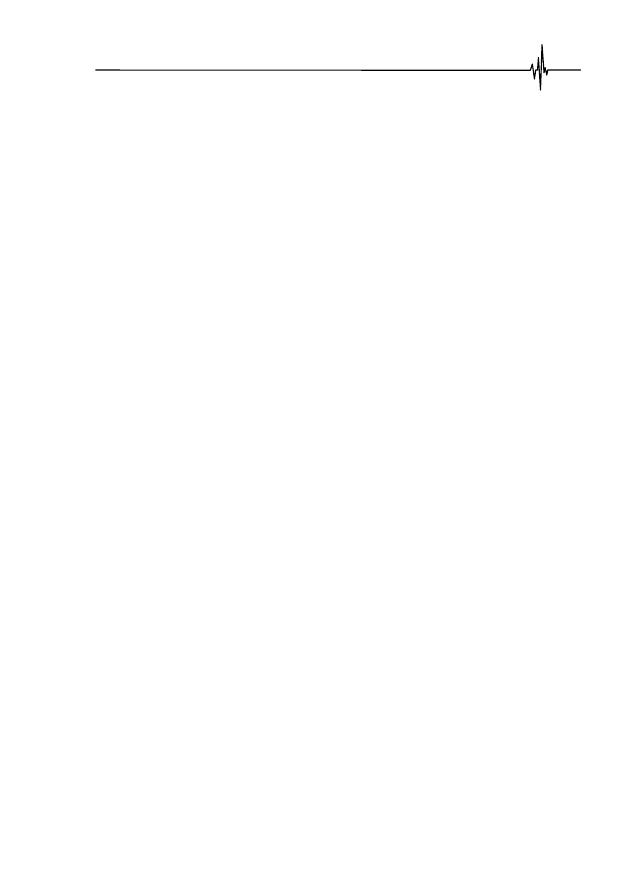
Глава 6. Оценка надежности и приоритетности ремонтов для электрооборудования
нефтяной промышленности с учетом возможного риска
147
Глава шестая
ОЦЕНКА НАДЕЖНОСТИ И ПРИОРИТЕТНОСТИ РЕМОНТОВ
ДЛЯ ЭЛЕКТРООБОРУДОВАНИЯ НЕФТЯНОЙ
ПРОМЫШЛЕННОСТИ С УЧЕТОМ ВОЗМОЖНОГО РИСКА
6.1. Корректная организация эксплуатации ПЭУ
Как отмечалось ранее, специфика нефтяной отрасли в значительной мере
связана с конкретными особенностями скважин, а именно: значительная
глубина, разнообразные рабочие среды (жидкости, газы, твердые примеси
и др.), физические условия по температуре и давлению, ограниченное рабо-
чее пространство, разнообразные технологические объекты, работающие
совместно в электротехнических комплексах (насосы и электродвигатели,
в частности ЭЦН и ПЭД, другие наземные и подземные элементы систем
электроснабжения (СЭС) и др.). Это в значительной мере определяет орга-
низацию современной эксплуатации ПЭУ наряду с общепринятыми положе-
ниями оптимального управления сложными электротехническими комплек-
сами (ЭТК) [71]. Ее важнейшим положением является обеспечение экономи-
чески оправданной надежности объектов ПН в соответствии с директивными
и перспективными рекомендациями [12]. Поэтому для решения задач управ-
ления в ЭТК нефтедобычи необходима прежде всего цифровизация [22]
объектов и технологических процессов ПЭУ.
Для ее реализации требуется формирование информационной базы (ИБ) –
конкретного цифрового множества разнообразных характеристик ПЭУ
в целом и его объектов. Состав и содержание ИБ определяются условиями
и требованиями комплекса решаемых задач и техническими возможностями
соответствующих служб ПН. С информационной точки зрения в названном
множестве содержатся паспортные данные, а также результаты, полученные
средствами спорадических измерений и диагностики технического состоя-
ния (ТС) ПЭУ в процессе эксплуатации, при техническом обслуживании
и ремонтах (ТОиР), с погрешностями, в общем случае известными тем
или иным образом. Также может быть использована информация из опросов
специалистов-экспертов [52]. В этом случае даже при высокой практической
достоверности оценка погрешности становится неопределенной.
Для снижения риска некорректного решения задач эксплуатации, свя-
занных с организацией ТОиР, к сведениям об отказах и простоях объектов,
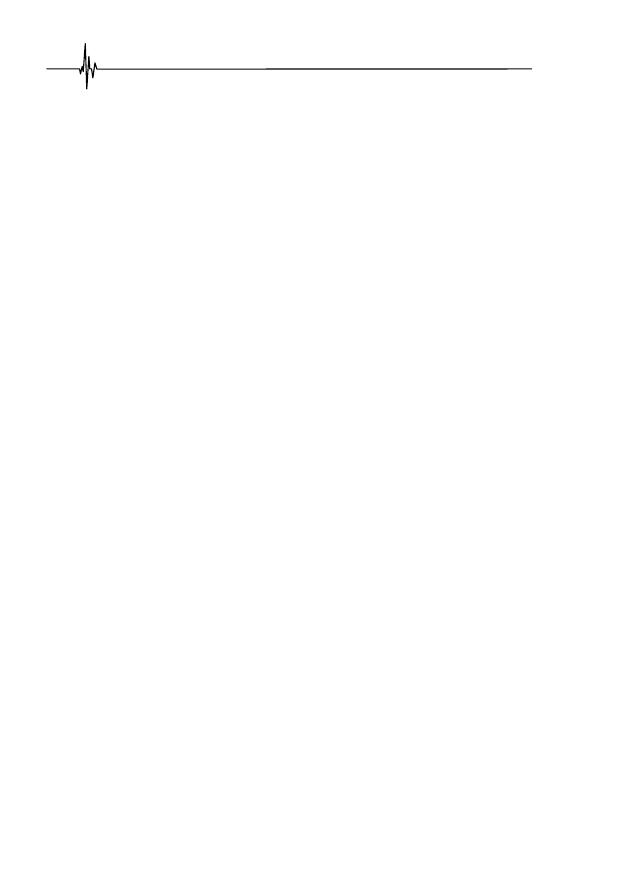
Повышение эффективности эксплуатации
погружных электроустановок нефтедобычи
148
как правило, добавляются сведения об испытаниях и оценке износа, сведения
о показателях ТС отдельных узлов ПЭУ [53]. Объем последних система-
тически возрастает в связи с ростом объема непрерывного и периодиче-
ского автоматизированного контроля их ТС стационарными и автоном-
ными диагностическими устройствами [11, 93]. В качестве примера мож-
но назвать комплекс устройств автоматизированного контроля ТС
и, в частности, температуры ПЭД.
Необходимость формирования актуальной и достоверной ИБ определя-
ется непрерывной выработкой ресурсов объектов ПЭУ в результате интен-
сивных (по внутренним запасам энергии) эксплуатационных физических
воздействий (ЭФВ) самого различного происхождения. Их объединяет то,
что, действуя совместно, они в конечном итоге приводят к полному износу
и последующему отказу конкретного объекта ПЭУ или их совокупности.
Формально отказ конкретного объекта ПЭУ имеет место, когда накопившиеся
негативные последствия различных ЭФВ в совокупности превысят внутрен-
ние возможности объекта противостоять непрерывному потоку данных воз-
действий. Их необходимо сравнивать в темпе технологических процессов
нефтедобычи, используя оценку работоспособности объекта по положитель-
ной величине его остаточного ресурса (ОР) как важнейшей эксплуатацион-
ной характеристики ПЭУ [81, 93].
Описанное увеличение количества способов сбора данных о тех-
ническом состоянии ПЭУ ПН в совокупности приводит к повышению на-
дежности единичных элементов комплекса ПЭУ. Поэтому данных по отка-
зам, особенно для наземной инфраструктуры и СЭС ПЭУ, информации
о проведении плановых и аварийных ремонтов становится все меньше.
В итоге возникают непреодолимые сложности в определении как единич-
ных, так и комплексных показателей надежности для групп однотипного
оборудования. В большинстве случаев расчет надежности сводится к опре-
делению показателей безотказности и ремонтопригодности [93]. Благодаря
внедряемым системам профилактических испытаний и непрерывной диагно-
стики ТС электрооборудования СЭС ПН стало возможным определение
количественных показателей долговечности и безотказности [94]. Более глу-
бокое изучение свойств надежности ПЭУ, а именно возможность количест-
венной оценки управляемости, безопасности, более того – оценка интеграль-
ных показателей надежности, находятся на начальном этапе обсуждения
и представляют неоспоримый научный и практический интерес.
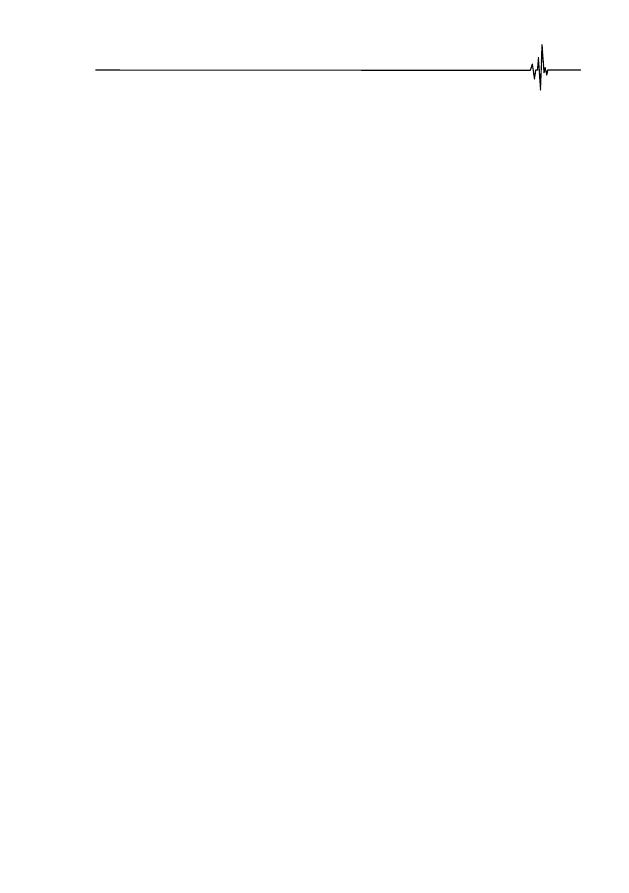
Глава 6. Оценка надежности и приоритетности ремонтов для электрооборудования
нефтяной промышленности с учетом возможного риска
149
6.2. Причинно-следственная оценка производственных рисков
эксплуатации парка ПЭУ
Помимо совершенствования подходов к реализации ремонтов на пред-
приятиях нефтяного кластера отдельный интерес представляет совершенство-
вание самого механизма проведения ремонта в пределах одной скважины.
Одно из перспективных направлений энергосбережения и повышения энерго-
эффективности работы ПН – это применение инструментов и технологий бе-
режливого производства (
lean production, lean manufacturing
) [94, 95].
Традиционно принято считать, что
lean
-менеджмент более применим
к отраслям с высокой добавленной стоимостью продукции, однако это всего
лишь стереотип. Установлено, что наиболее «узкое» место для ПН, связан-
ное с наибольшими рисками и затратами, – это выход из строя оборудова-
ния, технологические отказы. Именно поэтому вопрос оптимизации ремон-
тов оборудования на основе названной технологии является актуальным.
При детальном изучении процесса ремонта становится очевидно, что глав-
ный путь оптимизации заключается в снижении потерь, в данном случае это
длительное время выполнения ремонтов, прежде всего по смене УЭЦН.
При этом, как следствие, очевидно снижение объемов добычи нефти за от-
четный период.
Обработка результатов статистического анализа производственных
данных эксплуатации ПЭУ нефтедобычи говорит об острой необходимости
комплексной оценки их деятельности, в которой должны быть объединены
технические и экономические механизмы повышения эффективности экс-
плуатации. Теоретической основой технических методов повышения эффек-
тивности эксплуатации ПЭУ являются статистический анализ, математиче-
ское моделирование и исследования структурно-функциональных свойств
конструкций ПЭУ и конкретно ПЭД [82], которые подробно рассмотрены
в предыдущих главах. Можно констатировать, что значительные возможно-
сти для повышения эффективности эксплуатации технической системы
(ПЭУ и ПЭД) имеет подход, опирающийся на применение инженерных
методик и инструментов системы менеджмента качества, таких как диаграмма
К. Исикавы [41], известная также как диаграмма «рыбьей кости» (Fishbone
Diagram) или «причинно-следственная» диаграмма (Cause and Effect Diagram),
представленная на рис. 2.2; метод анализа видов и последствий потенциальных
отказов, или FMEA-анализ [94] (Failure Mode and Effects Analysis); диаграмма
В. Парето [95].
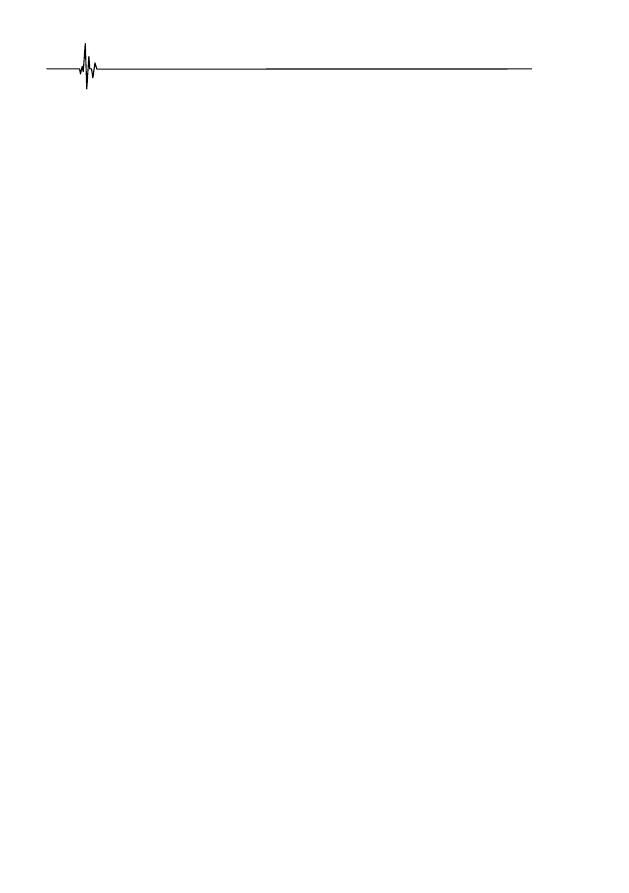
Повышение эффективности эксплуатации
погружных электроустановок нефтедобычи
150
Для повышения качества функционирования и эксплуатационной
эффективности ПЭУ и ПЭД разработана и описана методика, включающая
в себя перечисленные инженерные инструменты системы менеджмента
качества [92–95].
