активно используются в современных источниках питания — инверторы или коммутирующие элементы и источники электрического тока.