На первом этапе для конкретного технического объекта (в данном слу-
чае это ПЭУ) и (или) производственного процесса с его конкретной функци-
ей на основании опыта эксплуатации, предаварийной истории и технологи-
ческих нарушений, с использованием статистического материала по отказам
ПЭУ и ПЭД во 2-й главе представлена (см. рис. 2.2) диаграмма причинно-
следственной связи (диаграмма К. Исикавы) для оценки составляющих
эффективности эксплуатации ПЭУ и ПЭД. На данной диаграмме в графиче-
ской форме устанавливается причинно-следственная связь между всевозмож-
ными отказами (дефектами, приведшими к отказам) в работе погружного обо-
рудования и эффективностью эксплуатации комплекса. Краткое содержание
условного разделения причин отказов на электрические и технологические
(нет подачи) представлено ниже.
1.
Электрические причины
отказов элементов ПЭУ, как правило, связа-
ны с нарушением целостности цепи, электромагнитной совместимости либо
с низким качеством сборки и монтажа основных электромеханических
и электромагнитных устройств в составе ПЭУ [35]. Это возможно при сле-
дующих нарушениях:
а) снижение изоляции между жилами и землей:
– при пробое обмотки статора, который является следствием старения изо-
ляции ПЭД, заводского брака изготовления самого ПЭД, перегрева двигателя
(как правило, возникает по причине малого притока, срыва подачи, негерметич-
ности НКТ, высокой температуры перекачиваемой жидкости и т. д.), повышен-
ной вибрации, являющейся одним из немаловажных факторов отказа, в резуль-
тате которого происходят пропуски пластовой жидкости через торцевое уплот-
нение с последующим пробоем изоляции самого двигателя [36];
– при перегреве, течи и плавлении удлинителя, возникающих из-за нека-
чественной эксплуатации УЭЦН (частые отключения защиты от турбинного
вращения, некачественный подбор УЭЦН (недостаточный приток),
частые отключения защиты от срыва подачи (ЗСП) (в насосе газ, отсутствие
подачи), частые отключения защиты от перегруза (ЗП) (повышенное содер-
жание КВЧ (количество взвешенных частиц), интенсивные солеотложения,
подклинивания вследствие износа рабочих органов, некачественное электро-
снабжение) [37], некачественный вывод в ремонт УЭЦН (несоблюдение
регламента по выводу УЭЦН, брак подбора УЭЦН);
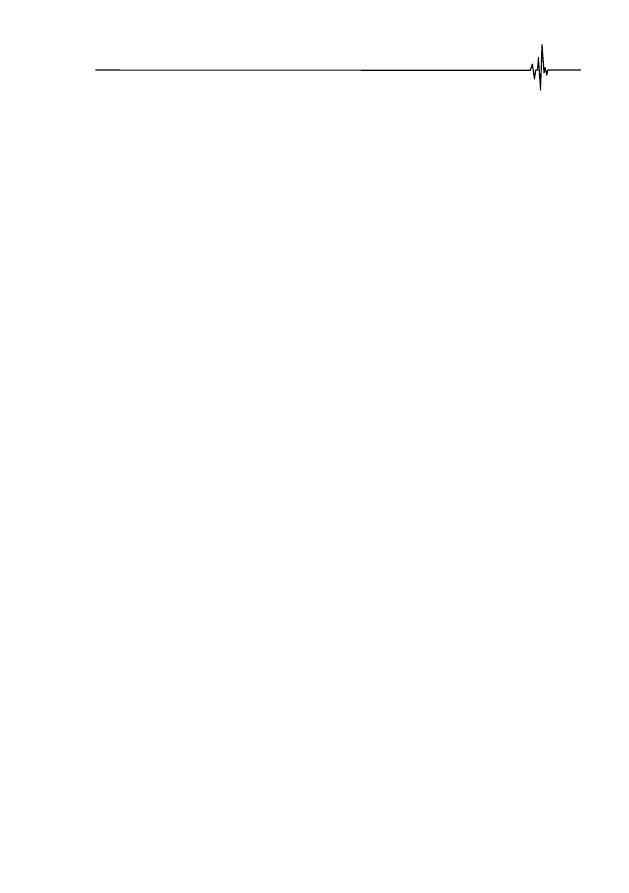
Глава 6. Оценка надежности и приоритетности ремонтов для электрооборудования
нефтяной промышленности с учетом возможного риска
151
– при повреждении изоляции при СПО (спускоподъемных операциях),
что обусловлено нарушением скорости спуска, наличием посторонних пред-
метов и перекрутом удлинителя кабеля;
б) К.З. обмотки ПЭД. Исключение возникновения подобного отказа
во многом обеспечивается герметичностью торцевых уплотнений, герметич-
ностью токоввода, применением качественного масла, отсутствием попада-
ния атмосферных осадков в ПЭД при монтаже [38];
в) отсутствие «звезды» (нарушение целостности цепи). Это один из са-
мых сложных комплексных параметров эксплуатационной эффективности
ПЭУ, основными вызывающими факторами которого являются: некачест-
венный ремонт ПЭД, повреждение сростка кабеля при СПО, некачественный
монтаж (кабель – ПЭД), замыкание датчика на УЭЦН [39].
2.
Технологические причины
отказов (нет подачи), как правило, связаны
с нарушениями условий функционирования составных элементов УЭЦН
вследствие ухудшения или изменения условий эксплуатации, низкого каче-
ства оборудования и его монтажа [40]. Наиболее частыми отказами по тех-
нологическим причинам являются следующие:
а) в результате возникновения сопротивления вращению вала УЭЦН
происходит его закручивание или слом. Главными определяющими факто-
рами данного отказа являются некачественная сборка насоса, кривизна
в зоне подвески УЭЦН [41], солеотложения, механические примеси;
б) полет (расчленение узла). При рассмотрении отказов в механической
части ПЭУ расчленение узла разделяют на расчленение по НКТ и расчлене-
ние по ЭЦН; в первом случает отказ возникает по причинам старения НКТ,
некачественной затяжки НКТ, неудовлетворительного качества резьбы, вибра-
ции [72]; во втором случае – из-за брака сборки ЭЦН, старения оборудования,
некачественной затяжки резьбовых соединений, динамических ударов [43];
в) заклинивание насоса – является частным случаем технологического
отказа и возникает из-за брака изготовления самого УЭЦН [64].
После проведенного анализа и установления причинно-следственной
связи между отказом в работе ПЭУ, ПЭД и основными дефектами, приводя-
щими к отказу, предлагается проводить мониторинг, посредством которого
выявляются все недостатки эксплуатации оборудования скважины, их при-
чины и разрабатываются процедуры в виде корректирующих действий с це-
лью повышения надежности всей системы в целом. Содержание предложен-
ной схемы мониторинга представлено на рис. 6.1.
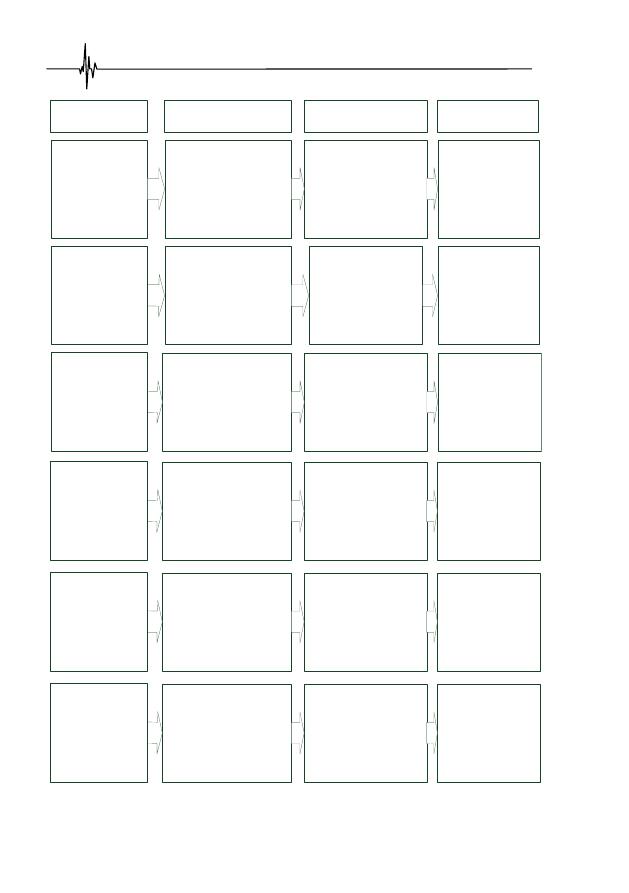
Повышение эффективности эксплуатации
погружных электроустановок нефтедобычи
152
Слом вала (шлицевой
муфты
1. Скрытые дефекты
2. Механические повреждения при
монтаже
3. Износ в результате выноса
проппанта после ГРП
4. Высокое содержания КВЧ
5. Коррозия в связи с длительной
эксплуатацией
6. Нарушение технологии
проведения СПО
7. Усталостное разрушение металла
1. Комплектация узлов и
деталей ЭЦН согласно
утвержденной технической
документации
2. Недопущение
длительного воздействия
критических нагрузок на
УЭЦН при эксплуатации и
работах по расклиниванию
1. Значительное снижение токовых
нагрузок и загрузки ПЭД
относительно нормальных рабочих
значений
2. Отсутствии или снижении
производительности УЭЦН
3. Недобор нефти, убытки
компании
1. Заводской брак
2. Скрытый дефект вала
3. Брак комплектации
4. Несоответствие максимально
передаваемой мощности вала
мощности ПЭД
5. Слом вала при расклинивании
УЭЦН (превышение допустимых
нагрузок на вал)
6. Выработка ресурса вала ввиду
длительной эксплуатации
1. Использование
качественных деталей при
изготовлении / ремонте
2. Проведение входного
контроля
3. Действия персонала при
подтверждении отказа в
соответствии с требованиями
ЛНД
4. Применение различных
методов борьбы с коррозией.
1. Полет на забой скважины,
останов оборудования
2. Недобор нефти, убытки
компании
3. Несоблюдение сроков
проведения ТОиР, непредвиденные
расходы
1. Засорение рабочих органов ЭЦН
2. Нарушение технологии
эксплуатации УЭЦН
3. Некачественное освоение
скважины
4. Работа УЭЦН в зоне
недопустимого значения кривизны
ствола скважины
5. Повышенный уровень вибрации
УЭЦН
1. Заклинивание и выход из
строя оборудования скважины,
останов скважины
2. Недобор нефти, убытки
компании
1. Соблюдение технологии
проведения ГРП и освоения
скважины после ГРП
2. Недопущение создания
высоких депрессий на ПЗП
3. Проведение промывки
рабочих органов УЭЦН
4. Профилактика и
предупреждение
солеотложений
Действия
Последствя
Причины
Характер отклонений
Клин
Полет (расчленение узла)
1. Пробой изоляции
2. Брак изготовления
3. Механическое повреждение кабеля
нарушение изоляции
(токопроводящей жилы).
4. Нарушение технологии
проведения (СПО)
5. Негерметичность системы
1. Недопущение теплового
воздействия и нагрузок на
электрочасть выше
допустимых
2. Проведение входного
контроля
3. Проведение стендовых
испытаний в полном объёме
и в соответствии с
требованиями директивных
документов
1. Авария по причине КЗ
2. Аварийный останов скважины,
недобор нефти, убытки компании
3. Несоблюдение сроков
проведения ТОиР, непредвиденные
расходы
Отсутствие «звезды»
1. Пробой изоляции
2. Брак изготовления
3. Брак монтажа
4. Низкое качество масла
5. Негерметичность системы
6. Превышение нагрузок сверх
допустимых
7. Заклинивание оборудования
механической части ЭПУ
1. Недопущение теплового
воздействия и нагрузок на
электрочасть выше
допустимых
2. Проведение входного
контроля
3. Проведение стендовых
испытаний в полном объёме
и в соответствии с
требованиями директивных
документов
1. Аварийный останов ПЭД,
возможен пожар
2. Аварийный останов скважины,
недобор нефти, убытки компании
3. Несоблюдение сроков
проведения ТОиР, непредвиденные
расходы
К.З. обмотки ПЭД
1. Пробой изоляции кабеля
2. Брак изготовления
3. Брак монтажа
4. Скрытый заводской дефект кабеля
нарушение технологии ремонта
кабеля
5. Нарушение технологии
проведения (СПО)
6. Повреждение кабельной линии при
изготовлении, транспортировке или
монтаже
1. Недопущение нагрузок
выше допустимых
2. Проведение входного
контроля
3. Проведение стендовых
испытаний в полном объёме
4. Проведение всех операций
с кабельной линией в
соответствии с требованиями
действующей НТД и ЛНД
1. Аварийный останов ПЭД,
возможен пожар
2. Аварийный останов скважины,
недобор нефти, убытки компании
3. Несоблюдение сроков
проведения ТОиР, вывод в ремонт
оборудования скважины,
непредвиденные расходы
Снижение изоляции
между жилами и
землей
Рис. 6.1.
Схема мониторинга причин и следствий,
связанных с технологическим отказом в работе ПЭУ
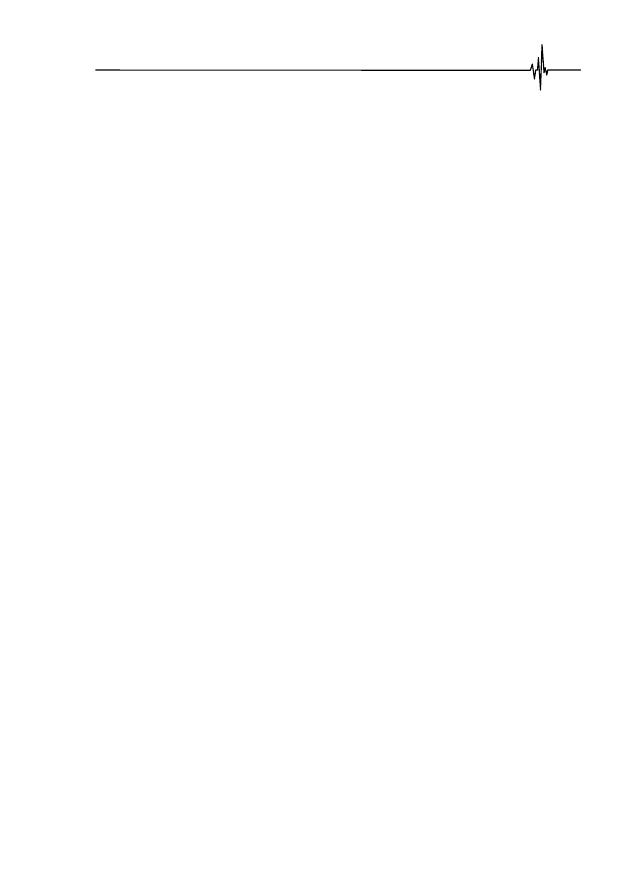
Глава 6. Оценка надежности и приоритетности ремонтов для электрооборудования
нефтяной промышленности с учетом возможного риска
153
Приведенная схема мониторинга устанавливает взаимосвязь между явле-
ниями возникновения отказов в работе ПЭУ, причинами их возникновения,
последствиями и предложенными действиями по их исключению в процессе
дальнейшей эксплуатации. На данной схеме описаны основные составляющие
диаграммы К. Исикавы, а именно: для электрической причины возникновения
отказа элементов ПЭУ – снижение изоляции между жилами и землей, К.З.
обмотки ПЭД, отсутствие «звезды» (нарушение целостности цепи); для техно-
логической причины отказа (нет подачи) – полет (расчленение узла), слом вала,
клин. Остальные виды технологических нарушений являются более частными
случаями либо следствием рассмотренных отказов и устраняется по разработан-
ным алгоритмам. Выполненная схема мониторинга с подробным описанием
причинно-следственной связи процесса возникновения технологических нару-
шений ПЭУ и ПЭД послужит базой для выполнения дальнейшего исследования
по методу FMEA-анализа.
6.3. Методология использования FMEA-анализа для оценки
вероятности возникновения производственных рисков
отказов парка ПЭУ
Метод анализа видов и последствий потенциальных отказов, или FMEA,
является эффективным механизмом обеспечения качества действующих
и разрабатываемых сложных технических систем, применяемым для обна-
ружения и устранения технологических нарушений и сопряженных с ними
дефектов либо снижения негативных последствий от них. Реализация воз-
можна за счет разработки комплекса мероприятий по прогнозированию
дефектов (отказов) и их анализу на различных жизненных циклах системы
(объекта) или отдельно взятого элемента [95].
Метод FMEA позволяет произвести анализ технологических нарушений
на ПН, спрогнозировать потенциально возможные отказы (дефекты), уста-
новить причины и последствия их возникновения, произвести оценку возни-
кающих рисков, в частности по выявлению или невыявлению дефектов
(скрытые дефекты), и предпринять меры для их устранения, уменьшения
вероятности возникновения, профилактики и снижения ущерба от их появ-
ления. На сегодняшний день данный метод представляет собой безотказную
методику по повышению эффективности эксплуатации, прошедшую апроба-
цию на промышленных предприятиях автомобилестроения в течение десят-
ков лет и доказавшую свою эффективность.
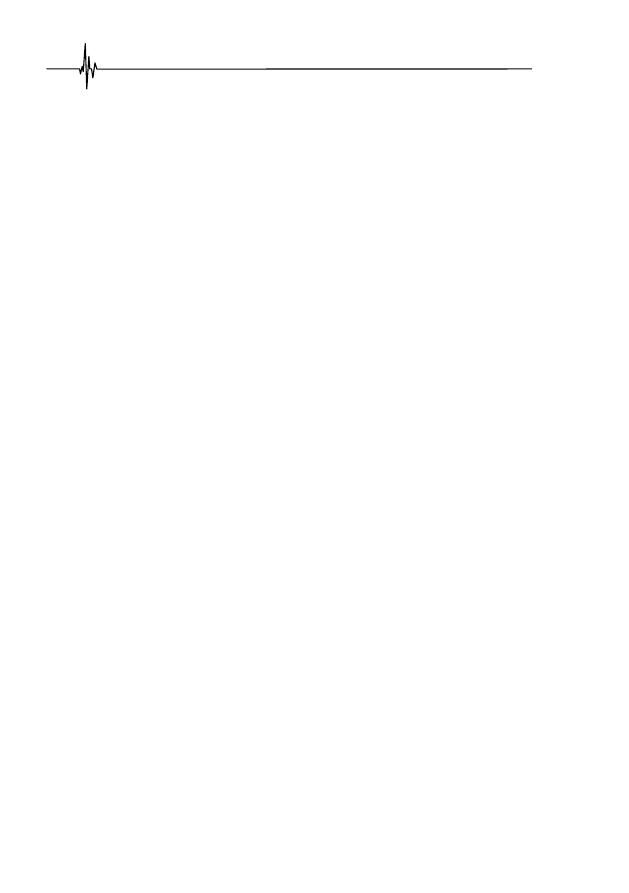
Повышение эффективности эксплуатации
погружных электроустановок нефтедобычи
154
Для полного понимания процессов выполнения FMEA-анализа
и терминологии, используемой в данной работе, необходимо определить
основные термины и сокращения.
Дефект
– невыполнение требования, связанного с предполагаемым или
установленным использованием. Определение установлено ГОСТ Р
51901.12-2007 (МЭК 60812:2006). Менеджмент риска. Метод анализа видов
и последствий отказов [97].
Отказ
– отклонение от нормального функционирования технической
системы (элемента системы), приводящее к сбоям в эксплуатации либо пол-
ной потере работоспособности.
Значимость
потенциального
дефекта
– параметр, характеризующий
вероятный ущерб от возникновения рассматриваемого дефекта, выраженный
в количественном эквиваленте.
Балл
значимости
(
S
) – оценка значимости потенциального дефекта,
определенная экспертно в зависимости от тяжести последствий от его воз-
никновения [97].
Вероятность
возникновения
дефекта
– параметр, характеризующий
количественную оценку состояния технической системы (элемента системы)
с дефектом данного вида.
Балл
возникновения
(
О
) – оценка, определяемая экспертно в зависимости
от вероятности возникновения рассматриваемого дефекта [97].
Вероятность
обнаружения
дефекта
– параметр, характеризующий
количественную оценку состояния технической системы (элемента системы)
с потенциальным дефектом данного типа, для которой существующие сис-
темы диагностики позволят обнаружить данный дефект или причину, его
вызвавшую.
Балл
обнаружения
(
D
) – оценка, определяемая экспертно и определяющая
вероятность обнаружения дефекта [97].
Комплексный
риск дефекта
– величина, характеризующая комплексную
оценку потенциального дефекта с позиций его значимости, вероятности воз-
никновения и обнаружения.
Приоритетное число риска
(
ПЧР
) – выражение величины комплексно-
го риска дефекта в количественной форме, равное произведению трех вели-
чин: балла значимости, балла возникновения и балла обнаружения примени-
тельно для рассматриваемого дефекта [97].
В рамках данной работы метод FMEA-анализа стратегически направлен
на решение следующих задач:
1. Формирование перечня всех возможных дефектов с выборкой по от-
казам, имеющим наибольшую плотность возникновения и наивысший класс
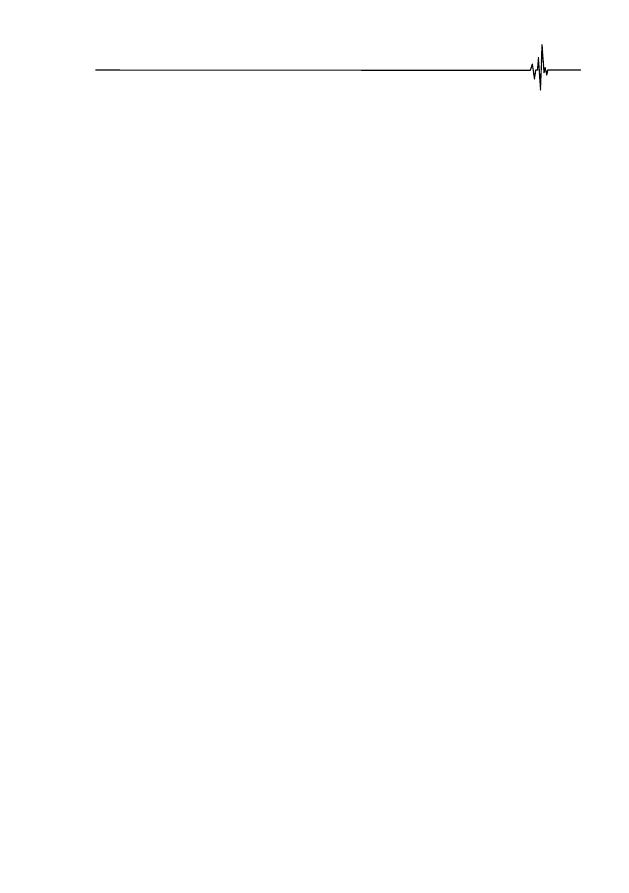
Глава 6. Оценка надежности и приоритетности ремонтов для электрооборудования
нефтяной промышленности с учетом возможного риска
155
опасности для оборудования, на основании данных статистики
о технологических нарушениях на ПЭУ ПН. При этом учитывается опыт
изготовления (заводские дефекты) и испытаний оборудования, а также опыт
реальных действий и вероятных ошибок эксплуатирующего персонала
в процессе производства, эксплуатации, ТОиР.
2. Определение в зависимости от вида предполагаемого отказа (дефек-
та) возможных отрицательных вариантов его возникновения и анализ тяже-
сти сопутствующих последствий с дальнейшей количественной и качествен-
ной оценкой их значимости.
3. Определение с оценкой частоты причины возникновения для каждого
возможного дефекта на основании свойств и особенностей конструкции,
технологического процесса, условий эксплуатации, ТОиР и т. д.
4. Определение на основе анализа технологического процесса коррект-
ности и достаточности предлагаемых и принятых мер по предупреждению
дефектов в эксплуатации, их обнаружению и устранению во время проведе-
ния ТОиР с количественной оценкой возможности исключения возникнове-
ния дефектов путем фиксации причин их происхождения на этапах эксплуа-
тации и изготовления элементов ПЭУ.
5. Оценка в виде численных значений обобщенного балла критичности ка-
ждого отказа, дефекта (с его причиной) по так называемому приоритетному
числу риска (ПЧР). При высоких значениях ПЧР следует произвести усовер-
шенствование технологического процесса или оборудования, а также выполнить
доработку системы мониторинга и диагностики, проведения ТОиР, пересмот-
реть требования правил эксплуатации с целью снижения данного показателя.
Проведение FMEA-анализа – достаточно сложная процедура, в основе
которой лежит работа группы экспертов по техническим направлениям изго-
товления, эксплуатации и испытания погружного оборудования скважины.
На рис. 6.2 представлен алгоритм применения метода FMEA-анализа
для оценки производственных рисков в эксплуатации парка ПЭУ ПН.
В соответствии с представленным алгоритмом процесс FMEA-анализа ус-
ловно разделяют на этапы. На первом этапе выполнена выборка дефектов,
имеющих наибольшую частоту возникновения, и сформирована диаграмма
К. Исикава, предложена схема мониторинга причин и следствий, связанных
с технологическим отказом в работе ПЭУ. На следующем этапе выполняется
оценка комплексного риска дефекта по критериям, установленным ГОСТ Р
51901.12-2007 (МЭК 60812:2006). Менеджмент риска. Метод анализа видов
и последствий отказов [97].
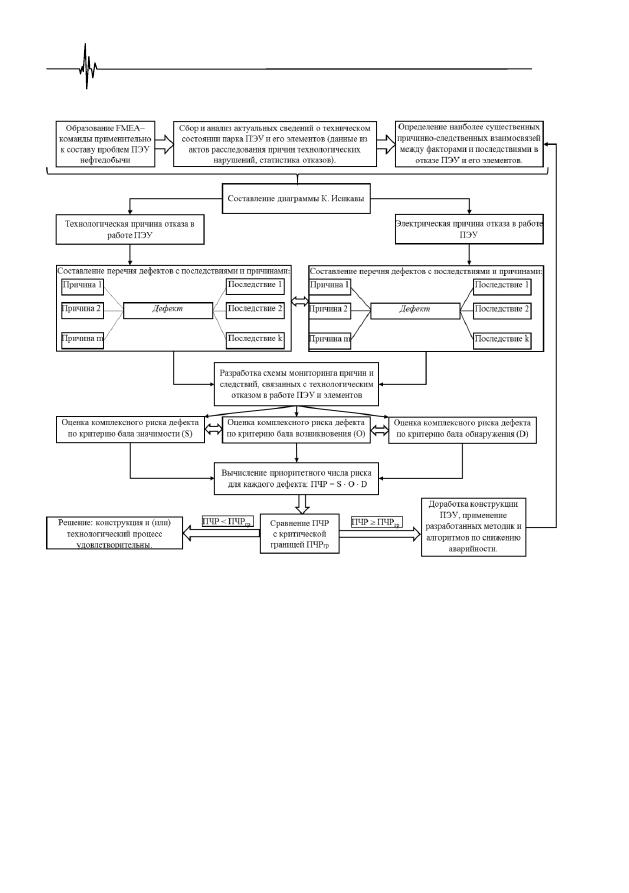
Повышение эффективности эксплуатации
погружных электроустановок нефтедобычи
156
Рис. 6.2.
Алгоритм применения метода FMEA-анализа
для оценки производственных рисков в эксплуатации парка ПЭУ
Для каждого рассмотренного дефекта следует определить его балл зна-
чимости
S
[97] по типовым таблицам баллов (табл. 6.1, 6.2) значимости
для предприятий нефтяной отрасли [95].
При последующем исследовании по методу FMEA-анализа необходимо
установить балл возникновения дефекта, для которого используется в соот-
ветствии с [97] обозначение
О
(типовые таблицы баллов возникновения
для ПН – табл. 6.3, 6.4). Для конкретного технологического процесса опре-
деляется частота причины возникновения рассматриваемого дефекта. Вели-
чина
O
измеряется в баллах и изменяется от 1 до 10 в зависимости от частоты
возникновения дефекта.
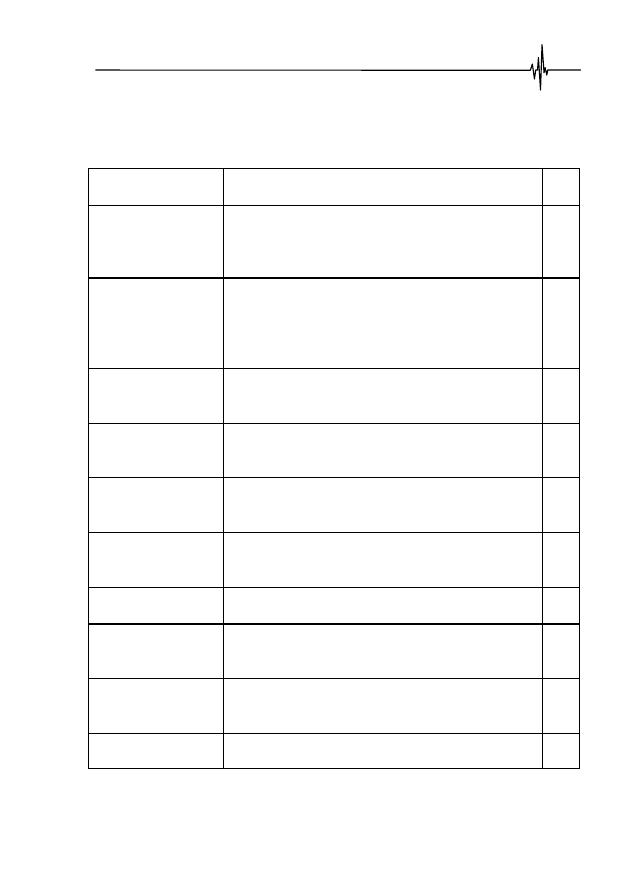
Глава 6. Оценка надежности и приоритетности ремонтов для электрооборудования
нефтяной промышленности с учетом возможного риска
157
Таблица 6.1
Шкала баллов значимости
S
для FMEA-конструкции
применительно к ПЭУ
Последствие
Критерий значимости последствия
Балл
S
Опасное
без предупреждения
Очень высокий ранг значимости, когда вид потенци-
ального дефекта ухудшает безопасность работы
ПЭУ, вызывает несоответствие обязательным требо-
ваниям безопасности и экологии без предупреждения
10
Опасное
с предупреждением
Весьма высокий ранг значимости, когда вид потен-
циального дефекта ухудшает безопасность работы
ПЭУ или вызывает несоответствие обязательным
требованиям безопасности и экологии с предупреж-
дением (пример для ПЭУ: К.З. обмотки ПЭД)
9
Очень важное
ПЭУ / элементы ПЭУ неработоспособны с потерей
основных функций (пример для ПЭУ: снижение
изоляции между жилами и землей)
8
Важное
ПЭУ / элементы ПЭУ работоспособны, но снижен
уровень эффективности (пример для ПЭУ: клин,
слом вала (шлицевой муфты))
7
Умеренное
ПЭУ / элементы ПЭУ работоспособны, но нарушена
функциональная связь со смежными элементами
(пример для ПЭУ: отсутствие «звезды»)
6
Слабое
ПЭУ / элементы ПЭУ работоспособно, но вспомога-
тельные системы работают малоэффективно (пример
для ПЭУ: полет (расчленение узла))
5
Очень слабое
Отклонение параметров добычи от нормы незначи-
тельно
4
Незначительное
Отклонение параметров добычи от нормы едва уло-
вимо, дефект может обнаружить оператор со средней
квалификацией
3
Очень
незначительное
Отклонение параметров добычи от нормы едва уло-
вимо, дефект может обнаружить оператор с высокой
квалификацией
2
Отсутствует
Нет последствия
1
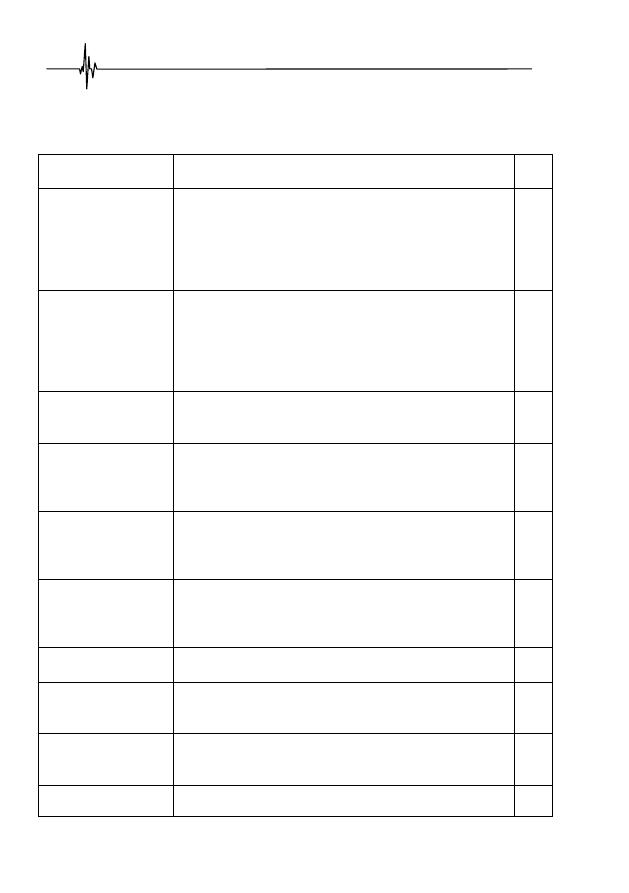
Повышение эффективности эксплуатации
погружных электроустановок нефтедобычи
158
Таблица 6.2
Шкала баллов значимости
S
для FMEA производственного процесса
применительно к ПЭУ
Последствие
Критерий значимости последствия
Балл
S
Опасное
без предупреждения
Аварийный останов процесса добычи, возможно возго-
рание, существует опасность для персонала. Очень высо-
кий ранг значимости, когда вид потенциального дефекта
ухудшает безопасность работы ПЭУ и (или) вызывает
несоответствие обязательным требованиям безопасности
и экологии без предупреждения
10
Опасное
с предупреждением
Аварийный останов процесса добычи, возможно возго-
рание, существует опасность для персонала. Очень высо-
кий ранг значимости, когда вид потенциального дефекта
ухудшает безопасность работы ПЭУ и (или) вызывает
несоответствие обязательным требованиям безопасности
и экологии с предупреждением
9
Очень важное
Большое нарушение производственного процесса.
Может отсутствовать подача. ПЭУ / узел ПЭУ неработо-
способны с потерей главной функции
8
Важное
Небольшое нарушение производственного процесса.
Может потребоваться работа выездной бригады, измере-
ния испытания оборудования. ПЭУ работоспособно, но
с пониженной эффективностью
7
Умеренное
Небольшое нарушение производственного процесса.
Снижение дебита сырья. ПЭУ / элемент ПЭУ работоспо-
собны, но нарушена функциональная связь со смежными
элементами
6
Слабое
Небольшое нарушение производственного процесса.
ПЭУ / элемент ПЭУ работоспособно, но некоторые
вспомогательные системы работают с пониженной
эффективностью
5
Очень слабое
Небольшое нарушение производственного процесса.
Отклонение параметров добычи от нормы незначительно
4
Незначительное
Небольшое нарушение производственного процесса. Может
потребоваться осмотр отдельного участка. Дефект может
обнаружить персонал со средней квалификацией
3
Очень
незначительное
Небольшое нарушение производственного процесса.
Дефект может обнаружить персонал с высокой квалифи-
кацией
2
Отсутствует
Нет последствия
1
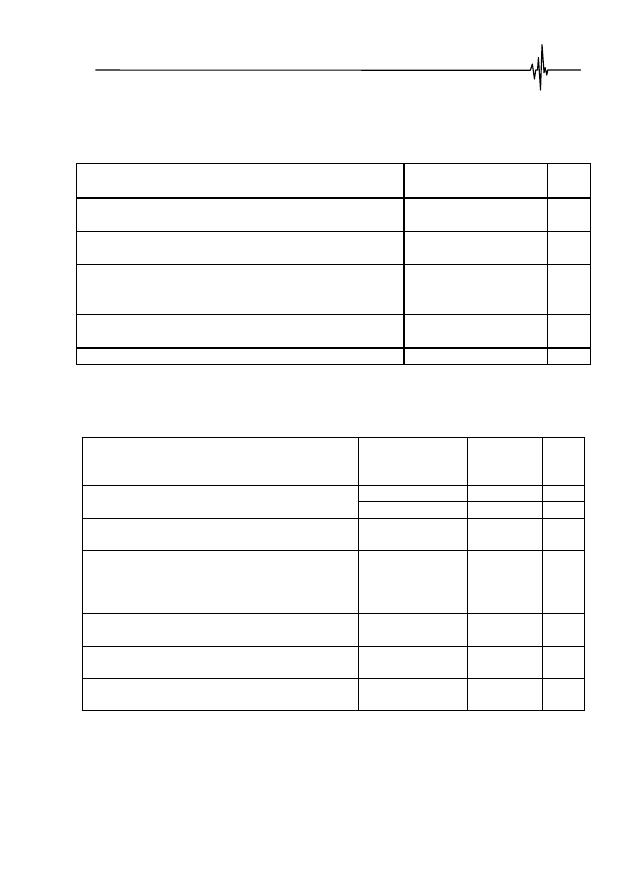
Глава 6. Оценка надежности и приоритетности ремонтов для электрооборудования
нефтяной промышленности с учетом возможного риска
159
Таблица 6.3
Шкала для выставления балла возникновения
О
для FMEA-конструкции применительно к ПЭУ
Вероятность отказа
Возможные частоты
отказа
Балл
О
Очень высокая: отказ почти неизбежен (снижение
изоляции между жилами и землей)
Более 1 из 2
10
>> 1 из 3
9
Высокая: повторяющиеся отказы (К.З. обмотки ПЭД)
Более 1 из 8
8
˃˃ 1 из 20
7
Умеренная: случайные отказы (расчленение узла,
клин, слом вала, отсутствие «звезды»)
Более 1 из 80
6
˃˃ 1 из 400
5
˃˃ 1 из 2000
4
Низкая: относительно мало отказов
Более 1 из 15000
3
˃˃ 1 из 150000
2
Малая: отказ маловероятен
Менее 1 из 1 500 000
1
Таблица 6.4
Шкала баллов возникновения
О
для FMEA-конструкции
применительно к ПЭУ
Вероятность дефекта
Возможные
частоты
дефекта
Индекс
pk
C
Балл
О
Очень высокая: дефект почти неизбежен
Более 1 из 2
Менее 0,33
10
˃˃ 1 из 3
˃˃ 0,33
9
Высокая: ассоциируется с аналогичными
процессами, которые часто отказывают
Более 1 из 8
˃˃ 1 из 20
Менее 0,51
˃˃ 0,67
8
7
Умеренная: в общем ассоциируется
с предыдущими процессами, у которых
наблюдались случайные дефекты,
но не в большой пропорции
Более 1 из 80
˃˃ 1 из 400
˃˃ 1 из 2000
Менее 0,83
˃˃ 1,00
˃˃ 1,17
6
5
4
Низкая: отдельные дефекты, связанные
с подобными процессами
Более 1
из 15000
Менее 1,33
3
Очень низкая: отдельные дефекты,
связанные с почти идентичными процессами
Более 1
из 150000
Менее 1,50
2
Малая: дефект маловероятен. Отказы никогда
не связаны с идентичными процессами
Менее 1
из 1500000
Более 1,67
1
На следующем этапе исследования определяется балл обнаружения
D
рассматриваемого дефекта [97] в процессе эксплуатации ПЭУ. Величина
D
измеряется в баллах и изменяется от 1 до 10 в зависимости от достоверности
обнаружения данного дефекта. Типовые значения балла обнаружения
для ПН приведены в табл. 6.5, 6.6.

Повышение эффективности эксплуатации
погружных электроустановок нефтедобычи
160
Таблица 6.5
Шкала баллов обнаружения
D
FMEA-конструкции для ПЭУ
Категория
Критерии обнаружения
D
при используемой системе контроля
Балл
D
Абсолютная
неопределенность
Существующая система контроля не обнаружит
или не может обнаружить потенциальные причины/
механизм и последующий вид дефекта
10
Очень плохое
Очень плохие шансы обнаружения потенциальных
причины/механизма и последующего вида дефекта
при существующей системе контроля
9
Плохое
Плохие шансы обнаружения потенциальных причи-
ны/механизма и последующего вида дефекта
при существующей системе контроля
8
Очень слабое
Очень ограниченные шансы обнаружения потенциальных
причины/механизма и последующего вида дефекта
при существующей системе контроля
7
Слабое
Ограниченные шансы обнаружения потенциальных
причины/механизма и последующего вида дефекта
при существующей системе контроля
6
Умеренное
Умеренные шансы обнаружения потенциальных причины/
механизма и последующего вида дефекта при существую-
щей системе контроля
5
Умеренно
хорошее
Умеренно высокие шансы обнаружения потенциальных
причины/механизма и последующего вида дефекта
при существующей системе контроля
4
Хорошее
Высокие шансы
3
Очень хорошее
Очень высокие шансы
2
Почти наверняка
Существующая система контроля почти всегда
обнаруживает потенциальную причину дефекта
1
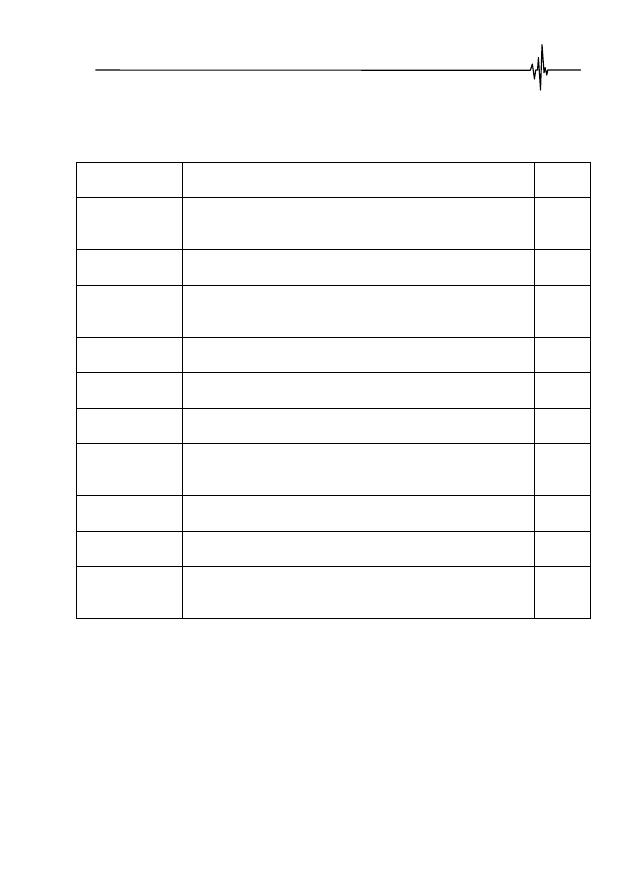
Глава 6. Оценка надежности и приоритетности ремонтов для электрооборудования
нефтяной промышленности с учетом возможного риска
161
Таблица 6.6
Шкала баллов обнаружения
D
FMEA-процесса
применительно к ПЭУ
Категория
Критерии: вероятность обнаружения дефекта
при контроле процесса
Балл
D
Почти
невозможно
Нет известного контроля для обнаружения вида дефекта
в производственном процесса (по практическим данным
для ПЭУ отсутствует)
10
Очень плохое
Очень низкая вероятность обнаружения вида дефекта
действующими системами контроля
9
Плохое
Низкая вероятность обнаружения вида дефекта
действующими системами контроля (расчленение узла,
клин, К.З. обмотки ПЭД)
8
Очень слабое
Очень низкая вероятность обнаружения вида дефекта
действующими системами контроля
7
Слабое
Низкая вероятность обнаружения вида дефекта
действующими системами контроля
6
Умеренное
Умеренная вероятность обнаружения вида дефекта
действующими системами контроля
5
Умеренно
хорошее
Умеренно высокая вероятность обнаружения вида дефекта
действующими системами контроля (слом вала
(шлицевой муфты), отсутствие «звезды»)
4
Хорошее
Высокая вероятность обнаружения вида дефекта
действующими системами контроля
3
Очень хорошее
Очень высокая вероятность обнаружения вида дефекта
действующими системами контроля
2
Почти
наверняка
Действующие системы контроля почти наверняка
обнаружат вид дефекта. Для подобных процессов
известны надежные методы контроля
1
После получения экспертных оценок
, ,
S O D
вычисляют приоритетное
число риска (
ПЧР
) [97]:
ПЧР S O D
.
(6.1)
Для дефектов, имеющих несколько причин, определяют соответственно
несколько ПЧР. Каждый ПЧР может иметь значения от 1 до 1000.
Согласно алгоритму работы по методу FMEA-анализа, приведенному
на рис. 6.2, для «обобщенного балла критичности» должна быть установлена
величина критического значения приоритетного числа риска – так называе-
мая критическая граница (
гр
ПЧР
), которая находится в пределах значений
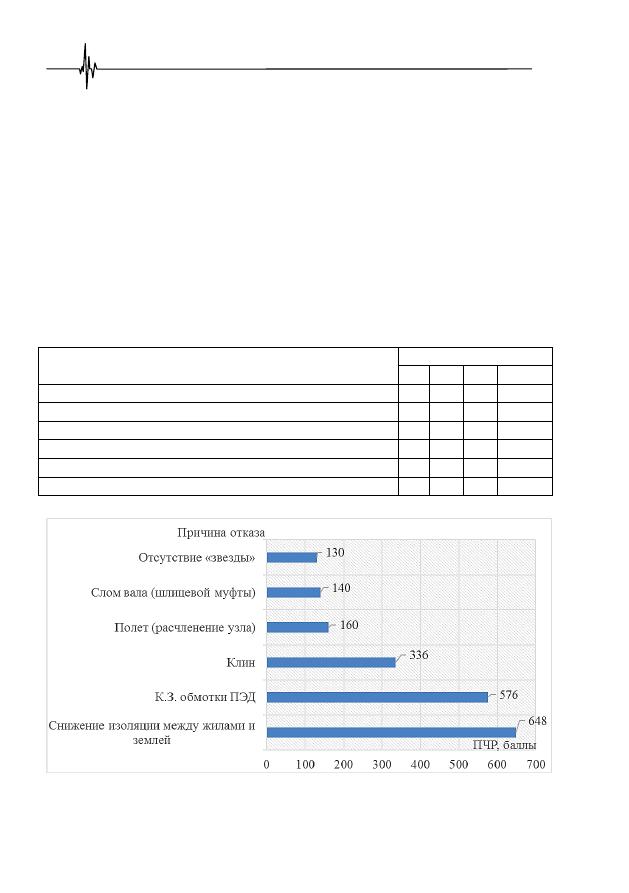
Повышение эффективности эксплуатации
погружных электроустановок нефтедобычи
162
ПЧР
100–125. Для дефектов с
ПЧР
> 100, в некоторых случаях > 125, сле-
дует вести доработку конструкции ПЭУ и ПЭД либо изменение, совершен-
ствование производственного процесса [97]. Анализируя данные, получен-
ные в процессе исследования и представленные в табл. 6.7, можно устано-
вить, что все рассмотренные технологические нарушения имеют
ПЧР
от 111 до 648 и, следовательно, высокий риск возникновения. Данное об-
стоятельство еще раз свидетельствует об актуальности темы исследования
и необходимости внедрения в производственный процесс добычи углеводо-
родов результатов, полученных в предыдущих главах книги.
Таблица 6.7
Основные причины, влияющие на технологический отказ в работе ПЭУ,
с вычислением приоритетного значения риска
Причина
Баллы
S
O
D
ПЧР
Полет (расчленение узла)
5
4
8
160
Клин
7
6
8
336
Слом вала (шлицевой муфты)
7
5
4
140
Отсутствие «звезды»
6
5
4
130
Снижение изоляции между жилами и землей
8
9
9
648
К.З. обмотки ПЭД
9
8
8
576
Рис. 6.3.
Диаграмма Парето основных причин,
влияющих на отказ в работе ПЭУ
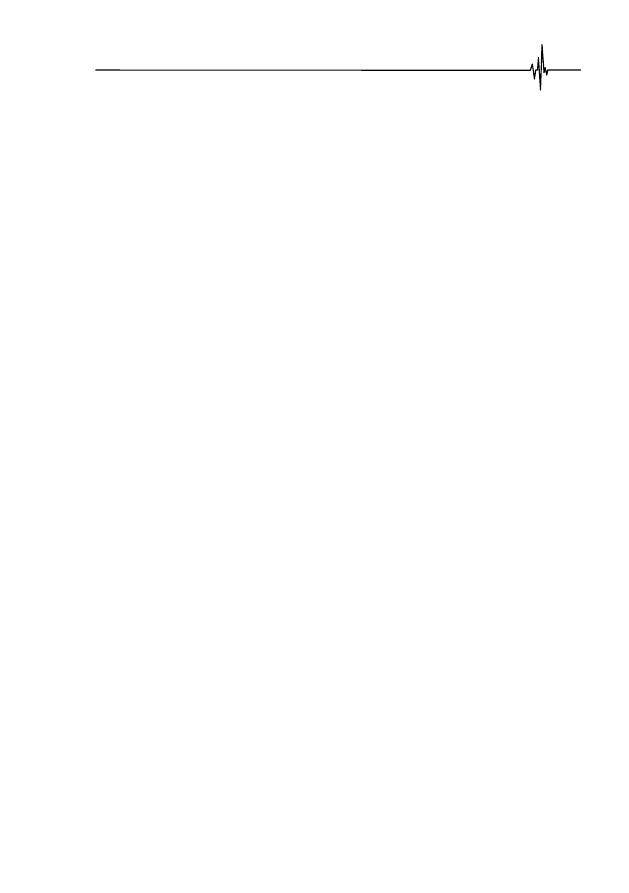
Глава 6. Оценка надежности и приоритетности ремонтов для электрооборудования
нефтяной промышленности с учетом возможного риска
163
На основании выполненного анализа и проведенных расчетов по методу
FMEA-анализа выполняется построение диаграммы Парето. Она использу-
ется при выявлении наиболее значимых и существенных факторов, влияю-
щих на возникновение несоответствий или брака. Это дает возможность ус-
тановить приоритет действиям, необходимым для решения проблемы.
На графике, представленном на рис. 6.3, отражены основные причины, ран-
жированные по значимости влияния на отказ в работе ПЭУ.
С использованием принципа Парето 80/20 [93] установлено, что
для снижения количества технологических нарушений и повышения эффек-
тивности эксплуатации ПЭУ менеджменту и техническим руководителям
предприятий нефтяной отрасли следует обратить внимание на исключение
либо снижение количества дефектов на оборудовании скважины по причине
снижения изоляции между токопроводящими жилами и землей. На втором
месте по значимости и степени влияния на безотказность и надежность экс-
плуатации находятся дефекты, связанные с коротким замыканием в обмотке
ПЭД. Третье место принадлежит технологическим отказам, связанным с закли-
ниванием УЭЦН. Как показали исследования, в том числе проведенные
в предыдущих главах, эффективность эксплуатации достигается за счет
снижения количества аварийных отказов в работе оборудования ПЭУ, и осо-
бое внимание следует уделять надежности функционирования узлов
«кабель – ПЭД» и УЭЦН как наиболее ответственных и наименее надежных
узлов системы. Практика эксплуатации ПЭУ, и в особенности ПЭД, является
информативным показателем испытания оборудования на надежность,
именно поэтому необходим тщательный анализ возникающих в процессе
эксплуатации дефектов, который позволит дать оценку степени влияния
факторов на проблему эффективности эксплуатации ПЭУ при анализе трех
основных показателей: значимость причины, частота ее возникновения
и вероятность обнаружения. Последующий расчет и экономический анализ
рисков возникновения отказов, расчет рентабельности, оптимизация произ-
водственного процесса и решение описанных проблем позволят достигнуть
главной цели – стабильного экономического роста и эффективной эксплуа-
тации ПЭУ и его элементов.
6.4. Оценка интегральных показателей надежности ПЭУ
В энергоснабжении нефтедобычи, как и в электросетевых компаниях
(ПАО «Россети») [62, 74], в настоящее время получает все большее распро-
странение новая концепция развития, направленная на повышение качества
эксплуатации и технического обслуживания за счет перехода на риск-
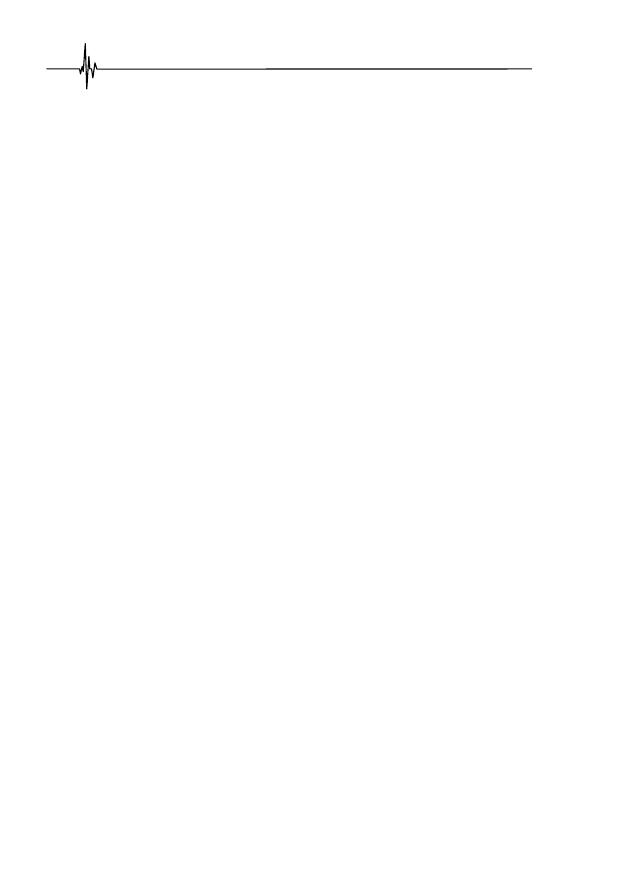
Повышение эффективности эксплуатации
погружных электроустановок нефтедобычи
164
ориентированное управление и основанная на цифровизации и анализе
больших ИБД [98]. Она опирается на методологию комплексной оценки теку-
щего технического состояния объектов СЭС НП с помощью интегральных
показателей надежности как технико-экономического обоснования корректно-
го управления жизненными циклами электрооборудования [93, 96].
На сегодняшний день в нефтяной отрасли России представляется целе-
сообразным использование стандарта [88], учитывающего ТС и риски
при планировании ТОиР ПЭУ, по аналогии с тем, как это производится
для электрооборудования электросетевых компаний [98]. В своих исследо-
ваниях [42, 58] авторы предлагают методологию определения индекса тех-
нического состояния (ИТС) для ПЭУ нефтедобычи. Ее сущность и основное
содержание кратко можно сформулировать в следующих положениях.
Перспективное планирование текущих и перспективных технических
мероприятий в эксплуатации оборудования, оценка его ТС и эффективности
производятся в соответствии с [98] при составлении графиков ремонтов
(годовых, многолетних), планировании и реализации комплексной програм-
мы технического перевооружения и реконструкции, после технических воз-
действий, изменяющих ТС ПЭУ. Корректировка ремонтной программы
осуществляется после внезапных отказов оборудования и проведения
внеплановых ремонтов с оценкой ТС, но не реже одного раза в год.
В соответствии с методологией определения ИТС ПЭУ [92, 93] форми-
руется ранжированный состав оборудования, упорядоченный по критерию
уменьшения вероятности возникновения отказа по техническим причинам
в зависимости от уровня эксплуатации, возможных последствий технологи-
ческих нарушений и действий по профилактике, определяется вид воздейст-
вия на оборудование. В этом списке наименьшему значению ИТС (критиче-
ский уровень) соответствует наибольший приоритет по изменению эксплуа-
тационного состояния и реализации технического воздействия (проведение
внепланового ТОиР, вывод из эксплуатации, контроль ТС, дополнительное
диагностирование и т. д.). В зависимости от состава, сложности и кон-
структивного исполнения оборудования расчет ИТС осуществляется для
следующих уровней:
– объект оборудования ПЭУ (ЭЦН, ПЭД, питающий погружной кабель,
силовой трансформатор и др.);
– многокомпонентный объект (ЭПУ);
– комплекс объектов (парк ЭПУ).
Это позволяет задать конкретные весовые коэффициенты признаков
при переходе от нижнего уровня к более высокому [93, 96]. Расчет ИТС
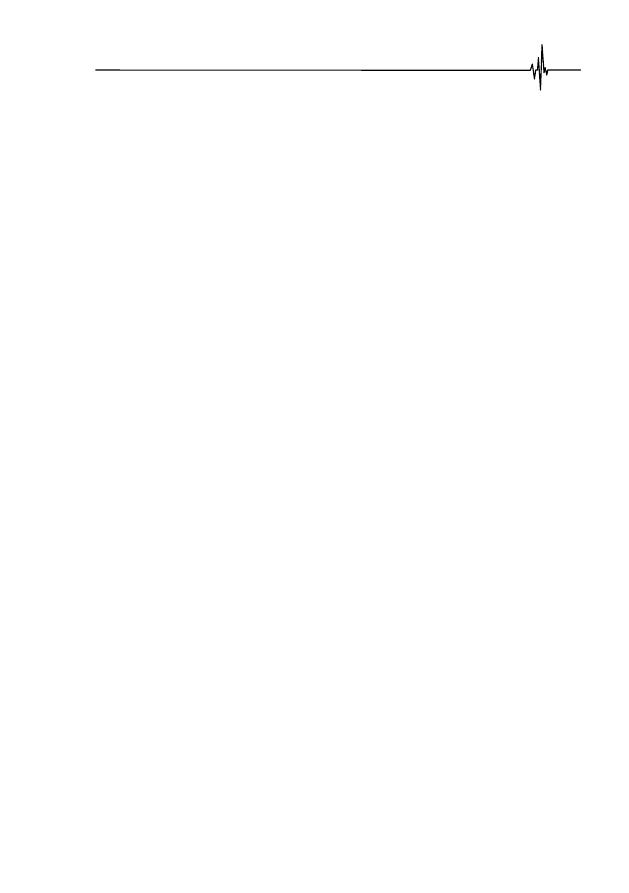
Глава 6. Оценка надежности и приоритетности ремонтов для электрооборудования
нефтяной промышленности с учетом возможного риска
165
выполняется на основе алгоритмов оценки [94]. Его результаты можно
сформулировать для каждого объекта ПЭУ в следующем виде:
– определение ИТС в относительных единицах в диапазоне 0–100, причем
значению «0» соответствует наихудшее значение показателя, значению
«100» – наилучшее, то есть используется принцип «больше – лучше»;
– в зависимости от состояния эксплуатации ПЭУ определяется вид
управляющего воздействия.
Для определения уровня физического износа ПЭУ необходимо привести
значение ИТС в диапазон 0–1 (выполнить деление показателя ИТС на 100):
1
Износ
ИТС
.
(6.2)
В соответствии с нормативными требованиями [93, 94] по условиям
стратегий, классификации и алгоритмам формирования технического воз-
действия на объекты ПЭУ значения ИТС разбиваются на пять равных интер-
валов, для которых устанавливаются конкретные виды качественного разли-
чия признаков (видов) ТС.
Положительным моментом данной методики является то, что по резуль-
татам оценки ТС ПЭУ можно прогнозировать изменения его ИТС и время
наступления предельного состояния, при котором эксплуатация будет
невозможна либо экономически не выгодна [97]. Названная методика пред-
полагает вероятностный расчет наступления негативного события (отказа),
а также возможных последствий для каждого известного технологического
нарушения. В результате определяется процедура управления жизненным
циклом ПЭУ в виде разработки, корректировки и оптимизации состава, вида,
периода проведения технологических воздействий на оборудование.
Существенный недостаток описанной методики заключается в том, что
алгоритм расчета остаточного ресурса построен на концепции постепенных
отказов – то есть для определения ТС используется ограниченный состав
набора факторов, обусловленных естественными процессами старения и из-
носа оборудования [95].
Кроме них в эксплуатации часто возникают внезапные отказы из-за воз-
действий нерасчетных нагрузок, резкопеременных режимов работы
и критических ЭФВ внешнего и внутреннего происхождения. Поэтому акту-
альны исследования, разработка и внедрение новых методов управления
жизненными циклами ПЭУ ПН для повышения их надежности и эффек-
тивности эксплуатации за счет использования различных данных.
Далее предлагается методология определения и ранжирования надежно-
сти сложных энергетических объектов, основанная на ранговом подходе [96].
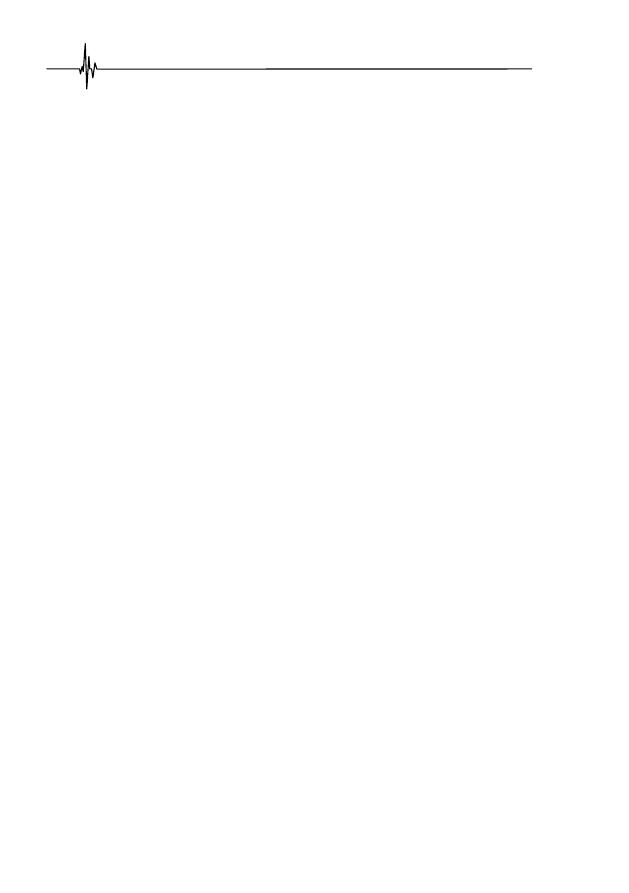
Повышение эффективности эксплуатации
погружных электроустановок нефтедобычи
166
Она позволяет идентифицировать наиболее ненадежные элементы ПЭУ
ПН, произвести анализ и оценку факторов, характеризующих надежность
и эффективность функционирования оборудования, сравнить и ранжировать
параметры многокомпонентных систем, выполнить их оценку на основе ана-
лиза разнотипных признаков в виде расчетного коэффициента ранговой
корреляции [99].
Основной результат здесь заключается в комплексной замене множества
независимых признаков, характеризующих эксплуатационные параметры,
надежность функционирования, экономичность, безопасность ПЭУ одним
интегральным показателем, адекватно и точно учитывающим свойства всех
показателей системы.
Разработанные методы и алгоритмы имеют очевидную научную
и практическую направленность как база для создания автоматизированной
системы управления жизненными циклами ПЭУ, обеспечивая технических
работников информационной и методической поддержкой.
Принципиально важно отметить, что для управления эксплуатацией
и принятия решений по повышению надежности оборудования в настоящее
время можно эффективно применять различные методы и алгоритмы сбора,
обработки информации для определения ТС ПЭУ. В большинстве случаев
названные методы носят прикладной характер исследования и основаны
на использовании положений квалиметрии с ее приложениями [95, 99]. Изу-
чение возможных путей поиска новых решений и расширение существующих
знаний позволяет более обоснованно и всенаправленно решать поставленные
задачи по повышению надежности и управляемости комплекса ПЭУ ПН.
На сегодняшний день при осуществлении бизнес-процессов планиро-
вания ТОиР, управлении работами, контроле состояния производственных
активов, служб управления эксплуатацией ПН недостаточно полно учиты-
ваются сведения о надежности оборудования [82, 84].
В аналогичных случаях в энергоснабжении используется детерминиро-
ванный подход по критерию
n – i
[97]. При использовании этого критерия
предполагается, что при исключении
i
составляющих из анализируемого
комплекса, в котором исходно в нормальном режиме работают
n
элементов,
он сохранит свою работоспособность и параметры режима в пределах до-
пустимых значений. При этом наиболее тяжелые отказы определяются тре-
бованиями эксплуатации [31, 32].
Приоритетность заявок на ремонты отдельных составляющих комплек-
са ПЭУ, в том числе требующих внепланового обслуживания или ремонта,
как правило, определяется сроками и объемом работ более ответственного
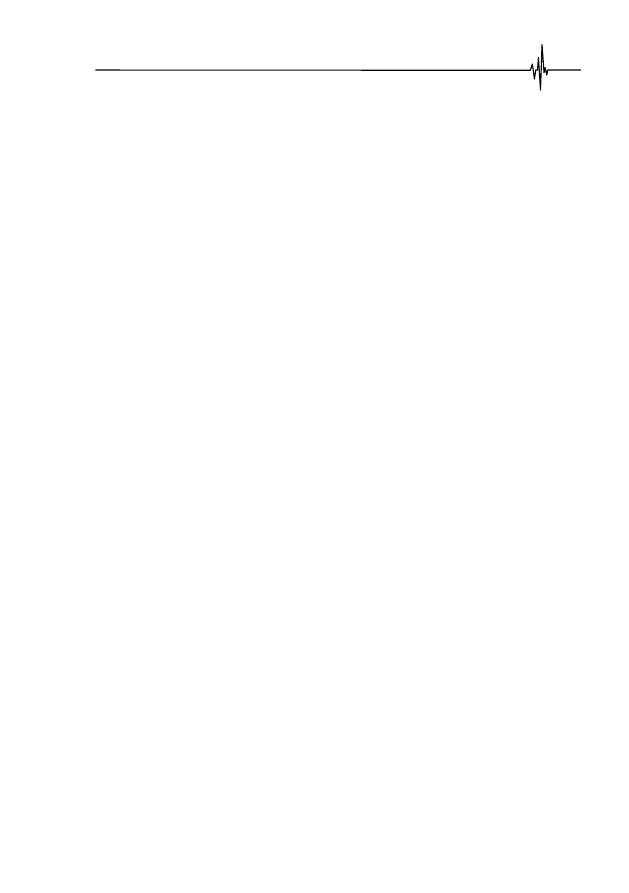
Глава 6. Оценка надежности и приоритетности ремонтов для электрооборудования
нефтяной промышленности с учетом возможного риска
167
оборудования, а также длительностью и важностью для ПН конкретного
ремонта [44]. Собственно, решение о проведении внепланового ТОиР в дан-
ном случае принимается на основании опыта и личного мнения работников,
осуществляющих эксплуатацию оборудования.
Стоит отметить, что в реальных условиях эксплуатации в период про-
ведения ремонтной кампании при плотном графике принятие взвешенного
решения по приоритетности ремонтов отдельных составляющих ПЭУ тре-
бует объективного учета надежности всего комплекса.
Обращая внимание на требование повышения качества эксплуатации
и снижения ущерба при возможных технологических нарушениях, целесообраз-
но использовать количественную оценку интегральных показателей индивиду-
альной надежности ПЭУ и его конкретных объектов. Для этого необходимо
произвести выборку показателей, которые с достаточной полнотой отражают
состояние ПЭУ и уровень его надежности, например сведения об отказах, дли-
тельности простоев, количестве плановых и аварийных ремонтов и т. д.
При совместной обработке названных показателей возникают опреде-
ленные трудности, обусловленные в первую очередь различием единиц из-
мерения, шкал и масштабов, а также необходимостью их комплексного объ-
единения в одном интегральном показателе. Характерная особенность этого
объединения ‒ совместное использование показателей и признаков с объек-
тивной численной оценкой в различных шкалах измерений, в частности
количественных (КШ), порядковых (ПШ) и номинальных (НШ). При этом
используются общие принципы квалиметрии и известные рекомендации
по выбору приоритетных решений, основанные на методах анализа много-
критериальных задач [97, 99].
Далее целесообразно сформулировать и представить основные положе-
ния методики оценки приоритетности выполнения ТОиР и ТПиР для ПЭУ
с целью долгосрочного планирования и реализации ремонтных циклов
для ПН. Эта оценка необходима центру управления эксплуатации ПЭУ
для принятия обоснованных решений по выводу в ремонт конкретного
объекта по плановым заявкам.
Данная методика сформирована как часть автоматической информаци-
онной системы поддержки персонала и реализуется с учетом следующих
положений:
– ранжирование объектов по надежности работы и возможному ущербу
при аварийном отключении;
– определение слабых мест ПЭУ и основных причин ухудшения ТС;
– оценка качества управления эксплуатацией ПЭУ [97].
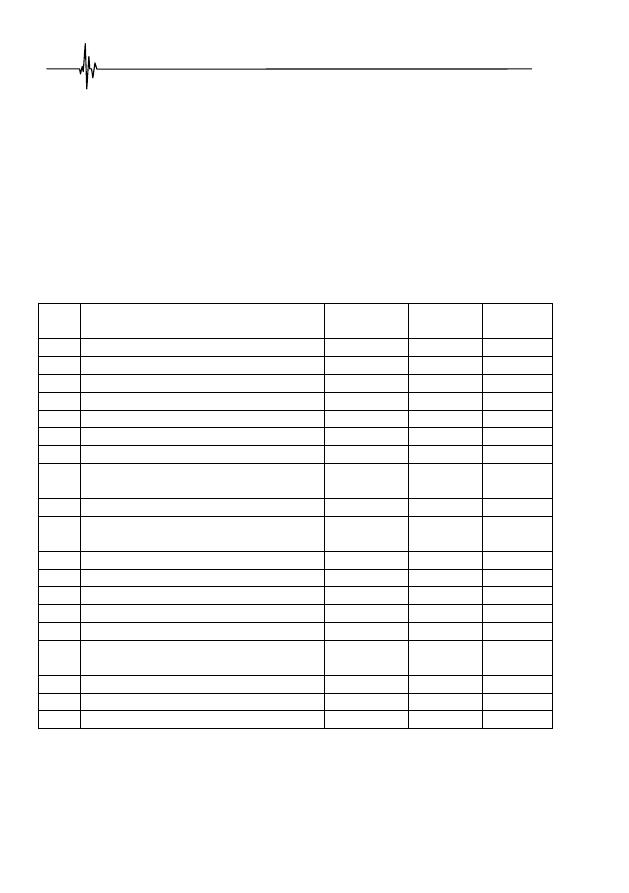
Повышение эффективности эксплуатации
погружных электроустановок нефтедобычи
168
Отметим, что в рамках представленной статьи дальнейшие расчеты
по предложенной методике будут производиться для ПЭД как наиболее ответ-
ственного и аварийного узла ПЭУ и непосредственно ЭПУ [92, 94, 100]. Прежде
всего определяется перечень показателей, характеризующих надежность
ПЭД (табл. 6.8). Стоит отметить, что данные показатели выбираются инди-
видуально в зависимости от требуемых задач исследования, условий экс-
плуатации и т. д., то есть задаются оператором.
Таблица 6.8
Выборка показателей, необходимых для анализа надежности ПЭД
№ п/п
Наименование
показателя ПЭД
Условное
обозначение
Единица
измерения
Тип
показателя
1
Номинальное напряжение
U
ном.
кВ
–
2
Средний срок службы
Т
сл.
год
S
2
3
Наработка после капитального ремонта
Т
кр.
год
S
2
4
Число отключений по аварийной заявке
n
ав.
–
S
2
5
Техническое состояние
ТС
–
S
1
6
Конструктивное исполнение
КИ
–
–
7
Последствия отказа
ПО
–
S
1
8
Относительная длительность простоя
в аварийном ремонте
δ
T
ав.
отн. ед.
S
2
9
Номинальная мощность
S
н
MBA
10
Температура обмотки статора
электродвигателя (по сопротивлению)
t
°C
S
2
11
КПД
КПД
%
S
1
12
Средняя нагрузка
δ
S
ср.
отн. ед.
S
2
13
Максимальная нагрузка
δ
S
макс.
отн. ед.
S
2
14
Среднее время восстановления
Т
в.ср.
часы
S
1
15
Средняя наработка до отказа
Т
отк.ср.
часы
S
2
16
Число КЗ в обмотке статора
после капитального ремонта
n
к.з.
–
S
2
17
Индекс технического состояния
ИТС
о.е.
–
18
Производитель
ПР
–
–
19
Интегральный показатель надежности
Р
о.е.
–
Они в основном формально определены паспортами оборудования,
имеют высокую информативность и достоверность. Названные показатели
систематически предоставляются в центры управления энергоснабжением
ПН в соответствии с руководящими документами и существующими регла-
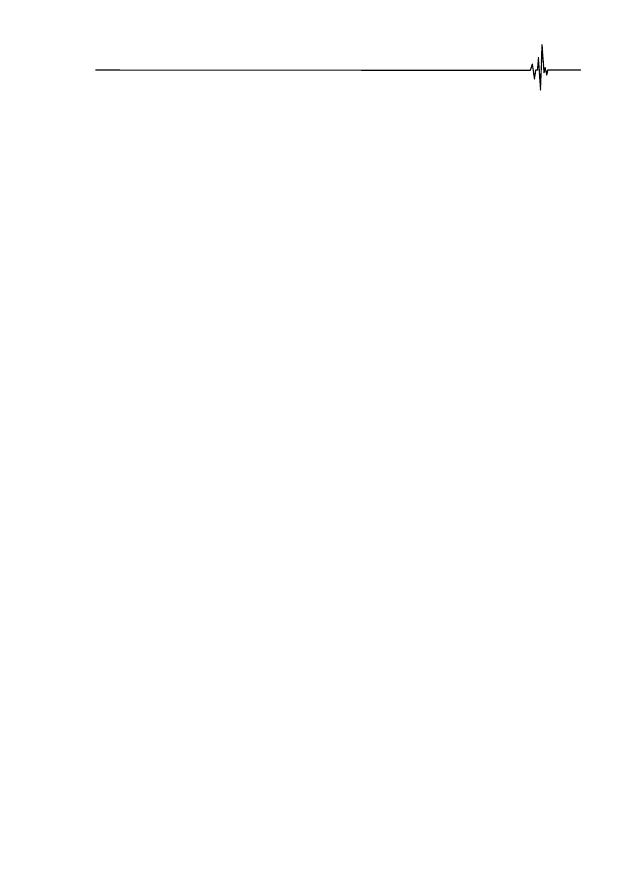
Глава 6. Оценка надежности и приоритетности ремонтов для электрооборудования
нефтяной промышленности с учетом возможного риска
169
ментами [93]. Отметим, что методика определения коэффициента риска не-
гативных последствий (РНП) при аварийном отказе ПЭД была ранее сфор-
мирована на основе диаграммы Парето (см. рис. 6.3).
Для выполнения расчетов по описываемой методологии по определению
интегрального показателя надежности необходимо произвести обработку
исходных данных, которая заключается в преобразовании выделенных призна-
ков из количественной шкалы в порядковую и производится в несколько этапов.
1. Необходимо определить диапазон изменения количественных показа-
телей выбранных признаков по выражению
max
min
(П )
(П
П
),
j
j
j
L
(6.3)
где
max
i, j
1,
П
max
j
i
n
П
,
min
i, j
1,
П
min
j
i
n
П
, которые делятся на пять
интервалов по аналогии с методикой определения ИТС [98]. Каждому
из интервалов соответствует порядковый номер
K
= 1÷5, который является
его количественным аналогом (рангом).
2. Одним из необходимых требований качественного сравнения объек-
тов ПЭУ является формирование перечня независимых признаков с учетом
их причинно-следственных взаимосвязей. Использование зависимых при-
знаков отрицательно влияет на точность расчетов, вносит явное доминиро-
вание и направленность, а также величину погрешности, значение которой
может существенно искажать полученные результаты [93, 96]. Для оценки
направленности и взаимосвязи признаков используется ранговый коэффи-
циент корреляции.
3. Для расчета интегрального показателя необходимо учитывать на-
правленность изменения используемых признаков. Принято использовать
два типа направленности –
S
1
, если увеличение показателя приводит к уве-
личению надежности и эффективности функционирования ПЭУ (ПЭД), и
S
2
,
если увеличение показателя приводит к уменьшению надежности и эффек-
тивности функционирования ПЭУ (ПЭД). Каждому названному типу на-
правленности соответствуют количественные оценки в виде числовых ин-
тервалов: для
S
1
K
= 1÷5, для
S
2
соответственно
K
= 5÷1. В табл. 6.9 пред-
ставлена выборка наиболее значимых показателей надежности для ПЭД,
определенных по критерию
S
2
.
Определение коэффициента РНП при аварийном отказе ПЭД.
На следующем этапе работы по описываемой методике необходимо произ-
вести оценку риска аварийного отключения исследуемого оборудования,
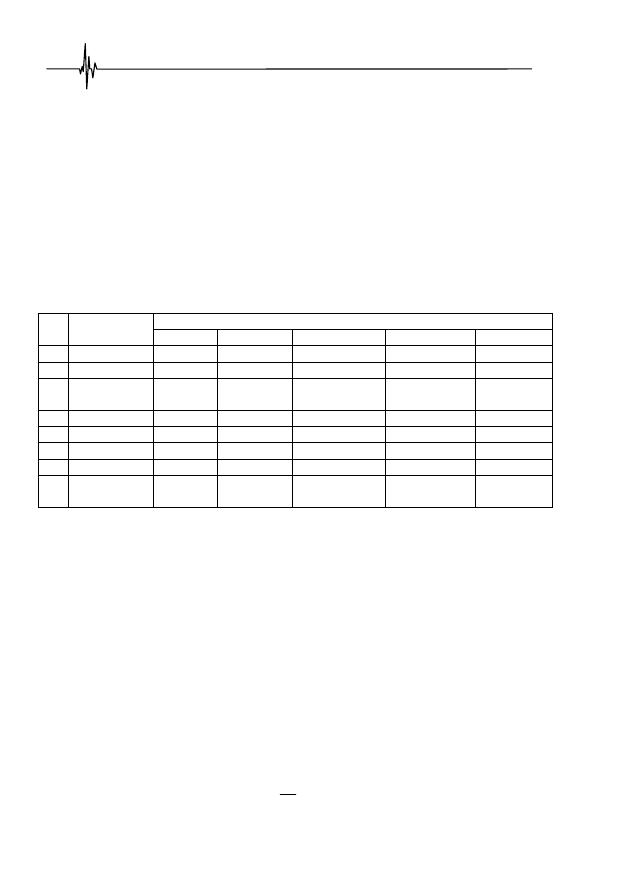
Повышение эффективности эксплуатации
погружных электроустановок нефтедобычи
170
в данном случае это ПЭД. Этот риск отличается тем, что с позиций управле-
ния эксплуатацией ПЭУ ПН, и в частности ПЭД, ущерб в основном связан
с такими негативными экономическими последствиями, как недобор нефти.
Это приводит к ухудшению показателей технико-экономической эффектив-
ности ПЭУ ПН или его части. С этой точки зрения приоритетность в очеред-
ности ремонта при прочих равных условиях должна быть у тех ПЭД, кото-
рые при аварийном отказе создают наибольшие проблемы для ПН в послеа-
варийном режиме.
Таблица 6.9
Ранжирование показателей надежности для ПЭД,
определенных по критерию S
2
№
п/п
Тип
признака
Номер разновидности признаков
5
4
3
2
1
1
Т
сл
.
, лет
< 1
1–2
2–3
3–4
> 5
2
t
, °C
< 115
115–130
130–140
140–150
> 150
3
Т
отк.ср
.
, час
< 15000
15000–
18000
18000–19000
19000–21000
> 21000
4
n
ав
.
0
1
2
3
> 3
5
n
к.з.
0
1
2
3
> 3
6 ИТС
0,85–1
0,7–0,85
0,5–0,7
0,25–0,5
< 0,25
7
Р
< 0,2
0,2–0,4
0,4–0,6
0,6–0,8
0,8–1
8
Техническое
состояние
Показа-
тельное
Хорошее
Удовлетвори-
тельное
Зона риска
Дефектное
Произведем количественную оценку аварийного отказа ПЭД, для чего
введем коэффициент риска, который для выбранного парка ПЭУ характери-
зует вес возможных негативных последствий при аварийном отказе ПЭД
с точки зрения управления его техническим состоянием и технико-эконо-
мической эффективностью.
На рис. 6.1 представлены названные отказы для ПЭД, рассмотрены их
основные причины и предложены действия по профилактике.
Для взаимного сравнения возможных негативных последствий отказа
по степени их воздействия на ТС ПЭУ (ПЭД) определим удельный вес
риска для каждого критерия отказа единицы ПЭУ в о. е. Воспользуемся
методом анализа иерархий [99]. В табл. 6.10 представлена матрица попар-
ных сравнений негативных последствий (факторов) аварийных отказов
ПЭД, где
а
ij
– отношение фактора
i
к фактору
j
:
1
,
1.
ji
ii
ij
a
a
a
(6.4)
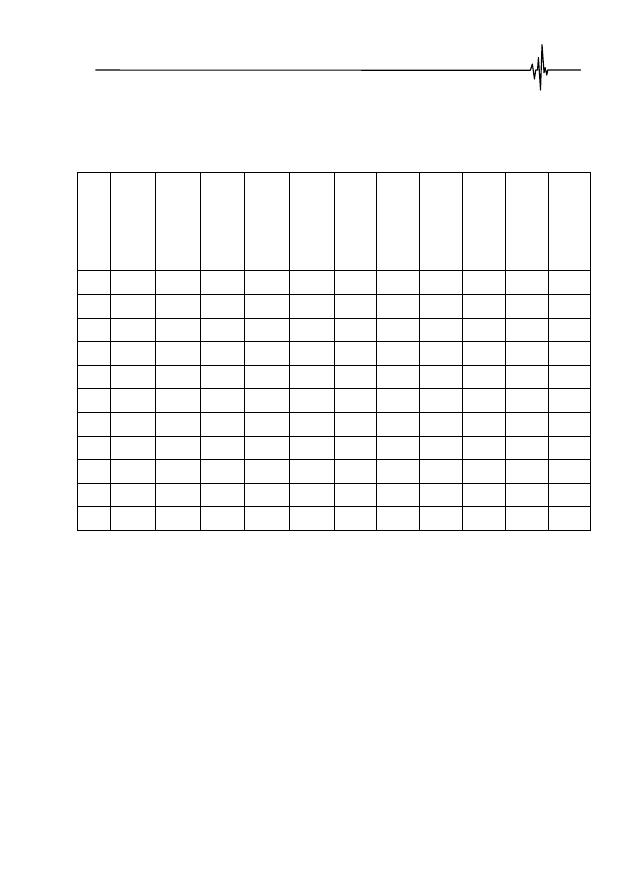
Глава 6. Оценка надежности и приоритетности ремонтов для электрооборудования
нефтяной промышленности с учетом возможного риска
171
Таблица 6.10
Матрица попарных сравнений негативных последствий
аварийных режимов для ПЭД
№
с
обы
тия
1
2
3
4
5
6
7
8
9
10
Уд
. в
ес
, γ
i
,
о.
е.
1
1,00
3,00
3,00
5,00
5,00
7,00
9,00
7,00
8,00
9,00
0,342
2
0,33
1,00
3,00
5,00
3,00
5,00
7,00
2,00
7,00
9,00
0,208
3
0,14
0,25
1,00
2,00
0,5
0,5
3,00
1,00
3,00
5,00
0,07
4
0,11
0,11
0,2
1,00
0,33
0,5
2,00
0,33
2,00
3,00
0,039
5
0,14
0,2
2,00
3,00
1,00
3,00
4,00
3,00
3,00
5,00
0,114
6
0,11
0,12
0,2
2,00
0,33
1,00
3,00
3,00
3,00
5,00
0,072
7
0,11
0,11
0,12
0,5
0,2
0,2
1,00
0,14
0,33
3,00
0,024
8
0,11
0,11
0,5
2,00
0,5
1,00
5,00
1,00
3,00
3,00
0,066
9
0,11
0,11
2,00
0,33
0,2
0,33
3,00
0,2
1,00
3,00
0,047
10
0,11
0,11
0,2
0,14
0,12
0,2
0,33
0,2
0,5
1,00
0,017
∑ S 2,27
5,12
12,2
20,97 11,18 18,73 37,33 17,87 30,83
46
1,00
Строго говоря, результаты расчетов в табл. 6.10 получены путем попар-
ного сравнения аварийных событий для ПЭД по качественной шкале
с последующим преобразованием в баллы. Для этого использованы основ-
ные положения метода анализа иерархий – составлена матрица из элементов,
характеризующих интенсивность проявления фактора
i
относительно факто-
ра
j
, оцениваемая по шкале интенсивности от 1 до 9. Числовые оценки имеют
следующий смысл: 1 – равная важность; 3 – умеренное превосходство;
5 – значительное превосходство; 7 – сильное превосходство; 9 – очень силь-
ное превосходство. В спорных случаях использованы промежуточные оценки
с четными баллами – 2, 4, 6, 8.
Использованы положения метода экспертных оценок с выбором баллов
по результатам опроса экспертов – специалистов служб управления эксплуа-
тации ПЭУ ПН – о тяжести негативных последствий отказов ПЭД и приори-
тетности действий при ликвидации аварийной ситуации [100].
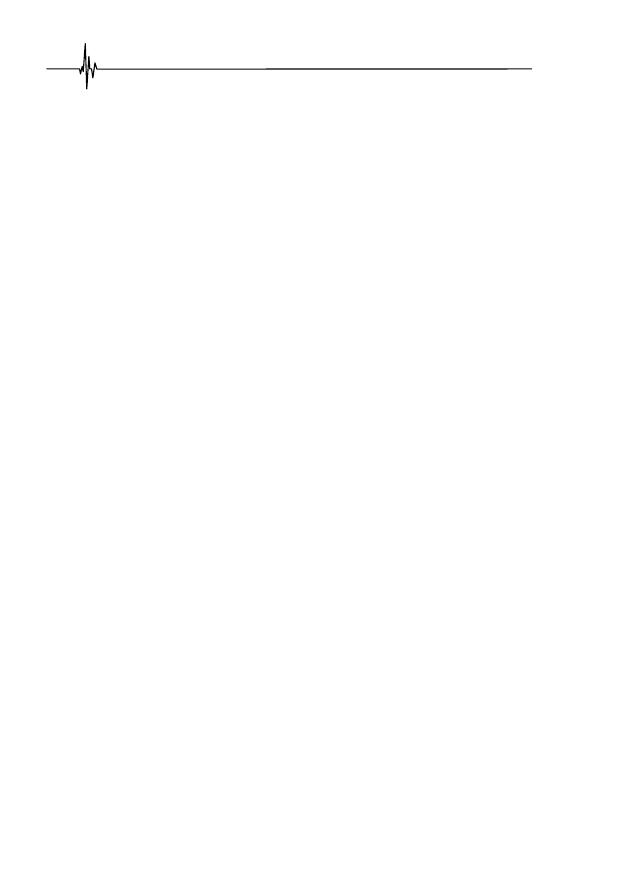
Повышение эффективности эксплуатации
погружных электроустановок нефтедобычи
172
Выбор баллов определяется практически для большинства позиций
классификации сокращением подачи ПЭД (вплоть до полного прекращения)
из-за отказа элементов ПЭУ. Это связано с остановкой всего комплекса на
время собственно ремонта, ликвидации непосредственных последствий
с учетом необходимого контроля ТС до и после аварии, спускоподъемных
и вспомогательных операций.
После формирования матрицы попарных сравнений негативных послед-
ствий аварийных отказов находим сумму элементов каждого столбца
табл. 6.10:
1
2
...
.
j
j
nj
S
a
a
a
(6.5)
Делим все элементы матрицы на сумму элементов соответствующего
столбца:
A
i,j
=
a
i,j
/
S
j
.
(6.6)
Действия (6.4) и (6.5) представляют собой нормирование, результаты
которого – средние значения строк нормированной матрицы – приведены
в последнем столбце, они представляют собой удельный вес (по табл. 6.10)
каждого из рассматриваемых негативных последствий аварийного отказа.
Результаты проведенных расчетов показали, что наиболее существенным
негативным по своим последствиям является аварийный отказ по критерию 1
«К.З. обмотки ПЭД» в соответствии с блок-схемой отказов, представленной
на рис. 6.3, с удельным весом 0,342. Вторым по тяжести является аварийный
отказ по критерию 2 «Пробой обмотки статора» с удельным весом 0,208. Третий
в списке отказов – № 5 «Отсутствие «звезды» (полет)» с удельным весом 0,114.
Для примера практической реализации предложенной методики авторами
работы использована база данных по технологическим нарушениям за 2018–
2022 гг. на ПЭУ ПН Поволжья, произведена выборка десяти наиболее ава-
рийных типов ПЭД с учетом мощности и типоразмера. Строго говоря, каче-
ственного результата при работе по описываемой методике можно
добиться даже при исследовании надежности ПЭУ и его элементов в преде-
лах локального набора оборудования (куст, скважина и т. д.) с учетом всех
местных условий эксплуатации и ведения режима.
На следующем этапе для каждого из выбранных ПЭД определим
коэф-
фициент риска наступления негативных последствий при аварийном
отказе
по выражению
1
,
n
i
i
i
P
B
(6.7)
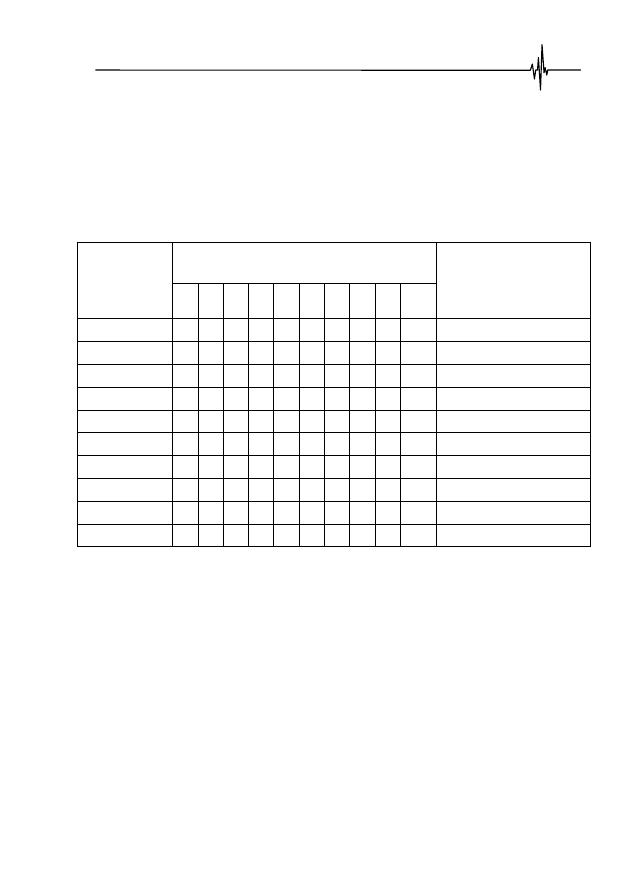
Глава 6. Оценка надежности и приоритетности ремонтов для электрооборудования
нефтяной промышленности с учетом возможного риска
173
где
γ
i
– удельный вес для каждого
i
-го негативного последствия послеава-
рийного режима;
B
i
= [0, 1] – коэффициент актуальности наступления ава-
рийного события (
В
= 1, если отказ рассматриваемого ПЭД приводит к
i
-му
негативному последствию,
B
= 0 соответственно, если нет).
Таблица 6.11
Результаты расчетов по определению коэффициента риска
при аварийном отключении ПЭД
Наименование
ПЭД
Номер негативного последствия
после аварийного режима
Коэффициенты риска
аварийного отключения
ПЭД,
Ро.е.
1
2
3
4
5
6
7
8
9
10
ПЭД-32-103
1
1
1
1
1
0
1
1
1
1
0,928
ПЭД-32-117
1
1
0
1
1
1
1
1
1
1
0,930
ПЭД-45-103
1
1
1
1
1
1
1
1
1
0
0,98
ПЭД-45-117
1
1
1
1
1
1
1
1
1
0
0,98
ПЭД-50-103
1
1
0
1
1
0
1
1
0
0
0,793
ПЭД-50-117
1
1
1
1
0
0
0
1
0
0
0,725
ПЭД-56-103
1
1
1
0
1
1
1
1
1
1
0,961
ПЭД-56-117
1
1
1
1
1
1
0
1
0
1
0,928
ПЭД-63-117
1
1
0
1
0
0
1
1
1
1
0,744
ПЭД-90-117
1
1
1
1
1
1
0
1
1
0
0,958
В табл. 6.11 приведены результаты расчетов коэффициентов актуально-
сти и коэффициентов риска аварийного отключения для рассматриваемых
ПЭД. Отметим, что исходными данными при определении коэффициентов
актуальности аварийного события послужила описанная выше ИБД по ава-
рийности:
1
,
n
i
j
i
P
K B
(6.8)
где
К
i
– среднее значение критерия (удельный вес) при
i
,
j
= 1,
n.
По результатам анализа данных табл. 6.11 можно установить, что наи-
большее значение коэффициента риска
Р
= 0,98 имеет отказ ПЭД-45-103
и ПЭД-45-117, а наименьшее
Р
= 0,725 – ПЭД-50-117.
Для идентификации слабых мест в эксплуатации и ведении режима
произведем ранжирование составленной группы ПЭД по приоритетности
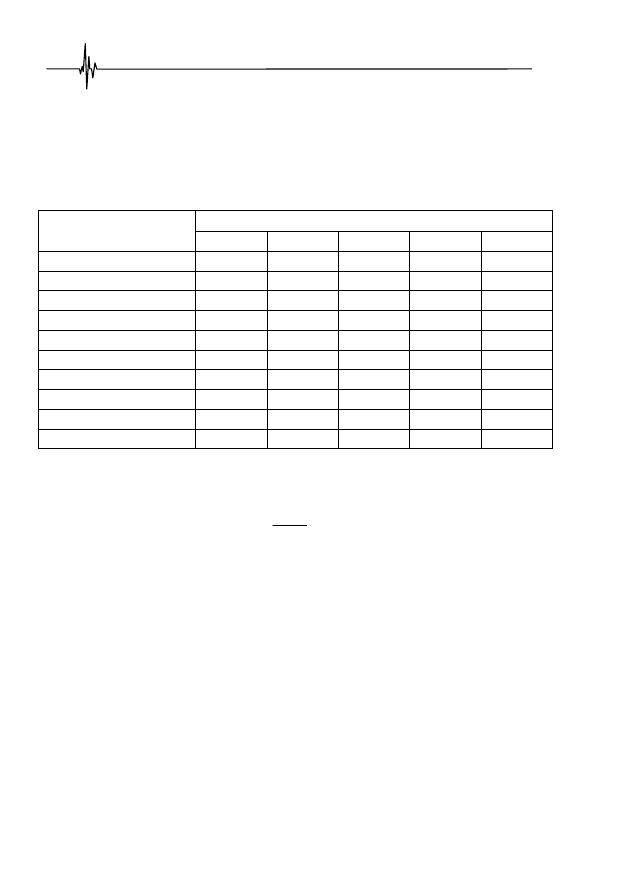
Повышение эффективности эксплуатации
погружных электроустановок нефтедобычи
174
выполнения операций ТОиР в соответствии с данными, полученными
в табл. 6.9 и 6.11. Ранги индивидуальных показателей надежности исследуе-
мой группы ПЭД представлены в табл. 6.12.
Таблица 6.12
Ранги индивидуальных показателей надежности для ПЭД
Наименование ПЭД
Показатели
Т
сл
Т
отк.ср
n
ав
t
Р
ПЭД-32-103
4
4
2
2
1
ПЭД-32-117
4
5
1
2
1
ПЭД-45-103
5
5
2
3
1
ПЭД-45-117
4
5
2
0
1
ПЭД-50-103
2
3
1
1
2
ПЭД-50-117
5
2
4
3
2
ПЭД-56-103
2
3
5
0
1
ПЭД-56-117
3
5
3
0
1
ПЭД-63-117
4
4
5
5
2
ПЭД-90-117
1
2
5
2
1
Интегральный показатель
К
приоритетности выполнения ремонтов ПЭД,
являющийся относительной суммой рангов, может быть определен в виде
1
1
,
n
j
j
K
r
n
m
(6.9)
где
r
j
– ранг
j
-го объекта;
m
– число рангов;
n
– число показателей.
Используя представленные выше интервалы значений интегрального
показателя, можно произвести ранжирование исследуемой группы ПЭД
в соответствии с расстановкой приоритетов при выполнении ТОиР с учетом
индивидуальных показателей надежности и свойств оборудования.
В соответствии с рекомендациями [93, 96, 97] для качественной оценки
надежности работы ПЭД сформирована шкала классификации с четырьмя
равными диапазонами, которая реализует следующие принципы организа-
ции ремонта и управления техническим состоянием парка ПЭД ПН:
– 0,2–0,4 ‒ необходимо внеплановое ТОиР в кратчайшие сроки;
– 0,4–0,6 ‒ необходимо внеплановое ТОиР, дополнительное диагности-
рование, повышенный контроль. Сроки ремонта определяются месячным
графиком ремонтов, а также временем аварийной готовности технологиче-
ски связанного оборудования, выведенного в ремонт;
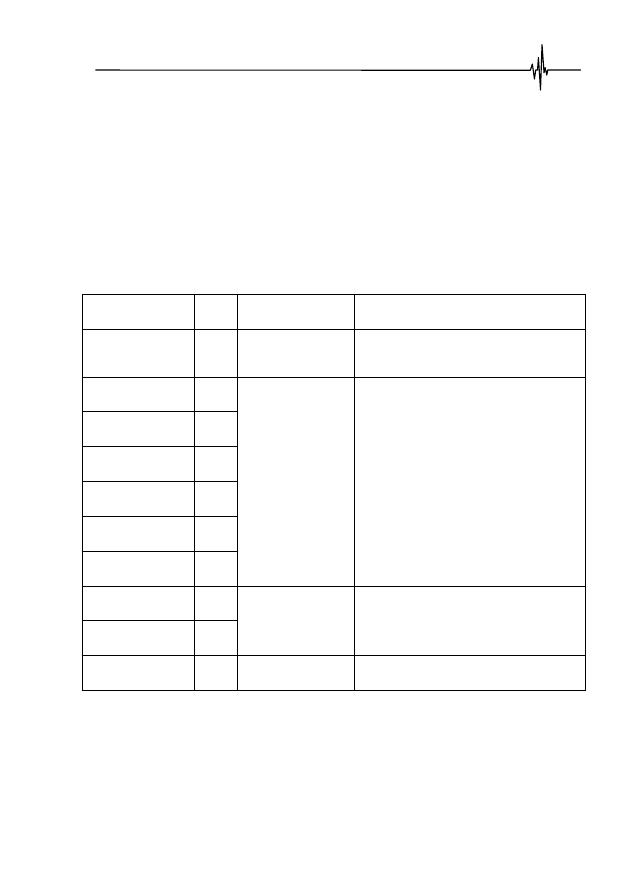
Глава 6. Оценка надежности и приоритетности ремонтов для электрооборудования
нефтяной промышленности с учетом возможного риска
175
– 0,6–0,8 ‒ внеплановый ремонт не требуется, работы проводятся
в соответствии с годовым графиком ремонтов;
– 0,8–1 ‒ показательное состояние, ремонт не требуется, возможно пла-
новое диагностирование.
Интегральные показатели
К
группы исследуемого парка ПЭД, которые
изменяются в диапазоне 0,2–1, представлены в порядке возрастания
в табл. 6.13.
Таблица 6.13
Приоритетность выполнения ремонтов группы ПЭД
в соответствии со значениями
К
интегрального показателя
Наименование
ПЭД
К
Интервалы
классификации
Рекомендации
по планированию ремонтов
ПЭД-50-103
0,36
0,2–0,4
Необходимо произвести внеплано-
вое ТОиР
в кратчайшие сроки
ПЭД-56-103
0,44
0,4–0,6
Необходимо произвести внеплано-
вое ТОиР, работы включить в ме-
сячный график ремонтов
ПЭД-90-117
0,44
ПЭД-45-117
0,48
ПЭД-56-117
0,48
ПЭД-32-103
0,52
ПЭД-32-117
0,56
ПЭД-45-103
0,64
0,6–0,8
Внеплановый ремонт не требуется,
работы можно провести
в соответствии с годовым планом
ремонтов
ПЭД-50-117
0,64
ПЭД-63-117
0,84
0,8–1
Ремонт не требуется
6.5. Выводы по главе
1.
Сформулирована и подробно представлена оригинальная методика
FMEA-анализа видов и последствий потенциальных отказов применительно
к ПН.
2.
На основе методологий В. Парето и К. Исикава сформирована
и построена диаграмма технологических нарушений в работе ПЭУ
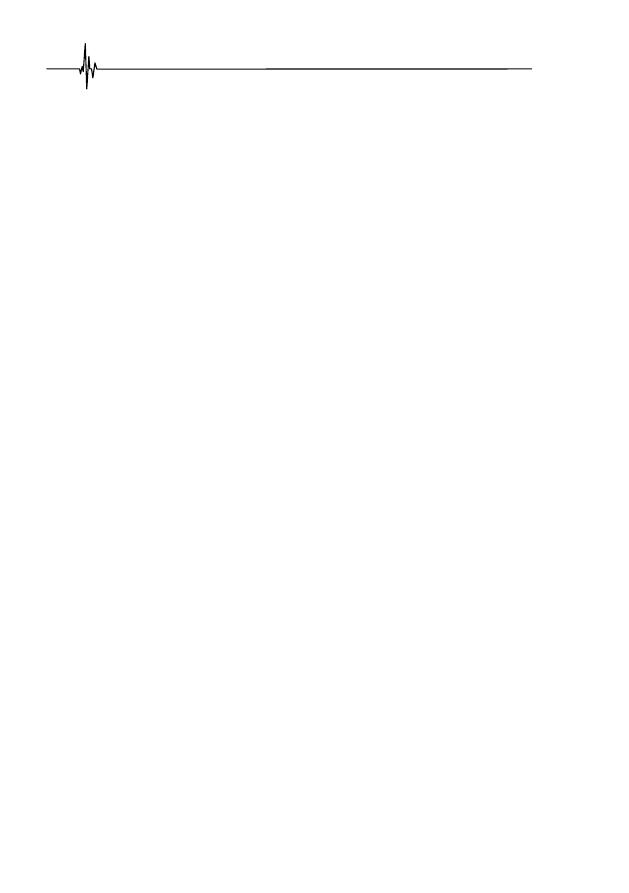
Повышение эффективности эксплуатации
погружных электроустановок нефтедобычи
176
и произведен анализ их причинно-следственной связи с подробным описа-
нием всех отказов. На основании данного анализа разработана схема мони-
торинга, посредством которого выявлены все недостатки эксплуатации
оборудования скважины и их причины, разработаны процедуры в виде кор-
ректирующих действий.
3.
На основании метода FMEA-анализа получены экспертные оценки
и рассчитано приоритетное число риска возникновения каждого отказа, позво-
ляющие дать оценку степени влияния факторов на проблему эффективности экс-
плуатации ПЭУ на основе следующих основных показателей: значимость причи-
ны, частота ее возникновения и вероятность обнаружения. Установлено, что наи-
высший риск для предприятия с
ПЧР
>>
гр
ПЧР
составляют отказы, связанные
со снижением изоляции между жилами и землей (
ПЧР
= 648 баллов), К.З. обмот-
ки ПЭД (
ПЧР
= 576 баллов) и клином УЭЦН (
ПЧР
= 336 баллов).
4.
Представлена методика по определению приоритетности планирова-
ния ремонтов ПЭУ нефтедобычи, обладающих низкими значениями показа-
телей надежности, повышенным износом и значительной степенью риска
при возможном выходе параметров ТС и режима конкретного ЭПУ (ПЭД)
за нормативные границы, установленные для возможных аварийных отказов.
5.
Разработан алгоритм комплексного анализа и учета индивидуальных по-
казателей надежности для объектов ПЭУ в интегральном показателе, позво-
ляющем адекватно учитывать возможные риски снижения параметров техниче-
ского и эксплуатационного состояния подконтрольного оборудования.
6.
Очевидная научная и практическая направленность предлагаемых
методов и алгоритмов позволяет использовать их для создания автоматизи-
рованной системы управления жизненными циклами ПЭУ, обеспечив техни-
ческих работников информационной и методической поддержкой.
Положительный технико-экономический эффект использования резуль-
татов данной работы для всего парка ЭПУ(ПЭД) ПН или его части опреде-
ляется общим повышением надежности ПЭУ, снижением простоев
в текущих и аварийных ремонтах.
Оригинал статьи: Глава шестая. Оценка надежности и приоритетности ремонтов для электрооборудования нефтяной промышленности с учетом возможного риска
6.1. Корректная организация эксплуатации ПЭУ
6.2. Причинно-следственная оценка производственных рисков эксплуатации парка ПЭУ
6.3. Методология использования FMEA-анализа для оценки вероятности возникновения производственных рисков отказов парка ПЭУ
6.4. Оценка интегральных показателей надежности ПЭУ
6.5. Выводы по главе